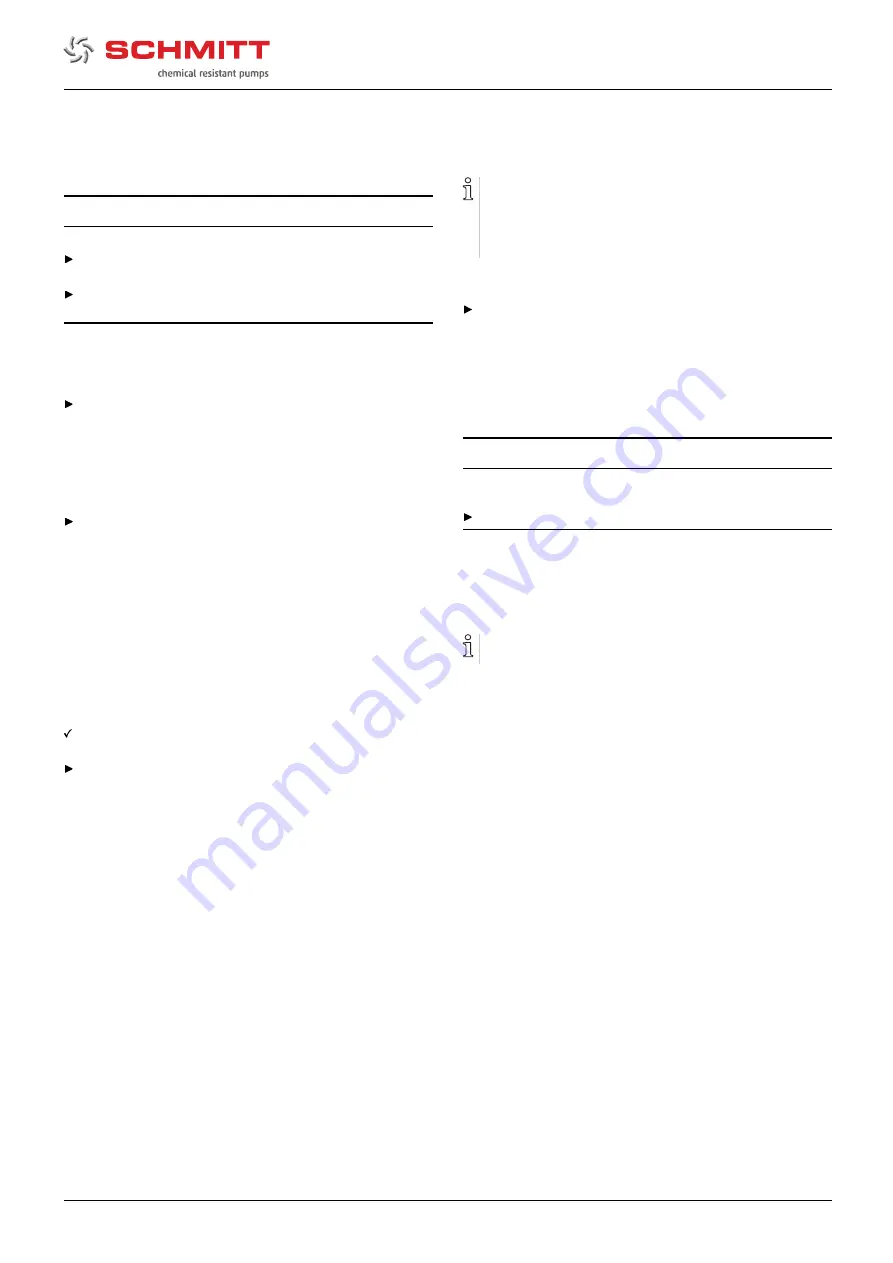
Installation and connection
5
Installation and connection
NOTE
Material damage caused by dirt!
Do not remove the transport seals until immediately before
installing the pump.
Do not remove any covers or transport and sealing covers
until immediately before connecting the pipes to the pump.
5.1
Preparing for installation
5.1.1
Check operating conditions
Ensure the required operating conditions are met:
–
Resistance of body and seal material to the medium
(
→
resistance lists).
–
Required ambient conditions
9.3.1 Ambient conditions, Page 30).
5.1.2
Preparing the installation site
Ensure the installation site meets the following conditions:
–
Pump is freely accessible from all sides
–
Sufficient space for the installation/removal of the pipes
and for maintenance and repair work, especially for the
removal and installation of the pump
–
Pump not exposed to external vibration (damage to
bearings)
–
Pump not exposed to external corrosive influences
–
Frost protection
–
Distance from the pump to the lowest tank fill level <
max. permissible differential head
5.1.3
Prepare foundation and surface
Aids, tools, materials:
–
Spirit level
Ensure the foundation and surface meet the following con-
ditions:
–
Level and horizontal
–
Clean (no oil, dust or other impurities)
–
Capable of bearing the weight of the machine drive and
all operating forces
–
Ensures the stability of the machine drive
5.2
Setting up
1. Lift up the machine drive
2. Put down the machine drive at the place of installation.
3. Screw the fastening screws into the flange and tighten
them.
5.3
Planning pipelines
Note the installation example
Water hammer may damage the pump or the system. Plan
the pipes and fittings as far as possible to prevent water
hammer occurring.
5.3.1
Designing pipelines
Plan pipes safely:
–
No pulling or thrusting forces
–
No bending moments
–
Adjust for changes in length due to temperature
changes (compensators, expansion shanks)
–
Avoid bends close to the pressure-side flange
5.3.2
Arranging the supports and connections
NOTE
Material damage due to excessive forces and torques on
the pump!
Ensure pipe connection without stress.
1. Support pipes in front of the pump.
2. Ensure the pipe supports will always allow expansion and
contraction of the pipes.
5.3.3
Specifying nominal widths
Keep the flow resistance in the pipes as low as possible.
1. Make sure the nominal suction line width is not smaller than
the nominal suction flange width.
2. Make sure the nominal pressure line width is not smaller
than the nominal discharge flange width.
11335/0320
SMP
11