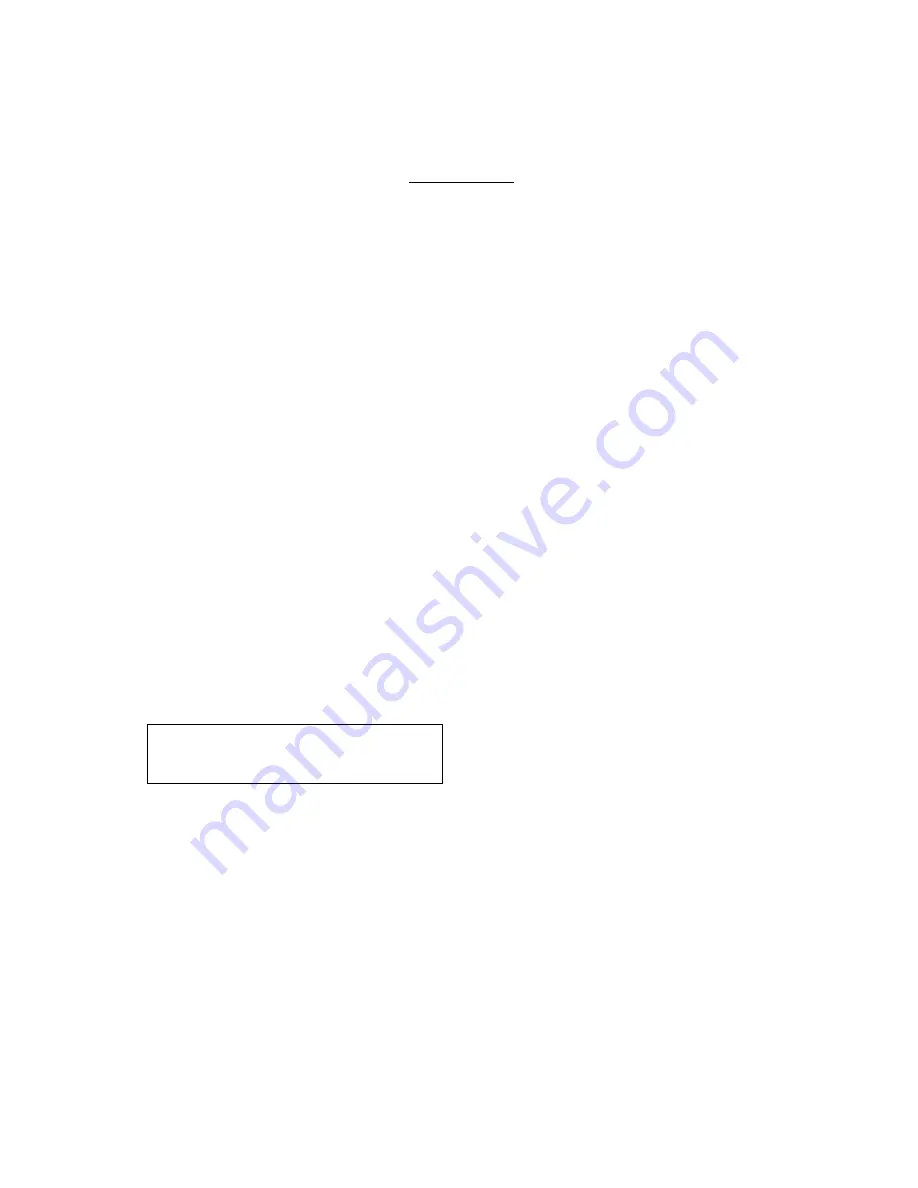
Page 16
Page 16
SECTION II
INSTALLATION
MAR SPLIT UNIT - UNPACKING AND
INSPECTION
1. Visually inspect the exterior of the shipping
container and skid and any severe demage
noted should be reported to the delivery carrier;
and a concealed damage claim filled subject
to internal inspection with carrier represen-
tative present.
2. Remove the packing and remove the side
panels to unloose the shipping bolts securing
the unit to the skid.
3. Remove screw and all panels from cabinet
and inspect for any concealed damage. Notify
carrier of any concealed damage claims as
stated in step 1 above.
4. Remove all internal packing from unit
compartment.
5. Check that refrigerant lines do not rub or
touch lines or surfaces and that all wires are
securely fastened to their terminals.
6. Use clean damp cloth or disposable paper
wiper to wipe clean the exterior surface of the
cabinet.
7. See DATA PLATE on the cabinet base and
check that the location source voltage
corresponds with the voltage specified on the
dataplate.
CAUTION - Unproper voltage supplied to
the icemaker will void your parts
replacement programm.
MAR SPLIT UNIT - LOCATION AND
LEVELLING
1. Position the MAR SPLIT UNIT in the selected
permanent location which could be on top of
ice storage cabinets, on the side of cold
storage room supported by special pre-set
stands or, in case of fishing vessel installation,
inside or on top of the fish hold.
2. After having placed the unit on the support
stand, level the cabinet on both the left to righ
and front to rear directions, by inserting
between the unit base and a support stand
few rubber pads. Fit in unit base holes in the
cabinet, appropriate bolts to fasten unit to
stand.
Make sure to leave enough space around the
unit to allow access to internal components
for inspection and servicing and also for the
fitting of the ice chute if needed.
3. Proceed to position the condensing unit in its
location and to mount it firmly to avoid a
sudden shift that would endager the refrigerant
lines. Precautions to be observed vary with
the kind of situation in which the unit is to be
placed. The area should be well ventilated to
permit escape of refrigerants in case unit
develops a leak.
MAR SPLIT UNIT - REFRIGERANT PIPING
CONNECTION
Fitting sizes:
Liquid Line
Suction Line
MAR 78-108-128
3/8" Gas
3/4" Gas
MAR 208
1/2" Gas
Ø 28 mm
MAR 308
1/2" Gas
Ø 42 mm
Take extreme care to keep refrigeration tubing
clean and dry prior to installation.
Following procedure should be followed:
a) Do not leave dehydrated compressor or filter-
drier open to the atmosphere any longer than
it is absolutely necessary. (One or two minutes
maximum suggested).
b) Use only refrigeration grade copper-tubing,
properly sealed against contamination.
c) Permanent suction lines filters and liquid line
filter-driers are recommended in all filled
installed system.
d) When brazing refrigerant lines, an inert gas
should be passed through the line at low
pressure to prevent scaling and oxidation
inside the tubing. Dry nitrogen is preferred.
e) Line connection to vibration eliminators be
made with silver solder alloy.
Arrange that refrigerant lines run along the walls
and cellings and be supported at intervals frequent
enough to keep tubing atraight and firmly in
place. In all cases the tubing should be run
horizontally and vertically with neat looking bends
of as perfect radius as possible.
The liquid line presents no difficulties as to its
sland and position, but you must install the suction
line so the tubing will drain toward the compressor.
During preparation of liquid line take the necessary
measure to install after evacuation of system, the
filter-drier of suitable size for constant operation.
You may as well consider to install on suction line
a suction tube filter, specially if the required
cleaness cannot be guaranteed.
After all lines are connected, the entire system
must be leak tested.
The complete system should be pressurized to
no-more than 12-13 atm. with refrigerant and dry
nitrogen or dry CO
2
for being leak tested by
means of an electronic type leak detector.