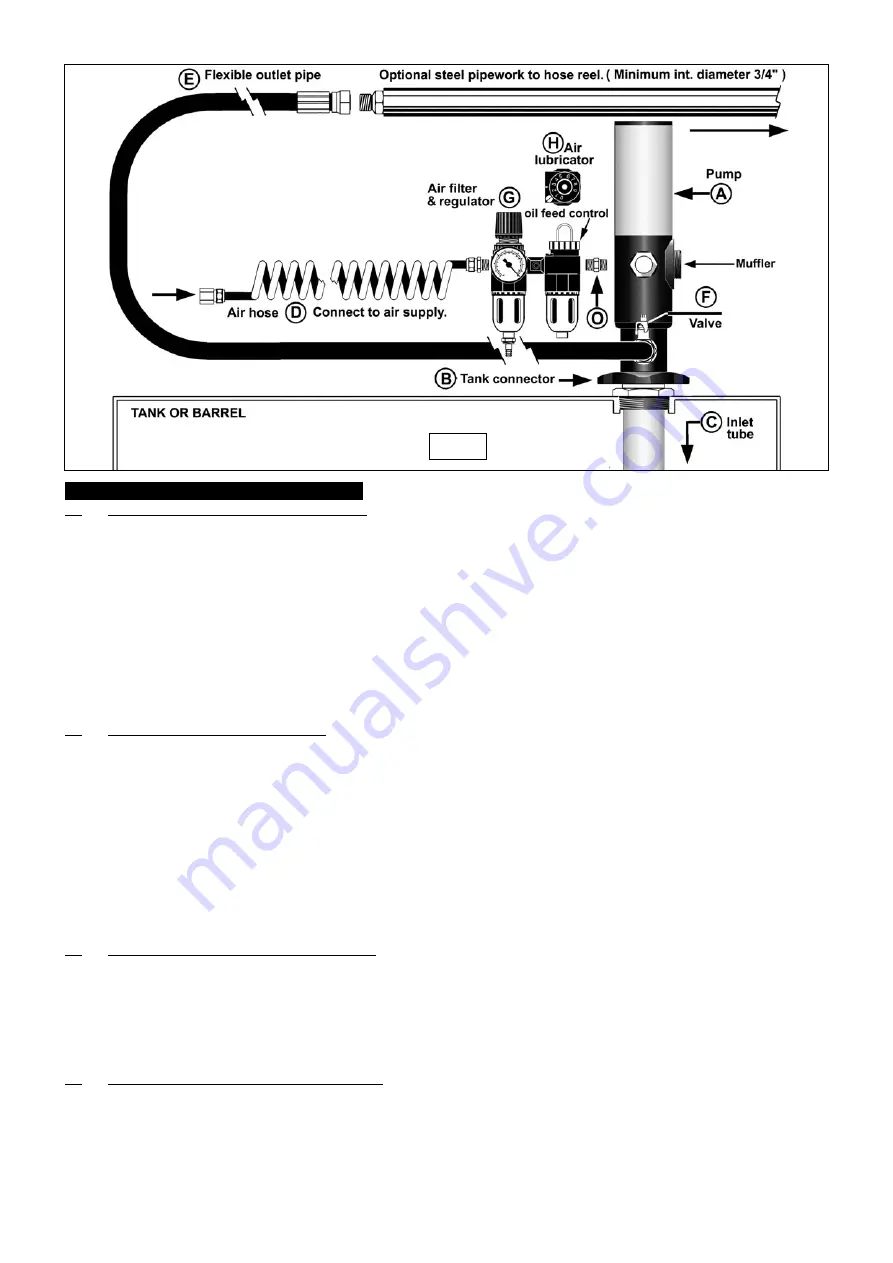
5. ASSEMBLY AND INSTALLATION
fig.1
5.1
Installing the pump and oil pipe connections. ( See fig.1 )
5.1.1
When the oil tank or barrel is to be situated next to the hose reel the flexible outlet hose (E) may be connected directly to the hose
reel inlet elbow. ( See P in fig.2 ) However, in larger workshop situations it will probably be necessary to install steel pipework between
the pump and reel. This pipework should have a minimum internal diameter of 3/4”. No more than two hose reels should be installed
on any one line.
5.1.2
The use of PTFE tape or a suitable sealant is recommended on all oil related joints.
5.1.3
Remove the tank connector (B) from the shank of the pump and screw it into the thread within the tank aperture. Tighten the fitting
with a suitable spanner/wrench applied to the metal flats directly underneath the black clamping ring.
5.1.4
Identify the 1” flexible suction tube complete with filter and non-return valve (C) and screw the open end into the bottom of the pump (A).
5.1.5
Insert the flexible suction tube through the previously fitted tank adaptor . Ensure that the tube lies unkinked within the container as
the body of the pump slides into the tank connector. Set the pump at the required height and rotate it to the required orientation, then
tighten the black clamping ring.
5.1.6
Attach the shut off valve (F) to the pump outlet fitting situated above the tank connector. Attach the flexible outlet hose (E) to the
valve. Before tightening the assembly ensure that the valve is orientated for convenient use.
5.1.7
The other end of the outlet hose may be attached direct to the hose reel or to an intervening steel pipeline.
5.2
Installing the air management system. ( See fig.1 )
"
WARNING!
Clean new air lines ensuring any metal shavings have been removed before connecting the pump and control unit. Dirt in
the inlet lines could damage the unit and may invalidate the warranty.
5.2.1 Use PTFE tape or similar on all air connections to ensure leak-free joints.
5.2.2
The air management system consists of a filter/regulator (G) and a lubricator (H) which are supplied pre-assembled. Both items
have polycarbonate bowls and must not be installed where the bowls may be exposed to solvents and chemicals incompatible
with polycarbonate, or where fumes can weaken the bowls.
5.2.3
Connect the filter/regulator/lubricator assembly to the pump air inlet using fitting (O). Note the air flow direction arrows on each unit and
that lubricator must be between the pump and filter-regulator as shown in Fig.1.
5.2.4
Screw the gauge into the port on the front of the filter-regulator. Screw the coiled air hose (F) into filter-regulator inlet port. Secure all
connections (but do not over tighten).
5.2.5
The bowl of the filter-regulator is fitted with an automatic drain valve the outlet of which may be piped away using suitably sized
flexible tube.
5.2.6
Remove lubricator oil filler plug and fill with good quality air tool oil (Sealey ATO/500 500ml size or ATO/1000 1L size) checking the
maximum level marked on the side of the unit.
5.3
Installing the self retracting hose reel and gun. ( See fig.2 )
5.3.1
Assess the siting of the hose reel in relation to the work area to ensure that the 10m length of hose will reach to the vehicles
work area. Ensure that the wall to which the hose reel will be attached is solid enough to bear the weight of the reel plus the
pulling strain that will be exerted when the hose is pulled out. Fix the hose reel in the chosen position using substantial fixings.
5.3.2
Where a pipeline has been installed between the pump and reel connect the shut off valve (K) and filter/drain cock (L) to the
end of the pipeline as shown in fig.2. Use the flexible inlet hose (J) to connect between the filter/drain cock and the inlet elbow
(P) on the reel. Where there is no pipeline connect the pump directly to the reel using the flexible hose from the pump.(see E in
fig.1) In this case the filter/drain cock should be installed between the shut off valve on the pump and the flexible hose.
5.3.3
Attach the gun (M) with integral digital meter to the end of the reel hose as indicated in fig.2.
5.4
Comissioning the system prior to everyday use.
"
WARNING! Do not operate pump dry - suction pipe must be immersed in oil before operating the pump.
Note: When resetting the regulated pressure always start from below the new required pressure and adjust up.
5.4.1
For the pump to operate at maximum efficiency it must push a full stroke of oil. Before operation and with the whole system installed
all air must be removed from the oil pumping system starting with the pump itself. Place a small container and /or wad of absorbent
material directly below the pump outlet fitting and loosen the fitting by 3/4 of a turn. Before turning on the air supply turn the knob on
AK4555D.V2 - AK4556D.V2 - AK4558D.V2 - 1 - 05/10/06