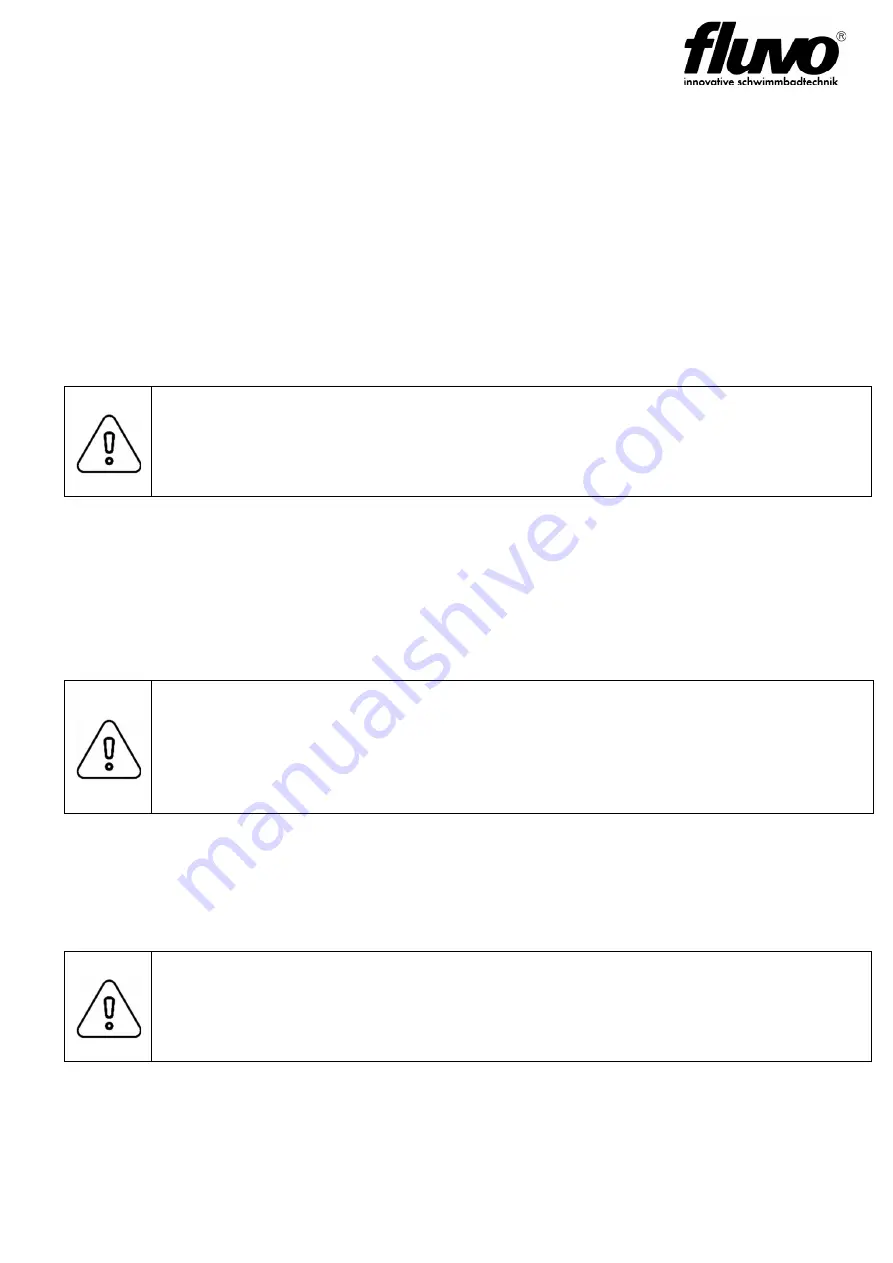
Pump type WK/ SMK
Version: 27220 - E
Schmalenberger GmbH + Co. KG
D-72072 Tübingen / Germany
13
Other external accessories such as air chambers, etc., that are not premounted on the centrifugal pump
in the factory should not be connected until after the centrifugal pump is installed in the system or on
the pump foundation.
3.3.
Setting up and Connecting
3.3.1.
Before starting to set up, check the following:
Is the machine / system / container connection prepared according to the dimensions of the
dimension sheet / installation diagram?
Do the concrete foundations have sufficient concrete strength (min. B 15) per DIN 1045?
Is the concrete foundation hardened?
Is the surface horizontal and even?
Caution! Risk of injury – stability
Pump with large drives that are installed vertically are top-heavy. These pumps must be
secured against tipping during assembly or disassembly, for example by using retaining ropes.
3.3.2.
Installation and Set-up of the Pump
Except for the special design, pumps are always placed on a base plate with the pump or motor mount
and fastened with bolts.
For assembly on a foundation, the centrifugal pump must be aligned with a spirit level.
3.4.
Connecting the Pipelines
Caution!
The centrifugal pump must never under any circumstances be used as a point for securing
the pipeline.
No forces or moments (for example caused by warping or heat expansion) from the pipelines
may be allowed to affect the centrifugal pump.
Pipes must be intercepted directly before the pump and connected with no tension. Their weight must
not place any load on the pump.
The alignment must be made very carefully, since it is the precondition for problem-free operation of
the unit.
Caution!
With hot, corrosive and toxic pumping media!
If pipeline forces are exceeded, points with faulty seals may develop on the centrifugal pump
itself or on the flanges, which may result in powerful ejection of pumping medium.
For short pipelines, the nominal widths should at least match those of the pump connections. For
longer pipelines, determine the most cost-effective nominal width from case to case.