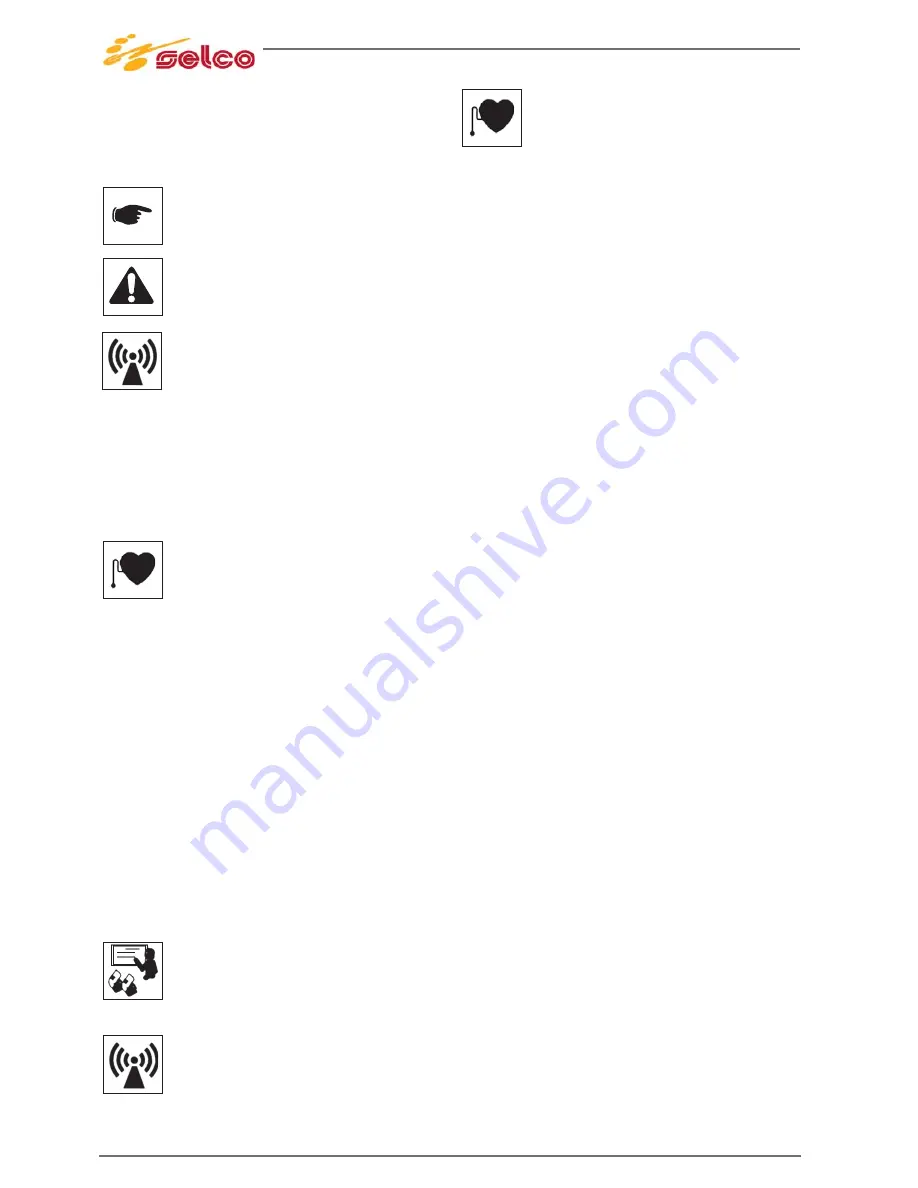
42
• Ensure the system is connected correctly to a socket and a
power source equipped with an earth conductor.
• Do not touch two torches or two electrode holders at the
same time.
lf you feel an electric shock, interrupt the welding (cutting)
operations immediately.
The arc striking and stabilizing device is designed
for manual or mechanically guided operation.
Increasing the length of torch or welding cables
more than 8 m will increase the risk of electric
shock.
1.7 Electromagnetic fields &
interferences
• The welding current passing through the internal and external
system cables creates an electromagnetic field in the proxim-
ity of the welding cables and the equipment itself.
• Electromagnetic fields can affect the health of people who
are exposed to them for a long time (the exact effects are still
unknown).
Electromagnetic fields can interfere with some equipment like
pacemakers or hearing aids.
Persons fitted with pacemakers must consult their
doctor before undertaking arc welding or plasma
cutting operations.
EMC equipment classification in accordance with EN/IEC
60974-10
(See rating plate or technical data)
Class B equipment complies with electromagnetic compatibility
requirements in industrial and residential environments, includ-
ing residential locations where the electrical power is provided
by the public low-voltage supply system.
Class A equipment is not intended for use in residential locations
where the electrical power is provided by the public low-voltage
supply system. There may be potential difficulties in ensuring
electromagnetic compatibility of class A equipment in those
locations, due to conducted as well as radiated disturbances.
Installation, use and area examination
This equipment is manufactured in compliance with the
requirements of the EN60974-10 harmonized standard and is
identified as "CLASS A" equipment.
This unit must be used for professional applications only, in
industrial environments.
The manufacturer will accept no responsability for any damages
caused by use in domestic environments.
The user must be an expert in the activity and as such
is responsible for installation and use of the equip-
ment according to the manufacturer's instructions.
lf any electromagnetic interference is noticed, the
user must solve the problem, if necessary with the
manufacturer's technical assistance.
In any case electromagnetic interference problems
must be reduced until they are not a nuisance any
longer.
Before installing this apparatus, the user must evalu-
ate the potential electromagnetic problems that
may arise in the surrounding area, considering in
particular the health conditions of the persons in
the vicinity, for example of persons fitted with pace-
makers or hearing aids.
Mains power supply requirements
(See technical data)
High power equipment may, due to the primary current drawn
form the mains supply, influence the power quality of the grid.
Therefore connection restrictions or requirements regarding the
maximum permissible mains impedance (Zmax) or the required
minimum supply capacity (Ssc) at he interface point to the pub-
lic grid (point of common coupling, PCC) may apply for some
types of equipment (see technical data).
In this case it is the responsibility of the installer or user of the
equipment to ensure, by consultation with the distribution
network operator if necessary, that the equipment may be con-
nected.
In case of interference, it may be necessary to take further pre-
cautions like the filtering of the mains power supply.
lt is also necessary to consider the possibility of shielding the
power supply cable.
Welding and cutting cables
To minimise the effects of electromagnetic fields follow the fol-
lowing instructions:
- Where possible, collect and secure the earth and power
cables together.
- Never coil the welding cables around your body.
- Do not place your body in between the earth and power
cables (keep both on the same side).
- The cables must be kept as short as possible, positioned as
close as possible to each other and laid at or approximately
at ground level.
- Position the equipment at some distance from the welding
area.
- The cables must be kept away from any other cables.
Earthing connection
The earth connection of all the metal components in the weld-
ing (cutting) equipment and in the close aerea must be taken in
consideration.
The earthing connection must be made according to the local
regulations.
Earthing the workpiece
When the workpiece is not earthed for electrical safety reasons
or due to its size and position, the earthing of the workpiece
may reduce the emissions. It is important to remember that the
earthing of the workpiece should neither increase the risk of
accidents for the user nor damage other electric equipment.
The earthing must be made according to the local regulations.
Shielding
The selective shielding of other cables and equipment present
in the surrounding area may reduce the problems due to elec-
tromagnetic interference. The shielding of the entire welding
(cutting) equipment can be taken in considered for special
applications.
Содержание Genesis 2200 PMC
Страница 1: ...Genesis 2200 PMC MANUALE DI RIPARAZIONE REPAIR MANUAL...
Страница 38: ...74...
Страница 41: ...77 16 SCHEMI ELETTRICI E DI COLLEGAMENTO WIRING DIAGRAMS AND CONNECTION...
Страница 42: ...78 17 CONNETTORI CONNECTORS...
Страница 43: ...79...
Страница 44: ...80 18 LISTA RICAMBI SPARE PARTS LIST 55 05 010 GENESIS 2200 PMC 1x230V...
Страница 47: ...83...
Страница 48: ...84 07 01 600 SL 4R 4T 11A 11B 11C 22...
Страница 50: ...86 19 INSTALLAZIONE KIT ACCESSORI INSTALLATION KIT ACCESSORIES 73 11 014 Kit Push Pull...
Страница 51: ...87...
Страница 52: ...88 STANDARD U D VERSION OPTIONAL PUSH PULL VERSION...
Страница 53: ...89...
Страница 54: ...90 MODULO RICAMBI...