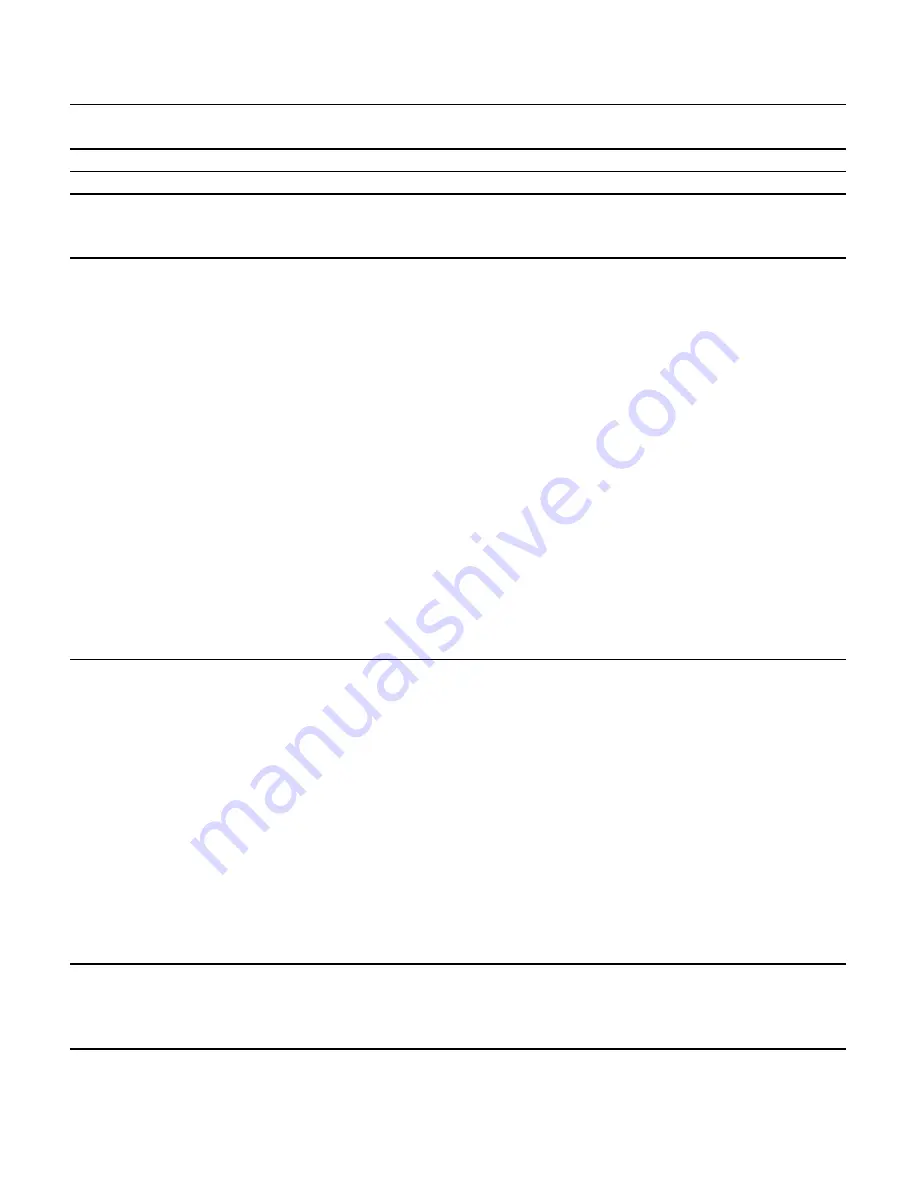
SERVICE DIAGNOSIS: Condition - No Ice Being Produced
STATUS:
NOTHING OPERATES
A. Check: Voltage to the unit, restore it if there is none. Compare to the nameplate.
B. Check: The master switch, switch ON if off.
C. Check: The 3 reset switches, (spout switch, or on prior models the circuit board), high and
low pressure): depress and release each switch. If the still does not start, check: the spout
switch; the high and the low side pressures.
D. Check the low pressure cut out, if closed, go to E; if it is open, it could be due to:
••
Low refrigerant charge
••
The auger not turning
••
Restricted system
••
TXV not opening
1. Check the low side pressure, the low pressure cut out opens at pressure below 4 psig.
If open, reset and:
a. Check if the auger is turning, if it is not, remove the gearbox and:
Check for internal damage, repair and replace in the machine.
b. Check for low charge, add some refrigerant, if the unit will operate,(normal
low side pressure being about 30 psig) stop and look for a leak, repair, replace the
drier, evacuate, and weigh in the nameplate charge. If, with added charge, the unit
does not operate:
Check for a restricted system, replace the drier, evacuate, and weigh in a
nameplate charge.
Check for a Thermostatic Expansion Valve that does not open, if defective,
replace it. Replace the drier, evacuate, and weigh in the nameplate charge.
E. Check the high pressure cut out, if closed go to F, if open check
1.The pressure control opens at 450 psig. Check the high side pressure, reset the control,
and observe: on water cooled, that water soon begins to flow from the condenser drain;
or, on air cooled, that the fan is forcing air through the condenser. If the unit trips out on
pressures below 450 psig, replace the control. If the pressures rise above the trip out
point, and the unit shuts down:
a. Check for adequate water flow on water cooled, if adequate, clean the interior
of the condenser. If the pressures are still too high replace the water regulating valve.
b. Check for adequate air flow on air cooled. Clean the condenser and (if used) the
filter. If the air flow is poor because of the installation, advise the user that the unit
should be moved, or the air around it kept cooler.
Check the fan motor for tight bearings and proper rotation.
Check that the fan blades are clean, and the fan secure to the fan motor shaft.
F. Check the spout switch (a manual reset). It opens from excess pressure of ice inside the ice
chute: this should only happen when the machine does not shut off when the ice storage bin is
full. On units older than July, 1990 production, this switch will reset when the ice melts, but the
machine will not resart until the reset switch on the circuit board is pressed.
G. Check the water level in the reservoir. The machine will not run if there is not enough water in
the reservoir.
1. Restore/adjust water level. See the next step.
FM1200
October, 1991
Page 20