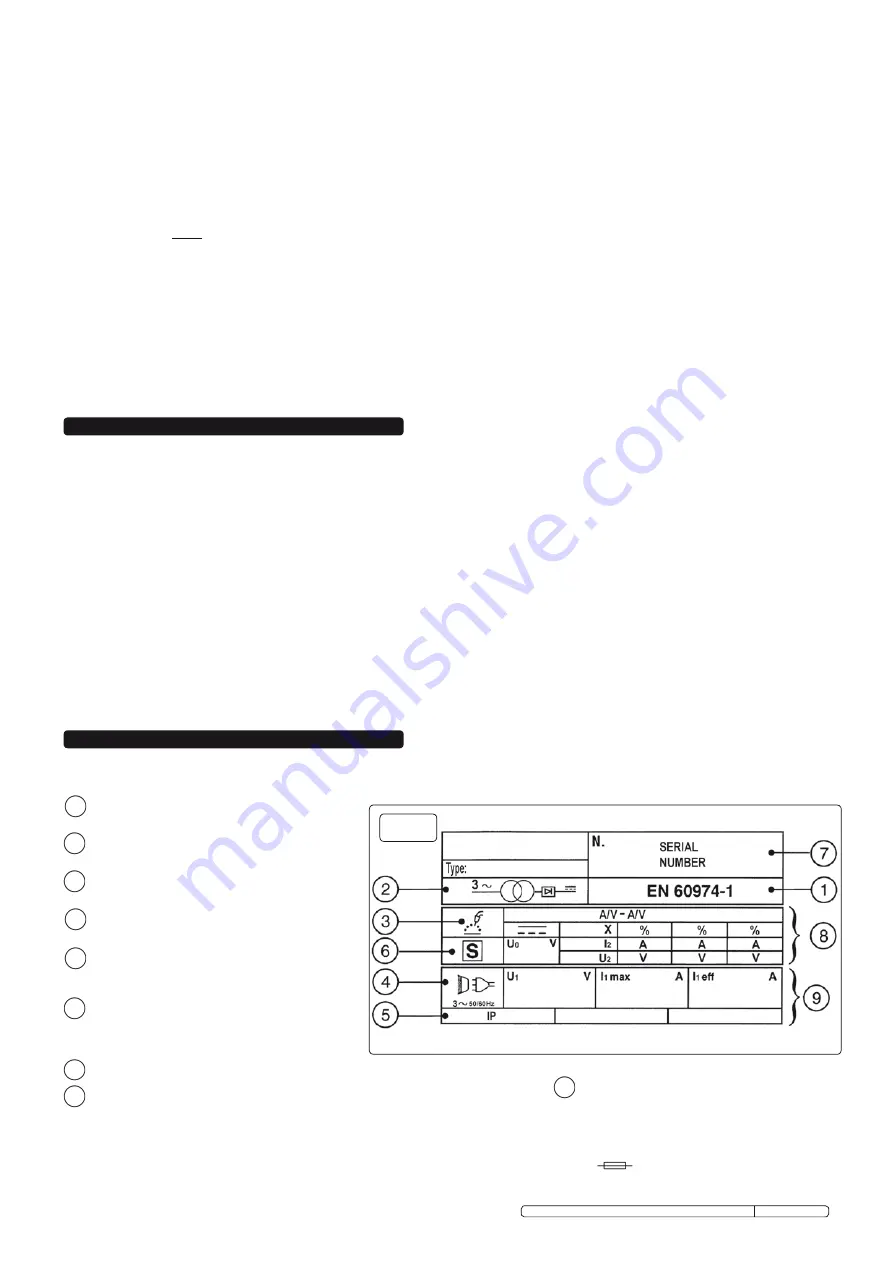
2. INTRODUCTION & SPECIFICATIONS
IMPORTANT: These instructions contain information you require to prepare your machine for welding, together with maintenance and a trouble shooting section.
If you have no previous experience the instructions are not intended to show you how to become a welder. Should you have no experience, we recommend that you
seek training from an expert source. Mig welding is relatively easy to perform, but does require a steady hand and time practising under supervision with scrap
metal as it is only with continued practice that you will achieve the desired results.
Tried and trusted by fabricators and professional car repair shops across the UK. Superb quality, Swedish made electronic wire drive motors and heavy-duty
transformers make these machines unmatched in performance and value. Our three top of the range 3ph units, are covered by the Sealey 12 month
warranty plus an additional 24 months on the main transformer. Each unit comes with 0.8mm steel wire, non- live torch and industrial Argon/CO2 regulator. All
can be used with CO2, Argon or CO2/Argon mix and accept any bottle size. Gas bottles not included.
DO NOT touch the torch or workpiece immediately after welding as they will be very hot. Allow to cool.
DO NOT operate welder while under the influence of drugs, alcohol or intoxicating medication, or if fatigued.
When not in use store the welder in a safe, dry, childproof area.
DO NOT operate welder in damp or wet places and do not weld in the rain.
Provide adequate ventilation or facilities for the removal for of welding fumes from near the arc. The risk should be assessed by a Health and Safety
professional in relation to the exposure limits for the welding fumes, which will depend on their composition, concentration and the exposure time
VOLTAGE BETWEEN ELECTORDE HOLDERS OR TORCHES.
Working with more than one welding machine on a single piece or on pieces that are connected electrically may generate a dangerous amount of no-load
voltage between the two electrode holders or torches, the value of which may reach double the allowed limit. Measuring instruments should be used to
determine the existence of a risk and suitable precautions taken as detailed in section 5.9 of the IEC TECHNICAL SPECIFICATION OF CLC/TS 62081.
1.4
ELECTROMAGNETIC INTERFERENCE.
The electromagnetic fields generated by the welding process may interfere with the operation of electrical and electronic equipment. Users of vital electronic
and electrical devices such as pacemakers and respirators are advised not to remain in the viscinity of an operating welding machine. If in doubt seek
medical advice before entering a welding area. Users of such devices should not operate the welding machine. This welder complies with the requirements
of the technical standard for the use of this type of product, only and exclusively in industrial environments and for professional purposes. It is not
guaranteed to meet electronic compatibility requirements in the home.
1.5
GAS SAFETY
Store gas cylinders in a vertical position only and ensure the storage area is correctly secured.
DO NOT store gas cylinders in areas where temperature exceeds 50°C. DO NOT use direct heat on a cylinder. Always keep gas cylinders cool.
DO NOT attempt to repair or modify any part of a gas cylinder or valve, and DO NOT puncture or damage a cylinder.
DO NOT obscure or remove any official labels from a cylinder. Always check the gas identity before use. Avoid getting gas cylinders oily or greasy.
DO NOT try to lift or handle cylinder by its cap, guard or valve. Always keep caps and guards in place and close valve when not in use.
The gas cylinder is heavy, use mechanical lifting equipment. Ensure the cylinder is correctly situated on the welder base stand and secured with chain.
1.6
RISK ASSESSMENT
Where welding is unavoidable in awkward situations such as in confined spaces, in environments with increased risk of electic shock, and in the presence of
inflamable or explosive materials, a risk assessment must be carried out by an experienced and qualified expert professional in consultation with providers of
emergency services to ensure that operations are carried out in the safest possible way.
Model
: . . . . . . . . . . . . . . . . . . . . . . . .
POWERMIG2750
. . . . . . . . . . . . . . . . . . . . . . . . . . .
POWERMIG3500
. . . . . . . . . . . . . . . . . . . . . . . . . .
POWERMIG4500
Current adjustment
. . . 10 level rotary power selection. . . . . . . . . . . . . . . . . 12 level rotary power selection. . . . . . . . . . . . . . . . 18 level rotary power selection.
Output
Range
: . . . . . . . . . . . . . . . . . . . . . .35-275 Amps . . . . . . . . . . . . . . . . . . . . . . . . . . . . . . . 35-350 Amps . . . . . . . . . . . . . . . . . . . . . . . . . . . . . .35-450 Amps
Duty
Cycle
: . . . . . . . . . . . . 10% @ 260A, 30% @ 240A . . . . . . .10% @ 330A, 15% @ 320A, 25% @ 300A, . . . . . 10% @ 430A, 15% @ 420A, 25% @ 400A,
. . . . . . . . . . . . . . . . . . . . . 60% @ 160A,100% @ 130A . . . . . . . . . . . . . . . . . . .60% @ 200A, 100% @150A . . . . . . . . . . . . . . . . . 60% @ 260A, 100% @ 200A
Power
Supply
: . . . . . . . . . . . . . . . . . . . . . . 415 Volt 3ph . . . . . . . . . . . . . . . . . . . . . . . . . . . . . . . 415 Volt 3ph . . . . . . . . . . . . . . . . . . . . . . . . . . . . . . 415 Volt 3ph
Power
Efficiency
: . . . . . . . . . . . . . . . . . . . . . . . 8.0 kVA . . . . . . . . . . . . . . . . . . . . . . . . . . . . . . . . . . 12.5 kVA . . . . . . . . . . . . . . . . . . . . . . . . . . . . . . . . . 18.5 kVA
Cooling
System
: . . . . . . . . . . . . . . . . . . . . . . Turbo Fan . . . . . . . . . . . . . . . . . . . . . . . . . . . . . . . . . Turbo Fan . . . . . . . . . . . . . . . . . . . . . . . . . . . . . . . . Turbo Fan
Accepts
Bottle
Size
: . . . . . . . . . . . . . . . . . . . . . . . . . All . . . . . . . . . . . . . . . . . . . . . . . . . . . . . . . . . . . . . . . All . . . . . . . . . . . . . . . . . . . . . . . . . . . . . . . . . . . . . . All
Spot
Welding
: . . . . . . . . . . . . . . . . . . . . . . .Timer Fitted . . . . . . . . . . . . . . . . . . . . . . . . . . . . . . . . Timer Fitted . . . . . . . . . . . . . . . . . . . . . . . . . . . . . . .Timer Fitted
Weight
: . . . . . . . . . . . . . . . . . . . . . . . . . . . . . . . . . .75 kg . . . . . . . . . . . . . . . . . . . . . . . . . . . . . . . . . . . . . 95 kg . . . . . . . . . . . . . . . . . . . . . . . . . . . . . . . . . . . 110 kg
3. RATINGS PLATE SYMBOLS
Detailed technical data relative to the performance of the machine is located on the back panel plate.
Please note
that the ratings plate shown (fig.2)
below is an example only intended to assist with the explanations of symbols. To determine the correct technical values of the machine in your possession,
you must refer to the data plate.
9
DATA REGARDING THE MAINS.
U1
:
Alternating supply voltage of the
machine. Allowed limits (±10%).
I1
max
:
Maximum current consumed.
I1
eff
:
Maximum effective current consumed.
Value of delayed fuses for mains
protection.
1
The EUROPEAN standard regarding safety and the
construction of arc welding machines.
2
Symbol for the main internal parts of the welder : i.e.
inverter - transformer - rectifier.
3
Symbol of planned welding procedure: i.e welding
with a continuous flow of welding wire
4
Symbol for power supply line: 3 phase alternating
voltage.
5
Case protection rating: IP2. Standard governing the
required protection from water ingress and isolation
of internal parts from persons and objects.
6
Symbol S: Indicates that welding operations may be
carried out in areas with greater risk of electric shock
(e.g. close to metal masses).
7
Serial Number : Refer to your particular machine
8
Performance of the welding circuit:
UO : Maximum voltage with no-load peak (welding circuit open)
12 /U2 :
Current and corresponding voltage are normal [ U2=(20+0.04 I2) V ] and may
be supplied from the machine during welding.
X :
Intermittent welding ratio: Indicates time during which machine can supply the
corresponding current (same column). This is expressed in % on the basis of
a 10min. cycle (e.g. 60% = 6 min of work, 4 min. break and so on).
A/V-A/V :
Indicates the welding current adjustment range ( minimum - maximum ) at the
corresponding arc voltage.
fig.2
Original Language Version
POWERMIG2750.V2, POWERMIG3500.V2, POWERMIG4500.V2 Issue: 3 - 09/04/10