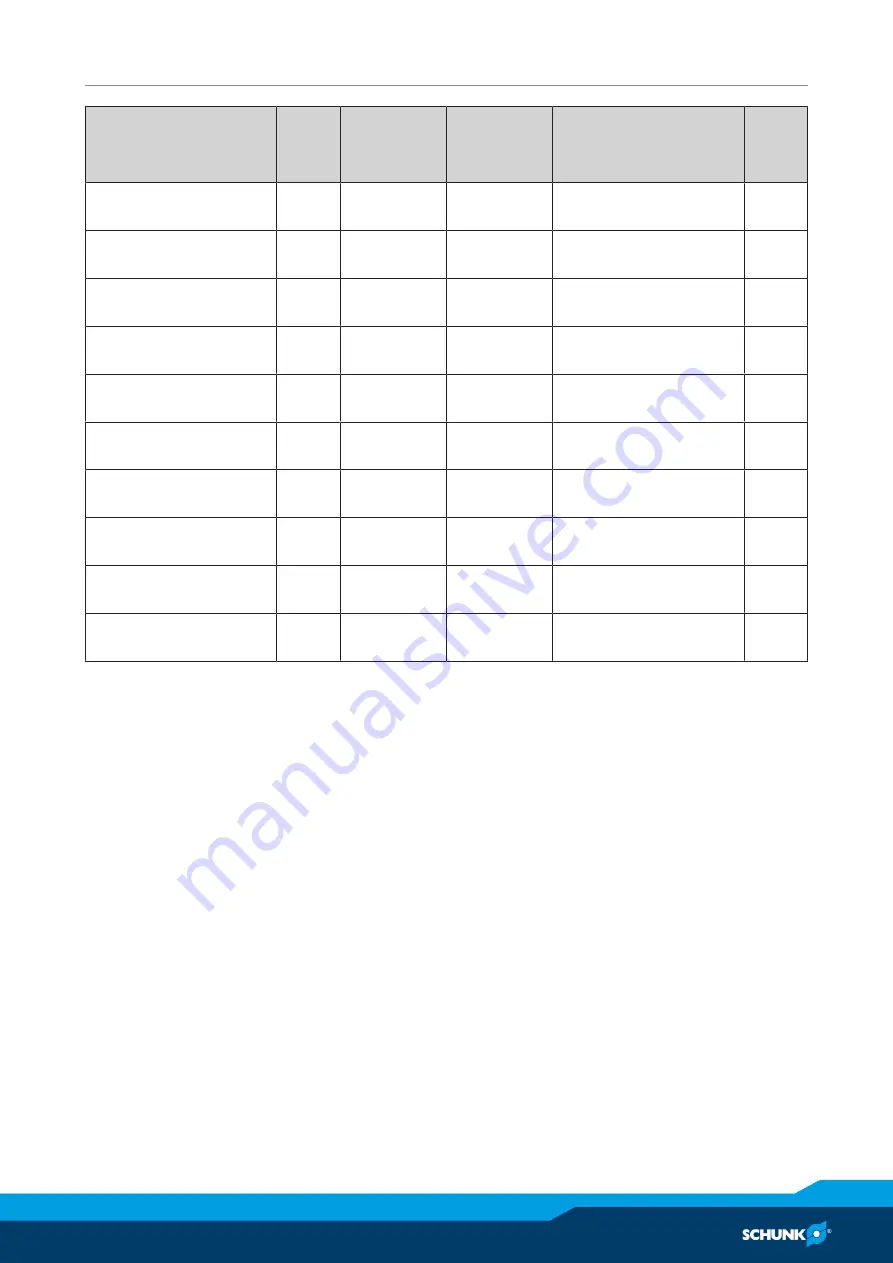
Technical data
02.00 | FMS | Assembly and Operating Manual | en | 389074
9
Behavior active (with
sensor systems)
Height
H [mm]
Measureme
nt range up
to [N]
Overload
range up to
[N]
Behavior passive
(intermediate jaw)
Height
H [mm]
FMS-ZBA → PGN-plus
50
20
145
290
FMS-ZBP → PGN-plus
50
20
FMS-ZBA → PGN-plus
64 / PZN-plus 64
22
260
520
FMS-ZBP → PGN-plus
64 / PZN-plus 64
22
FMS-ZBA → PGN-plus
80 / PZN-plus 80
24
430
860
FMS-ZBP → PGN-plus
80 / PZN-plus 80
24
FMS-ZBA → PGN-plus
100 / PZN-plus 100
28
685
1370
FMS-ZBP → PGN-plus
100 / PZN-plus 100
28
FMS-ZBA → PGN-plus
125 / PZN-plus 125
30
1120
2240
FMS-ZBP → PGN-plus
125 / PZN-plus 125
30
FMS-ZBA → PGN-plus
160 / PZN-plus 160
36
1600
3200
FMS-ZBP → PGN-plus
160 / PZN-plus 160
36
FMS-ZBA → PGN-plus
200 / PZN-plus 200
40
2325
4650
FMS-ZBP → PGN-plus
200 / PZN-plus 200
40
FMS-ZBA → PGN-plus
240 / PZN-plus 240
46
on request
on request
FMS-ZBP → PGN-plus
240 / PZN-plus 240
46
FMS-ZBA → PGN-plus
300 / PZN-plus 300
53
5150
10300
FMS-ZBP → PGN-plus
300 / PZN-plus 300
53
FMS-ZBA → PGN-plus
380
64
on request
on request
FMS-ZBP → PGN-plus
380
64
Range of measurement: range within which the total system has
an accuracy of ±3% / ±5%.
Overload range: range within which the total system has an
accuracy of > ±3% / ±5%. At the end of the overload range, there is
the danger of the mechanical destruction of the intermediate jaw.
Range of measurement and overload range apply to
each
intermediate jaw.