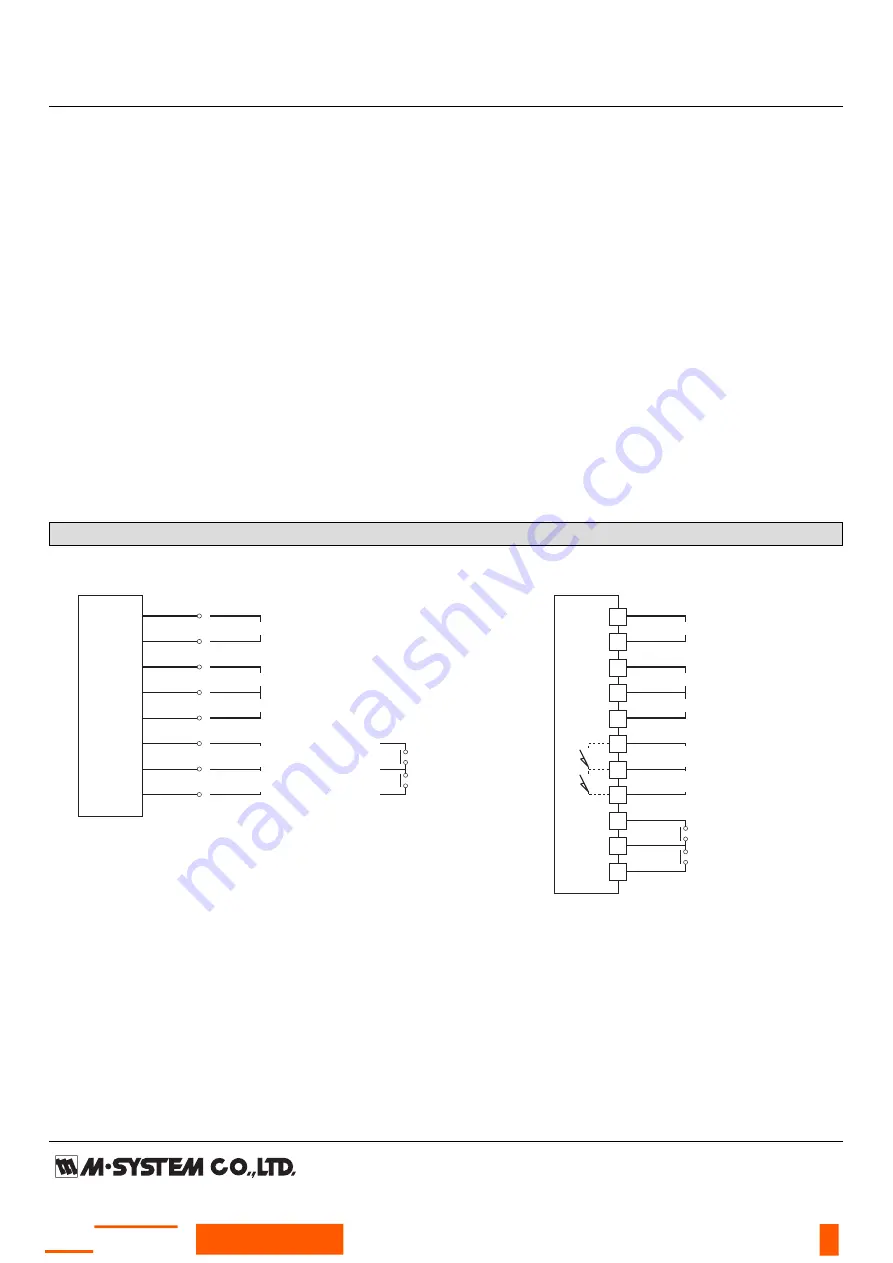
MODEL: MRP6
When an overload is detected, the Mini-Top stops supplying
power to the motor and the status LED blinks in 0.5 sec.
intervals.
The protection is reset automatically with applying opposite-
direction input signal or turning the power off and
restarting.
• Restarting Timer
The Mini-Top Series is equipped with a timer circuit which
gives an interval period (0 – 10 seconds) between stop-
restart actions to prevent the motor and other internal
components from overheating.
It is recommended to set a long restarting time when the
ambient temperature and/or the temperature of flow
material is high.
• Electronic Limiter
This model is equipped with electronic limiters in order to
prevent mechanical locks when the input goes below 0 % or
above 100 %.
Limiters are set at approx. -0.5 % for the full-closed side,
approx. 100.5 % for the full-open side.
TERMINAL CONNECTIONS
black (1)
+
(U)
–
(V)
+
COM1
+
COM2
white (2)
red (3)
green (4)
yellow (5)
blue (6)
gray (7)
brown (8)
(1) to (8): Terminal No. of terminal box.
Full-open/-closed signals and forced open/close signals are optional.
POWER
INPUT
POSITION OUTPUT (1 – 5V DC)
FULL-OPEN or
FULL-CLOSED
SIGNAL
(
output stem
)
turned CCW
(
output stem
)
turned CW
+
(U)
–
(V)
+
COM1
+
COM2
COM1
POWER
INPUT
POSITION OUTPUT (1 – 5V DC)
FULL-OPEN or
FULL-CLOSED
SIGNAL
(
output stem
)
turned CCW
(
output stem
)
turned CW
COM1
FORCED
OPEN/CLOSE
SIGNAL
FORCED
OPEN/
CLOSE
SIGNAL
(
output stem
)
turn CCW
(
output stem
)
turn CW
(
output stem
)
turn CCW
(
output stem
)
turn CW
1
3
2
4
6
5
7
8
11
9
10
• With Both Full-open/closed Signal
and Forced Open/Close Signal
Rugghölzli 2
CH - 5453 Busslingen
Tel. +41 (0)56 222 38 18
Fax +41 (0)56 222 10 12
www.sentronic.com
Produkte, Support und Service
SENTRONIC
AG