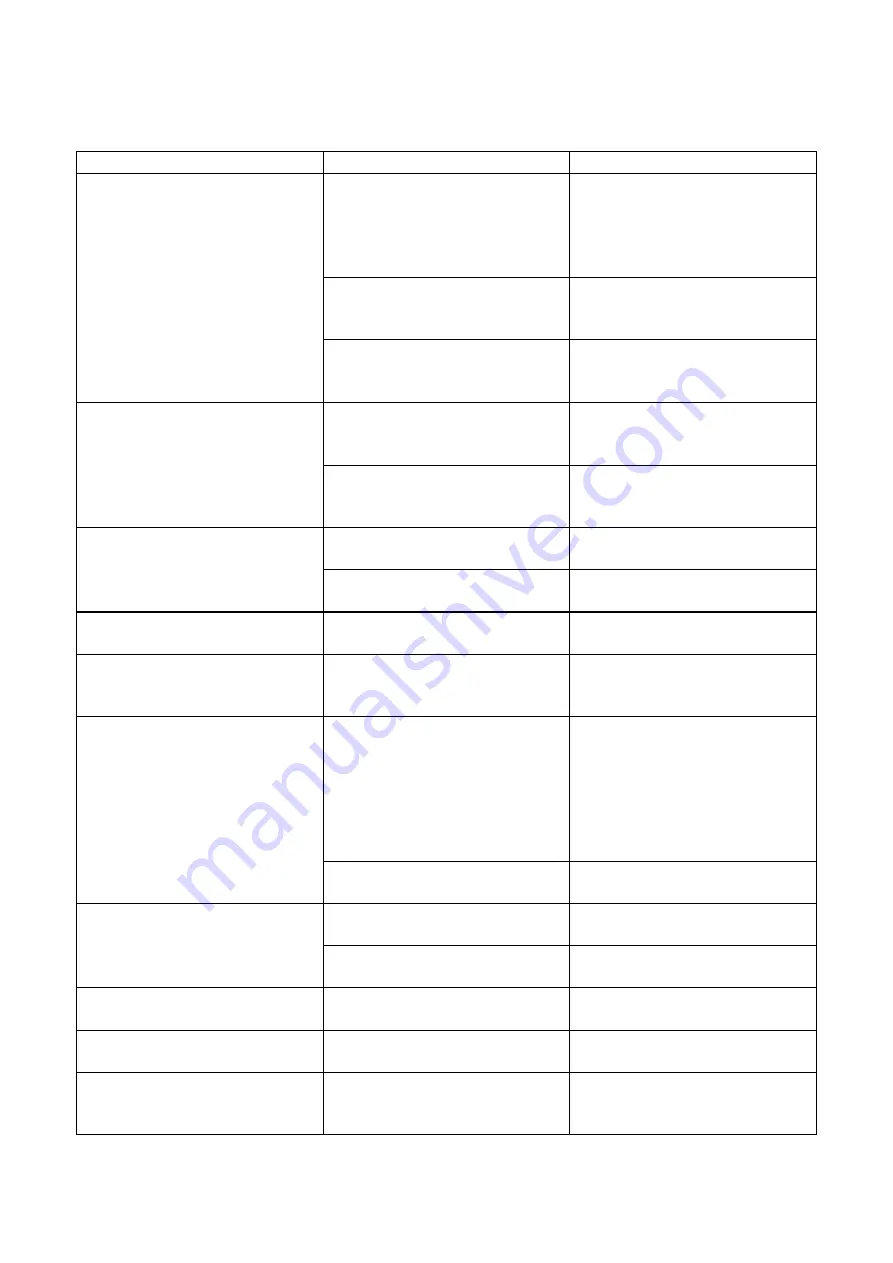
25
11.0 Diagnosing Faults
All faults should be reported as soon as they are discovered.
Fault
Cause
Diagnosis
The timber rocks, and the
edge is rounded in length
after being surfaced.
The cutters are out of
alignment with the table.
Re-set the cutters and check
the edge for straightness,
wear or maladjustment of the
slides on the table.
Chippings lie between the
timber and table.
Isolate the machine and clear
the chippings.
The timber is placed round-
edge down.
Place the timber hollow edge
down.
Uneven finish.
Dull cutters causing chatter
marks on the timber.
Re-sharpen the cutters.
An uneven feed rate.
Feed the timber into the
cutters at the correct rate.
A
pronounced
cuttermark
pattern.
Too fast a feed rate.
Reduce the feed rate.
One knife is set higher than
the other
Re-set the cutters.
An unplaned line is left on an
otherwise smooth finish
Chipped cutter
Replace the cutters.
The timber ‘drops’ at the end
of the cut and gouges out the
end of the timber.
The knives are too high above
the cutterblock.
Re-set the cutters.
Excessive vibration causing a
poor finish.
Unbalanced cutters or block.
Check the balance of the
cutters on a balancing stand,
and grind the heavier one so
as to balance correctly. Run
the block without cutters to
see if it still vibrates.
Worn bearings.
Renew the bearings.
The edge of the timber is not
square to the face.
The fence is not square.
Adjust the fence square to the
table.
The cutters are out of line
with the table.
Re-adjust the cutters.
Timber hits the outfeed table
Knives are too low in the
cutterblock.
Re-set the cutters
Timber
becomes
wedge
shaped over full length.
Knives are too low in the
cutterblock.
Re-set the cutters.
End snipe when thicknessing
End of timber is not being
held down against the table
by the outfeed roller.
Adjust roller setttings. For
long boards, use an auxiliary
table on the thicknessing bed.
Содержание PT255
Страница 36: ...36 14 0 PT255 Planer Thicknesser Parts Diagram ...
Страница 39: ...39 ...
Страница 40: ...40 ...