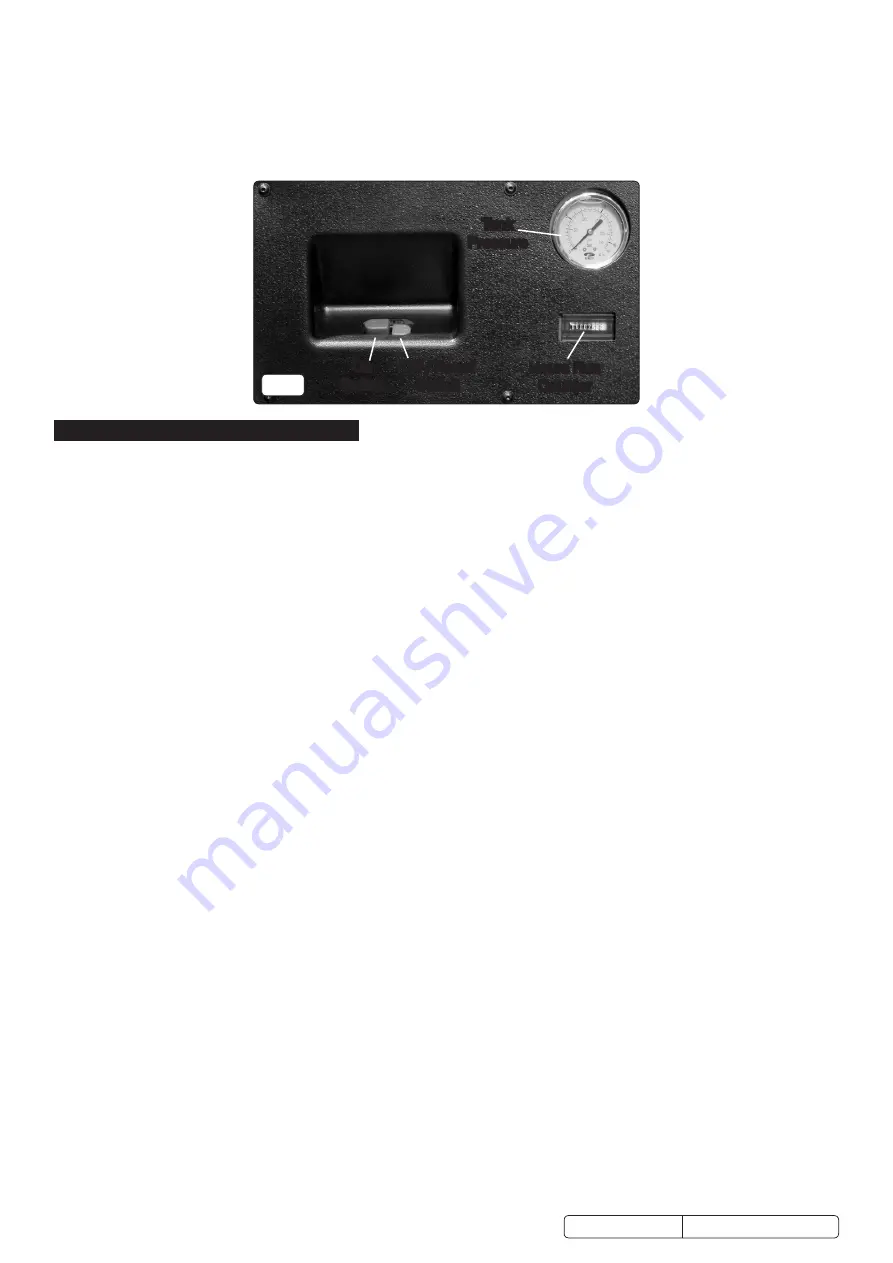
the restart easier and preventing the motor from being damaged.
DO NOT,
other than in an emergency
,
stop the compressor by switching
off the mains power, or by pulling the plug out, as the pressure relief will not then operate and motor damage may result upon restart.
5.1.4.
The motor of the compressor is fitted with a thermal breaker. The manual resetting button is doubled up with the “OFF” button (fig.6).
When the breaker is tripped, wait for a few minutes and then press the reset button. If the unit keeps tripping investigate and rectify the
cause.
NOTE:
If the motor does not cut in and out, but runs continuously when using an air appliance, the capacity of the compressor may be
too small for the equipment or tool.
WARNING!
DO NOT
tamper with, or adjust, the switch or safety valve.
6. MAINTENANCE
6.1.
In order to keep the compressor in good working condition, periodic maintenance is essential.
IMPORTANT!
Failure to carry out maintenance tasks may invalidate the warranty on your compressor.
Inspection of pressure tank both inside and out. Under the Pressure Systems Safety Regulations 2000 it is the responsibility of the
owner of the compressor to initiate a system of inspection that both defines the frequency of the inspection and appoints a person who
has specific responsibility for carrying out the inspection.
WARNING!
Before performing any maintenance operation, switch off the compressor, disconnect from electricity supply and release
all air from the tank.
NOTE!
To gain access to the pump and motor you must remove the 4 bolts from the top lid of the sound proof casing. For some servicing
such as draining oil, you must also remove the rear panel by removing the 4 bolts.
8
DO NOT
operate the compressor without the panels fitted.
6.1.1.
OPERATIONS TO BE CARRIED OUT AFTER THE FIRST 50 WORKING HOURS:
a) Check that all bolts/nuts are tight, particularly those retaining the crankcase and cylinder head.
b) Replace the lubricating oil.
6.1.2.
OPERATIONS TO BE CARRIED OUT WEEKLY:
a) Drain condensation by opening the valve located under the tank (fig.8). Place a container under the valve and open the valve by
turning anti-clockwise.
WARNING!
Take care if there is still pressure inside the cylinder as water could flow out with considerable force. Recommended
pressure 1 - 2bar max.
b) Check oil level and, if necessary, top up.
6.1.3.
OPERATIONS TO BE CARRIED OUT EVERY 50 - 100 HOURS: (or more frequently, if the compressor operates in a very
dusty atmosphere):
a) Remove the air filter element (fig.7). Using stored air from the compressor’s tank, clean the filter with compressed air.
(Wear eye protection and
DO NOT
direct air towards the body or hands).
DO NOT
operate the compressor without the filter as foreign
bodies or dust could seriously damage the pump. Replace the filter element and air filter housing.
b)
Check for oil leaks.
c)
Check the automatic cut-out at max. pressure and the automatic cut-in at 2bar below.
6.1.4.
OPERATIONS TO BE CARRIED OUT EVERY 400 - 500 HOURS DEPENDING ON CONDITIONS (IF THE COMPRESSOR
OPERATES IN A DUSTY OR HARSH ATMOSPHERE USE 400 HOURS)
a)
Replace the lubricating oil. For oil specifications see 6.2.
Remove the filler/breather plug (see fig.4-B) then open oil drain tap, draining the oil into a container. Drain when the
compressor is hot so that the oil drains rapidly and completely. Replace oil drain plug and refill through the filler/ breather
aperture.
DO NOT
overfill. Check sight glass for correct level. Replace plug.
WARNING!
Never mix different oils and
DO NOT
use non-detergent/low quality oils as the compressor may be damaged.
WARNING!
Dispose of waste oil only in accordance with local authority requirements.
b)
Replace air filter. (See fig.7)
c)
Check all tube fittings and electrical connections.
d)
Inspect pressure tank inside and out for damage or corrosion.
6.2.
RECOMMENDED OILS
Synthetic oil suitable for temperatures ranging from -5°C to 45°C: viscosity 5W50. We
DO NOT
recommend using mineral oil in this
compressor.
Part No. Qty
Description
FSO1
1ltr x 12 Compressor oil fully synthetic
FSO1S 1ltr x 1 Compressor oil fully synthetic
FSO5
5ltr x 1 Compressor oil fully synthetic
fig.6
On
Switch
Hours Run
Counter
Tank
Pressure
Off / Reset
Switch
SAC2203BLN.V2 Issue 2 (H, 3, F) 09/07/18
Original Language Version
© Jack Sealey Limited