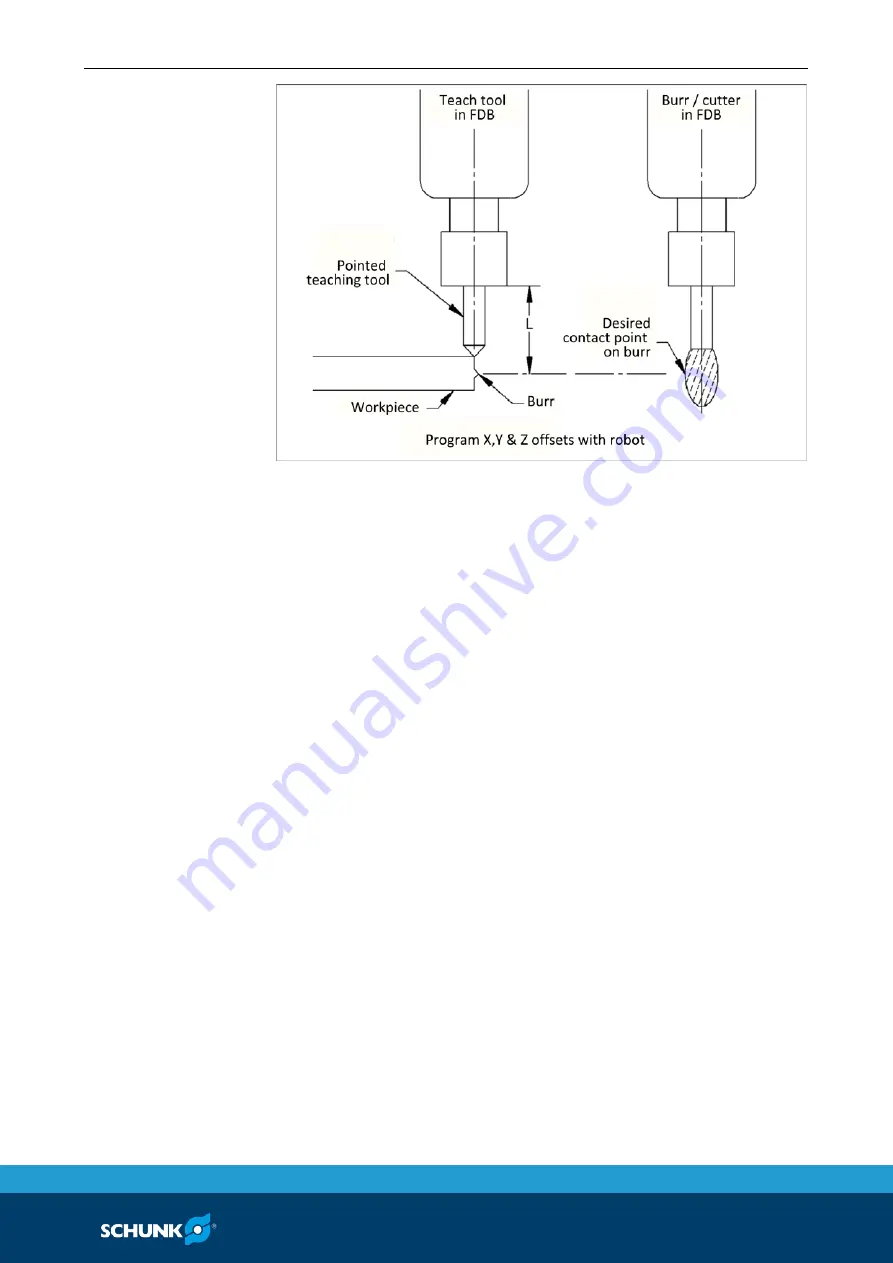
Operation
02.01|FDB 150, 300, 340, 660, 900, 1040 |en
27
FDB Pointed Teaching Tool
Another programming method is to teach the path using the cen-
terline of the burr as a guide, following the edge of the part, and
then manually or automatically adding offsets to the robot path to
achieve the final correct burr path (see Figure). The programming
method used will depend on the machining center's or robot’s ca-
pabilities and programmer preferences.
Inside corners represent a complex situation for compliant debur-
ring spindles. In general, the cutter must not be allowed to simul-
taneously contact both perpendicular surfaces of an inside corner.
The resulting force imbalance in two planes will cause severe tool
chatter. The customer is advised to create a tool path, which will
prevent the cutter from simultaneously contacting two perpendic-
ular surfaces. A tapered cutter may reach further into such an in-
side corner if the tool is presented in an inclined orientation and
closer to the tip of the tool. (Note: When working near the tip of a
tapered cutter the surface cutting speed is reduced.)
When deburring inside radii, a similar situation may arise. The cus-
tomer is advised that no attempt should be made to deburr an in-
side radius less than 1.5 times the diameter of the desired cutter
(Rmin = 1.5 x Cutter diameter). Depending on the depth of cut,
failing to follow these guidelines may result in excessive cutter
contact resulting in excessive tool chatter.
When running the program the first time, observe the path with
the radial compliance air supply turned down to approximately 1.4
bar (FBD-150) oe 0.35 bar (FDB-300/-340/-660/990/1040). When
the robot path speed is increased, it is important to notice that ro-
bot may deviate from the programmed path. Verify that at opera-