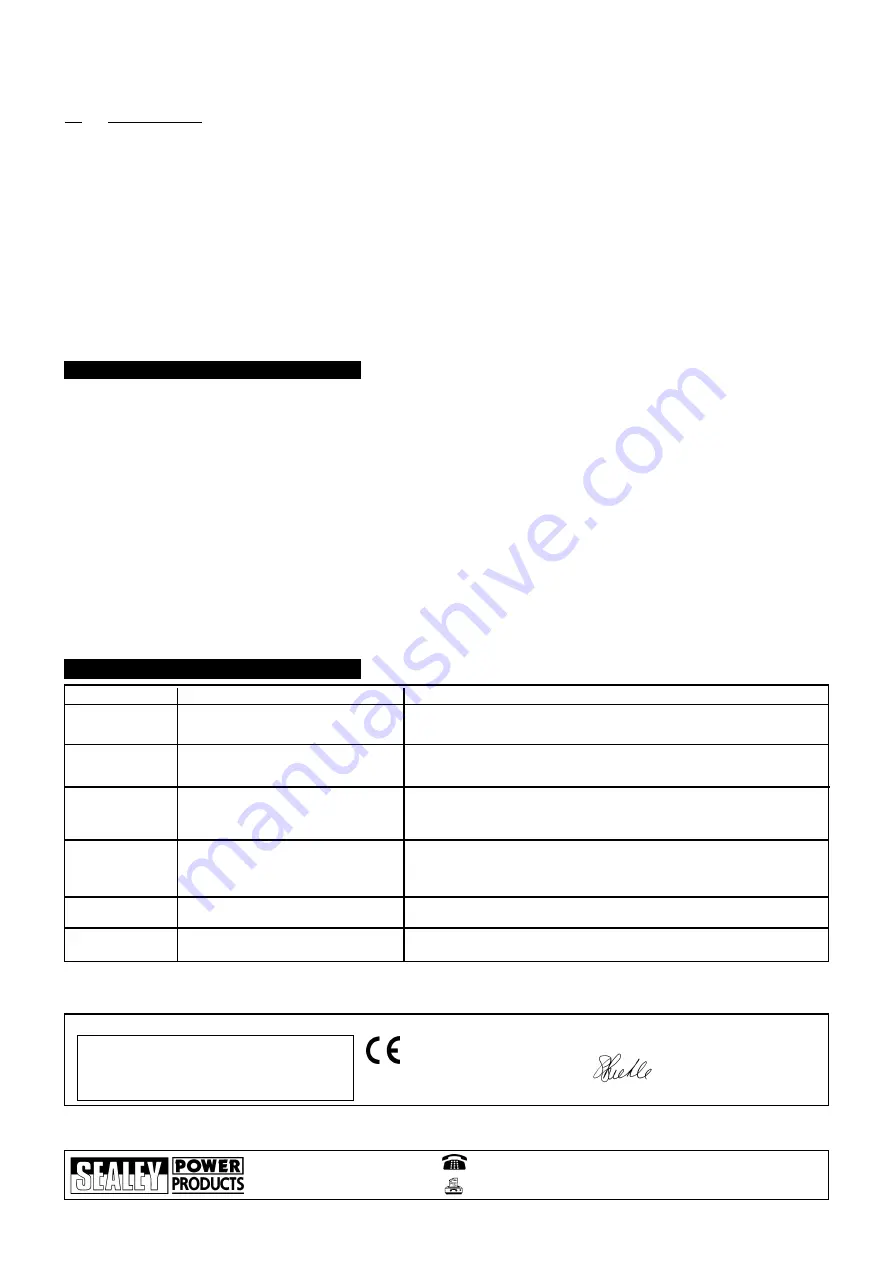
THE PROBLEM
THE CAUSE
THE SOLUTION
8. TROUBLESHOOTING
1. Air motor does
not operate.
2. Poor performance
3. The pump continues
to operate after the
gun trigger has been
released.
4. Reduction of oil
delivery or reduced
pressure in the
system
5. Air loss through the
air exhaust.
6. Oil leaks through the
air exhaust.
1.1. Air pressure is too low.
1.2. Muffler is blocked.
1.3. Internal defect
2.1. Muffler is blocked.
2.2. Oil to be pumped is below 15
0
C.
2.3. Viscosity too high for pump.
3.1 There is an oil leak somewhere in the system.
3.2 Valves not closing properly due to wear or the
presence of dirt.
4.1 Silencer dirty
4.2 Blocked at some point in the system.
4.3 Ball valve not closing properly due to wear or
the presence of dirt.
5.1 Internal damage
6.1 Damaged seals.
1.1. Adjust air pressure to above 2 bar/30psi. (5.1).
1.2. Contact service agent.
1.3. Contact service agent.
2.1. Contact service agent.
2.2. Site tank / barrel in warmer area.
2.3. Check viscosity of oil.
3.1 Check and tighten unions.
3.2 Return pump to service agent for replacement of appropriate valve set.
4.1 Clean or replace silencer element
4.2 Find and clear blockage. Ensure that oil used is clean.
4.3 Return pump to service agent for replacement of ball valve.
5.1 Return pump to service agent for precise diagnosis and replace ment of appropriate parts.
6.1 Return pump to service agent for precise diagnosis and replace ment of appropriate parts.
NOTE:
It is our policy to continually improve products and as such we reserve the right to alter data, specifications and component parts without prior notice.
IMPORTANT:
No liability is accepted for incorrect use of this equipment.
WARRANTY:
Guarantee is 12 months from purchase date, proof of which will be required for any claim.
INFORMATION:
For a copy of our latest catalogue call us on 01284 757525 and leave your full name and address, including postcode.
Declaration of Conformity
We, the UK distributor, declare that the products listed below are in conformity with the following standards and directives
The construction files for this product are held by the Manufacturer and may be inspected on
request by contacting Jack Sealey Ltd.
For Jack Sealey Ltd. Sole distributor of Sealey Power Products.
AIR OPERATED OIL INSTALLATION PUMP STATION
Models AK4555D.V2, AK4556D.V2, AK4558D.V2
98/37/EC Machinery Directive
Signed by Steve Buckle
31st October 2006
"
WARNING!
Ensure that the pump is disconnected from the air line and that there is no pressure in any part of the system before
removing the pump, gun, or hose reel for service or maintenance.
The units should be serviced by an approved Sealey service agent
.
Note: It is essential that dirt and moisture are kept out of the air supply to the pump. Drain air supply system and clean filters regularly.
7.1.
Air line lubricator and water trap
(see fig.1)
This unit is designed to automatically lubricate the pump via the air supply. The unit must be kept topped up with good quality air tool
oil (Sealey reference: ATO/500 - 500ml size or ATO/1000 - 1L size). To adjust the oil flow turn the oil feed control ring on the top of the
unit clockwise - set to minimum flow for this application. At regular intervals check that water is draining from filter-regulator, since it is
essential that water does not enter the pump.
7.2.
Cleaning.
Clean pump and air units with clean damp cloth. Mild detergents may be used to remove oil.
DO NOT use solvents or abrasives and do not get the pump or air units wet.
7.4
Oil line filter.
Item (L) Filter / drain cock (see fig.2) contains a small filter which should be cleaned every 3 months to remove any
accumulated debris from the oil line. First disconnect the air line and then close the shut off valve (K) next to the filter . Operate the
trigger on the dispensing gun to releive any pressure remaining in the system. Unscrew the cap on the ‘Y’ piece and remove and
clean the filter. Replace filter and cap. Open the shut off valve.
NOTE: We recommend that when the pump is not in use for long periods the air supply should be turned of off. This will prolong seal life.
7. MAINTENANCE
01284 757500
01284 703534
E-mail:
Sole UK Distributor
Sealey Group,
Bury St. Edmunds, Suffolk.
Web address: www.sealey.co.uk
6.1.6
CHANGING THE BATTERY. To access the battery compartment remove the screws from the sides of the display moulding (2
each side) and lift off the display. Turn the display moulding over and remove the screw which holds the battery compartment lid
in place (see fig.4). Prise out the old battery and replace with a new one (see fig.5). Lithium battery reference: CR123A.
6.2
To dispense oil.
For safety reasons the system is not designed to fill at high speed. The end of line flow rate will vary
depending on a number of factors including length of line, temperature, air pressure and viscosity of oil.
6.2.1
Pull the hose from out of the hose reel and place the digital dispensing gun in a convenient place. Set the digital display to zero.
6.2.3
Ensure that the shut off valves on the pump and on the hose reel are open.
6.2.4
Before turning on the air supply rotate the knob on top of the air regulator anti-clockwise to set an air pressure less than 6bar.
Now turn on the air supply and screw the air regulator knob clockwise to gradually work up to a pressure of 6bar. The pump will
start to operate at about 2bar and will continue to run until the set pressure is reached within the system.
6.2.5
Before commencing to fill the vehicle with oil ensure that you know the capacity of oil required.
6.2.6
Remove the oil filler cap and place the dispensing nozzle into the aperture. Squeeze the trigger to commence filling with oil. When
the digital display indicates the required amount release the trigger. When a large amount of oil is to be dispensed the trigger can be
locked in the on position by swinging the wire trigger lock over the end of the trigger lever. To release the lock sqeeze and hold the
trigger and swing the wire clip out of the way.
6.2.7
When filling is complete replace the oil filler cap.
6.2.8
Retract the hose into the reel by giving a sharp pull on the hose close to the reel. Do not allow the retracting hose to drag the
dispensing gun over the floor or return unaided.
6.2.9
When filling operations are complete turn the air supply off. Keep the system clean, especially the dispensing gun and nozzle.
NOTE: We recommend that when the pump is not in use for long periods the air supply should be turned of off. This will prolong seal life.
AK4555D.V2 - AK4556D.V2 - AK4558D.V2 - 2 - 05/10/06