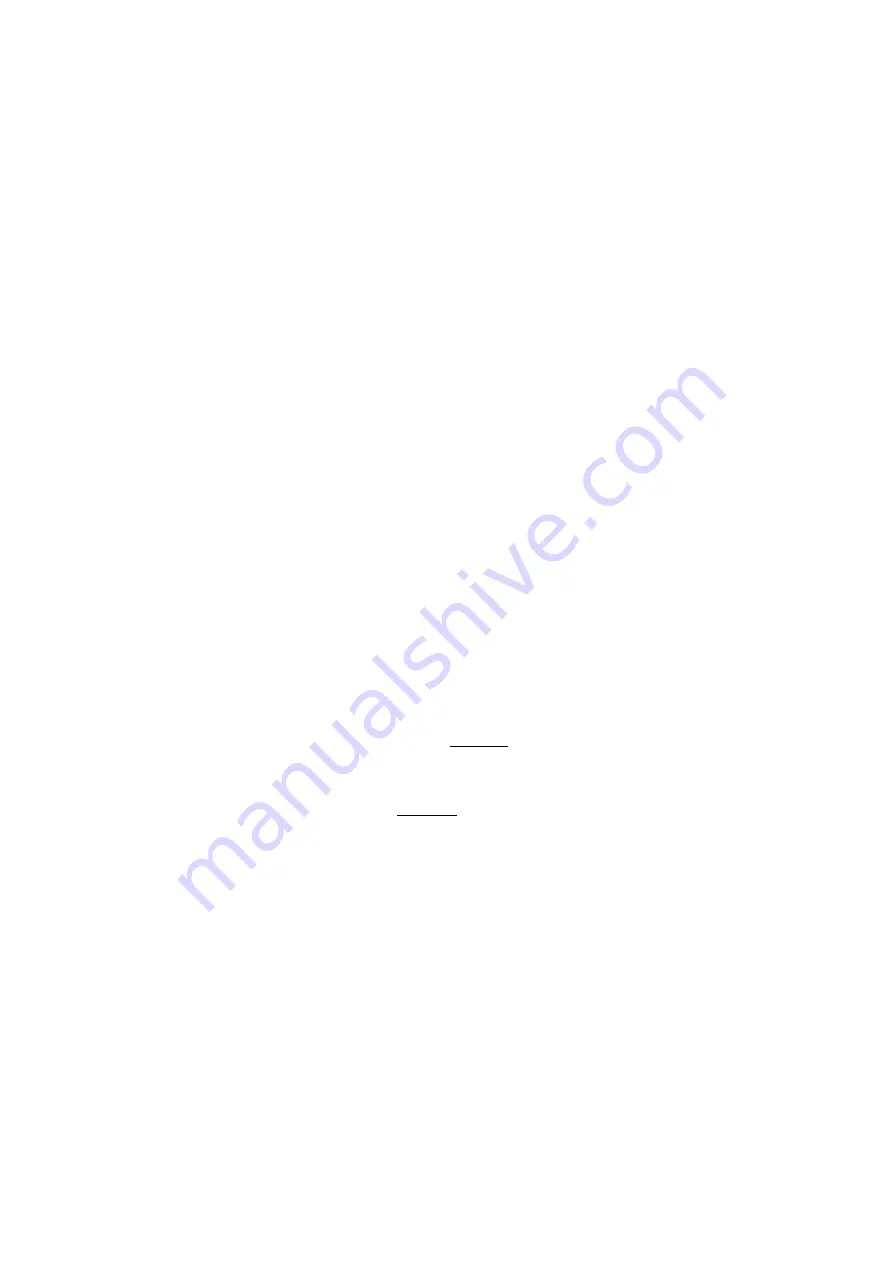
Sensor Technology 2016
Page 5
RWT3745V (Rev 2)
Whilst the transducer is resistant to EMC interference to BS EN 61326-1:2006, the
sensible routing of cables is important to avoid possible EMC interference. Avoid
running the transducer cables close, and/or parallel, to high voltage cables, solenoid
valves, generators or inverters etc. If the cables must follow the same route as
interfering cables then additional screening such as metal conduit should be used to
provide isolation.
To avoid damaging the transducer during installation it is highly recommended that
it is electrically connected and working during this process so that any torque
overloads due to handling can be monitored.
Operating Principles
The shaft of the transducer should be connected to the mechanical system on which the
measurements are to be made using appropriate couplings so it can rotate freely up to its
maximum recommended speed, with relation to the transducers body and bearings fitted.
Torque applied to the shaft causes an angular deflection in the shaft (approximately 0.5
degree at maximum rated torque). This deflection is sensed by two Surface Acoustic Wave
devices, resulting in a change to their resonant frequency. It is this change, which is
processed to provide a torque reading.
The RWT series transducers can sense both polarity output signals. Torque applied in the
clockwise sense along the transducer shaft axis produces a positive polarity output signal
while torque applied in the anticlockwise sense produces a negative polarity output signal.
If an optical rotary speed sensor is fitted, a light beam is interrupted by the rotation of a disc
consisting of alternate opaque and translucent segments attached to the shaft. Both 60 line
and 360 line encoders are available.
The thermal characteristics of the steel shaft are compensated by having an infrared
temperature sensor monitoring the shaft temperature at all times. This information is then
used to correct the modulus of the steel.
Pre-load, note:
All RWT410/420
transducers with a LED in the centre of the front label (connector side) have
a bearing pre-load spring fitted internally at the left hand side (pre-load end) when viewing the
front label of the transducer and with the earth stud bottom ride hand corner.
All RWT430/440
transducers with a LED on the separate electronics module have a bearing
pre-load spring fitted internally at the left hand side (pre-load end) of the transducer head
when viewing the label of the transducer head and the connector and gland facing towards
you.
If there is a possibility of an end load being applied to the transducer, the transducer
should be orientated during installation such that the load is applied at the pre-load
end (side with the internally fitted spring). Excessive end loads must be avoided and it
is recommended that appropriate couplings be used to compensate for axial and radial
misalignment.
Содержание RWT420
Страница 23: ......
Страница 31: ...Transducer Control 5 User Manual Revision 5 December 2016...