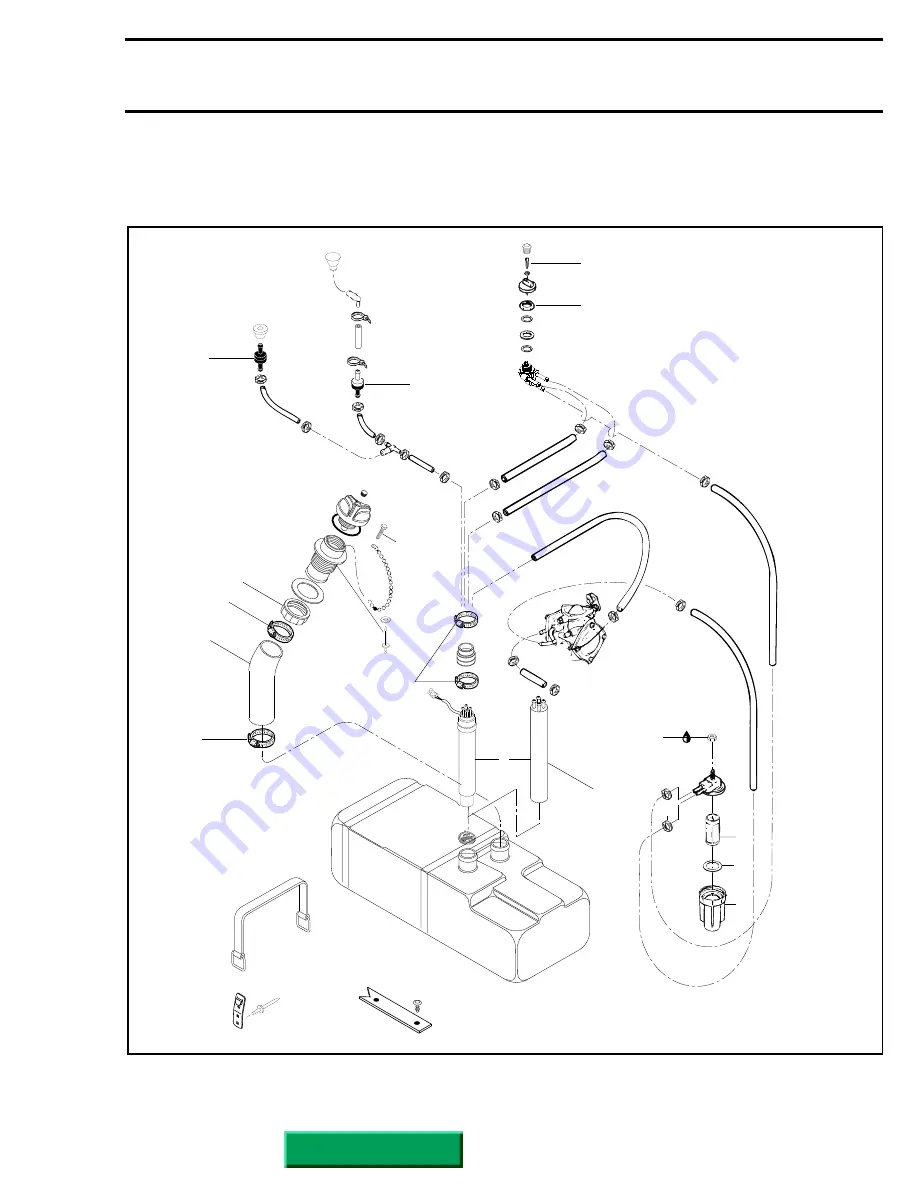
Section 06
FUEL SYSTEM
Sub-Section 01
(FUEL CIRCUIT)
06-01-1
FUEL CIRCUIT
1
SP, SPI and GTS Models
F01F19S
2 N•m
(18 lbf•
in
)
6 N•m
(53 lbf•
in
)
7
6
1 N•m
(9 lbf•
in
)
4
22 N•m
(16 lbf•ft)
4 N•m
(35 lbf•
in
)
5
4
4 N•m
(35 lbf•
in
)
3 N•m
(27 lbf•
in
)
8
(SP)
Loctite 242
3 N•m
(27 lbf•
in
)
1
2
3
1
2
3