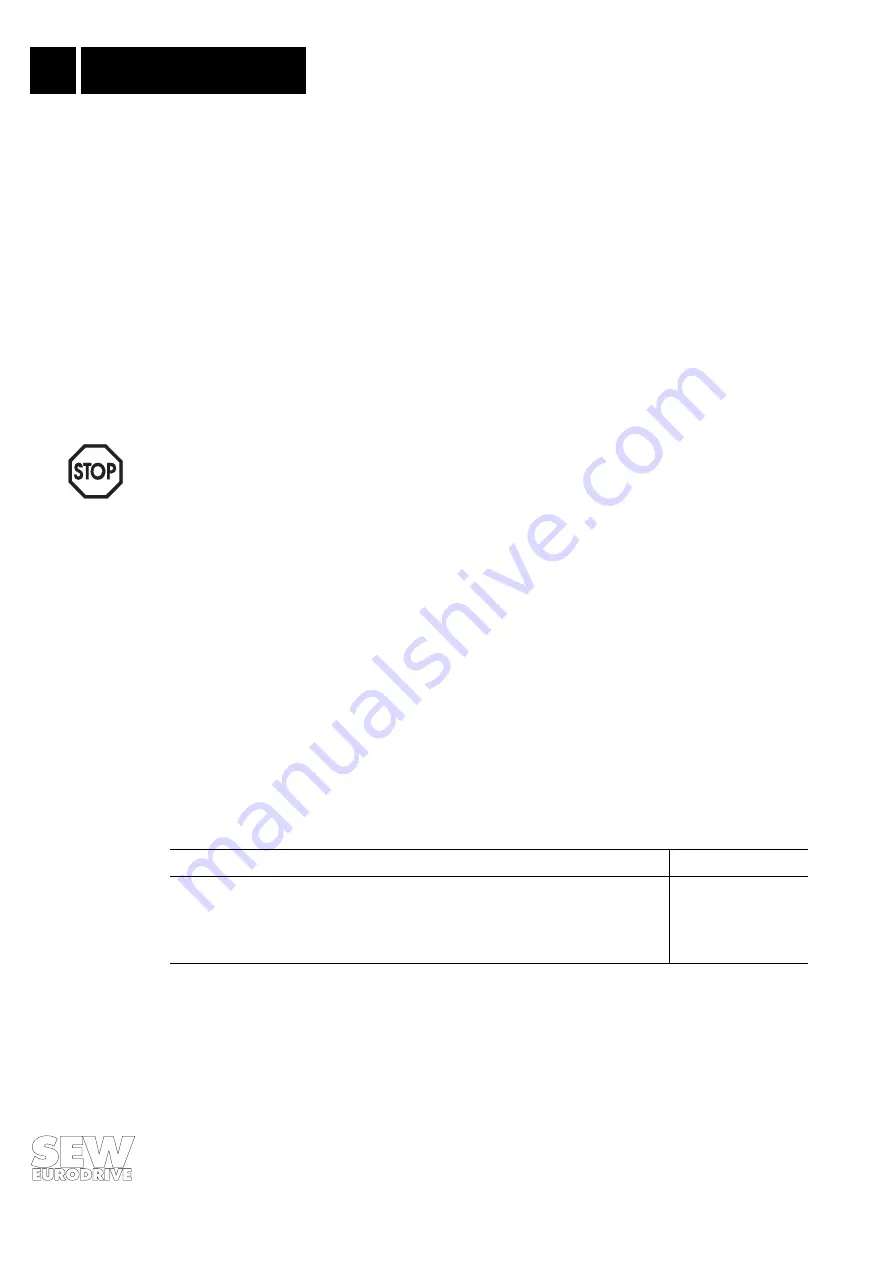
6
DFS/DFY Synchronous Motors
2
Installation/Assembly
Check the terminal box/connector to ensure that:
– the inside is clean and dry
– connection and mounting components are free of corrosion
– joint seals are in order
– screwed cable glands are tight.
if not, clean or replace them.
2.3
Installing the motor
The motor or geared motor may be only be mounted or installed in the specified mounting position
on a level, vibration-free and torsionally rigid support structure.
• Thoroughly remove anti-corrosion agents from the shaft ends and flange (use a standard
solvent). Do not allow the solvent to penetrate the bearings and oil seals - this could cause
material damage.
• Carefully align the motor and the driven machine to avoid placing any unacceptable strain on the
motor shafts (observe permissible overhung loads and axial thrusts).
• Avoid thrusts and blows on the shaft ends.
• Protect motors in a vertical mounting position with a VY forced cooling fan with a suitable
cover against the ingress of foreign matter and liquid!
• Ensure an unobstructed cooling air supply.
• Balance components for subsequent mounting on the shaft without key.
• The surface temperature of the motor may exceed 65 °C when in operation. Therefore
appropriate measures must be taken to safeguard against accidental contact.
2.3.1 Installation in damp areas or in the open air
• Mount the terminal box so that the cable entries point downwards if possible.
• Use suitable screwed cable glands for the supply lead (use reducing adapters if necessary).
• Coat the threads of screwed cable glands and sealing plugs with sealing compound and tighten
them well, then coat them again.
• Seal the cable entries well.
• Clean the sealing faces of terminal boxes and their covers well before reassembly; gaskets must
be cemented in on one side. Replace brittle gaskets.
• Restore the anticorrosive coating if necessary.
• Check the type of enclosure.
2.4
Tolerances
→
“Servo Geared Motors” catalog, Sec. “Notes on Dimension Sheets”
Shaft ends
Flanges
Diametric tolerances
– ISO k6 for
≤
50 mm
– ISO m6 for > 50 mm
(Centring hole to DIN 332, shape DR.. . Use centring hole for mounting transmission
elements to prevent damage to the anti-friction bearings.)
Centring shoulder
tolerance
– ISO j6 for
≤
230 mm
– ISO h6 for > 230 mm
Содержание DFS 56L/B
Страница 1: ...14 004 92 T DFS DFY Synchronous Motors Operating Instructions Edition 02 2000 0919 9519 0200...
Страница 34: ......
Страница 35: ......