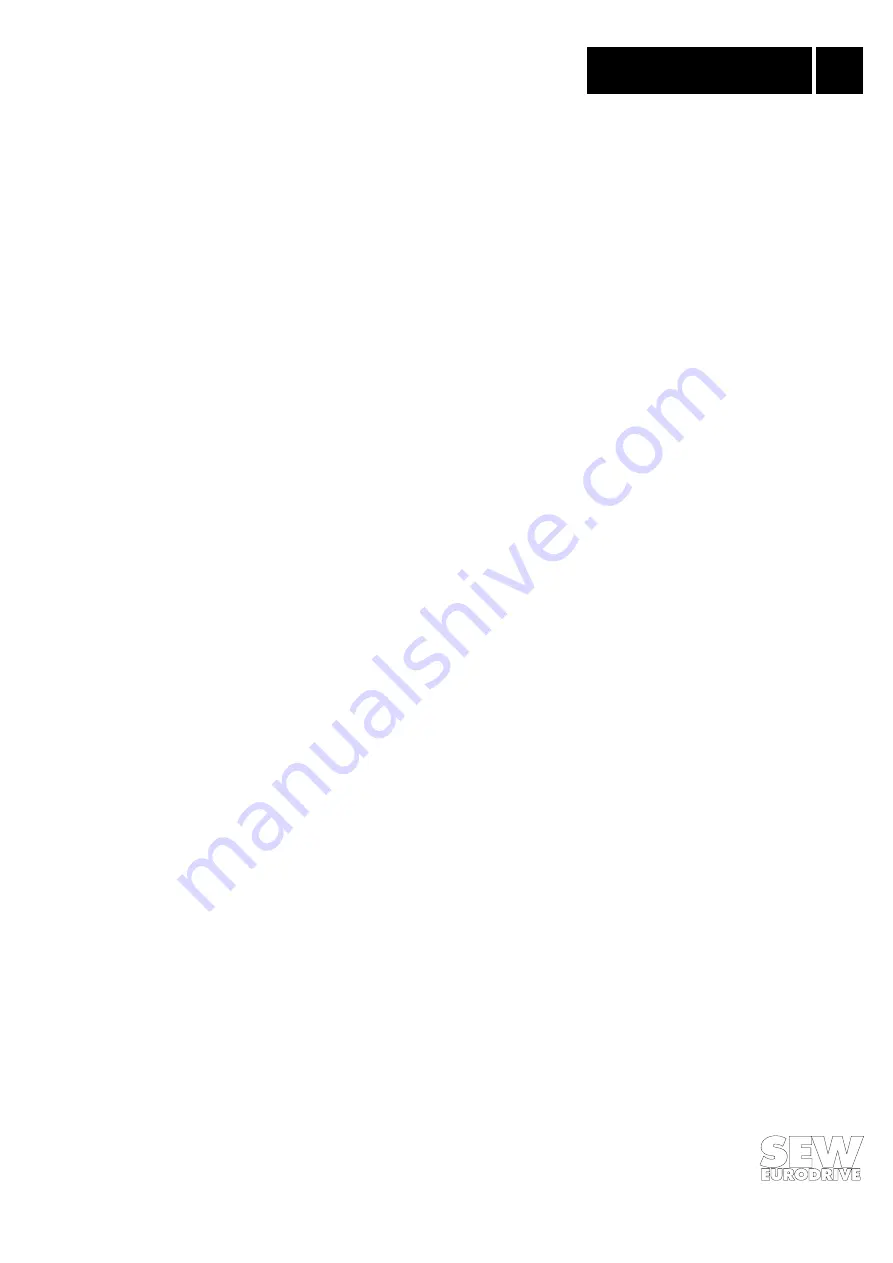
MOVIDRIVE
®
PROFIBUS DFP11A
5
Introduction
1
1
Introduction
This PROFIBUS (DFP11) Option Manual describes the procedure for installing the DFP11 PROFI-
BUS option pcb in the drive inverter and for commissioning the MOVIDRIVE
®
drive inverter when
connected to a PROFIBUS-DP or PROFIBUS-FMS fieldbus system.
In addition to describing all the settings on the fieldbus option pcb, this manual further discusses
the various options for connecting the drive inverter to PROFIBUS-DP or PROFIBUS-FMS in the
form of brief commissioning examples.
In addition to this PROFIBUS Option Manual, we recommend that you familiarize yourself with the
following more detailed documentation on fieldbuses, which will provide you with the necessary
information for simple and efficient connection of the MOVIDRIVE
®
to the PROFIBUS fieldbus
system:
• MOVIDRIVE
®
Fieldbus Unit Profile Manual
The MOVIDRIVE
®
Fieldbus Unit Profile Manual gives a detailed description of the fieldbus parame-
ters and their codes and discusses various control concepts and potential applications in the form
of brief examples.
The MOVIDRIVE
®
Fieldbus Unit Profile Manual also contains the parameter list which is sorted in
the order of the parameter numbers.
Thanks to this high-performance, universal fieldbus interface, the MOVIDRIVE
®
drive inverter with
the DFP11 option can be connected to and controlled from higher-level automation systems via
PROFIBUS-FMS and PROFIBUS-DP.
MOVIDRIVE
®
= Combislave
With the DFP11 PROFIBUS option pcb the MOVIDRIVE
®
drive inverter as Combislave unit supports
both PROFIBUS-FMS and PROFIBUS-DP to DIN E 19245 Part 3 / EN 50170. This allows the drive
inverter to be controlled via PLC and PROFIBUS-DP, for example, while at the same time a visuali-
zation system can read out and display on a PC screen actual values from the drive inverter using
PROFIBUS-FMS. Of course the drive inverter may be controlled and parameterized using only
PROFIBUS-DP or only PROFIBUS-FMS, too.
MOVIDRIVE
®
and PROFIBUS
The drive inverter device profile for PROFIBUS mode, for example the way the drive inverter
operates and responds when in PROFIBUS mode, is independent of the type of fieldbus, and thus
consistent for all fieldbus types. This allows the user to develop his drive applications independent
of a particular fieldbus or change to another bus system, e.g. INTERBUS (DFI 11 option) without
any problems.
MOVIDRIVE
®
offers digital access to all drive parameters and functions via the PROFIBUS inter-
face. The drive inverter is controlled by the high-speed cyclic process data. This process data chan-
nel provides the facility to specify setpoints, such as setpoint speeds, ramp generator times for
acceleration and deceleration etc., as well as various drive functions such as enable, controller
inhibit, stop, rapid stop, etc. to be triggered. This channel can also be used to read back actual
values from the drive inverter, such as actual speed, current, inverter status, fault number or refer-
ence messages.
Whereas process data are generally exchanged in cycles, the drive parameters can be read and
written acyclically via the READ and WRITE services or the parameter channel. This exchange of
parameter data enables applications where all major drive parameters are stored in the higher-level
automation unit to be implemented, thus avoiding manual adjustment of parameters on the drive
inverter itself.