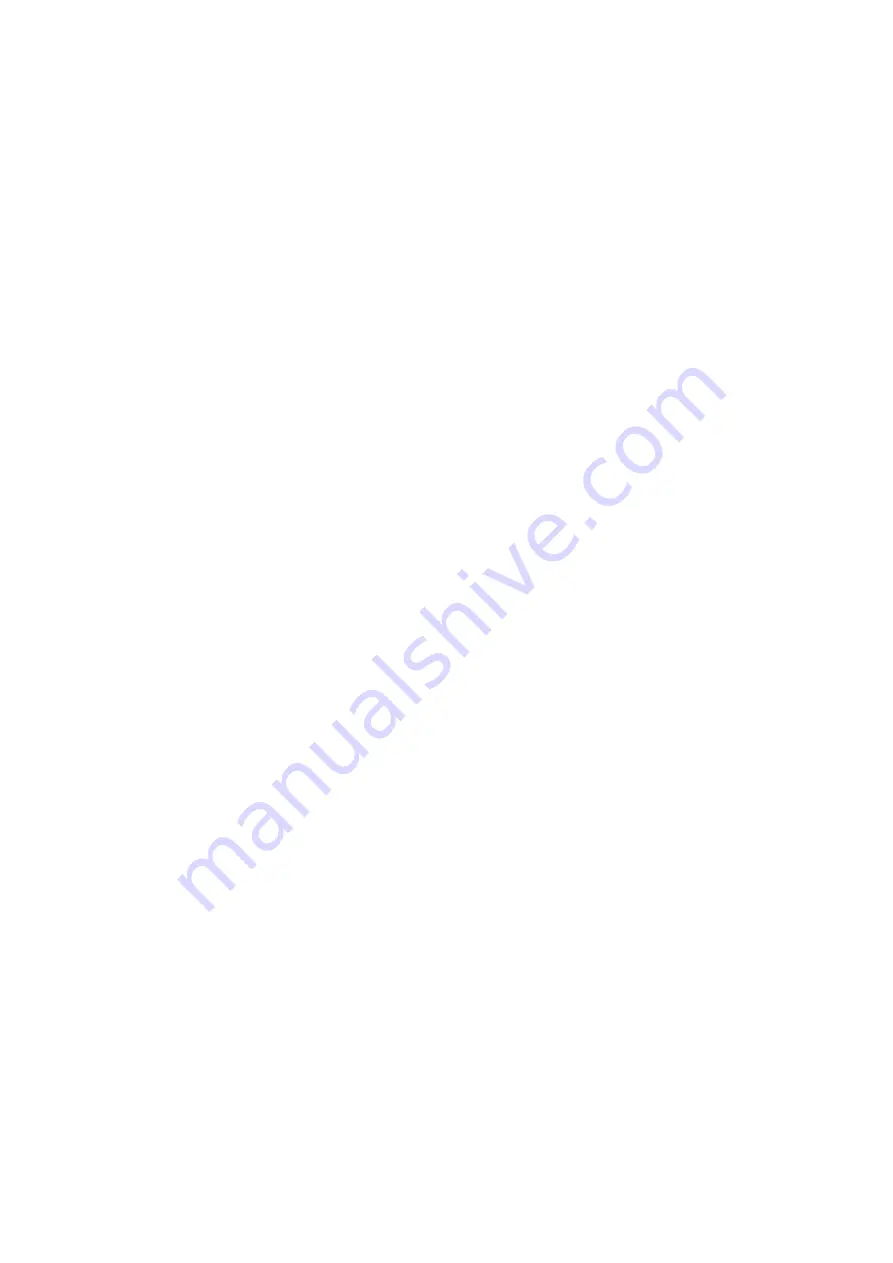
13
3. Feed too deep -Decrease depth of feed.
•
Shake of spindle and roughness of working surface has taken place during performance:
1. The gap of spindle bearing too wide - Adjust the gap in proper or replace bearing
with new one.
2. Spindle loosening up and down - Make two of inner bearing covers on the top tight
each other. Do not over-tighten two inner bearing covers with the taper bearing, it
is ok as long as no gap between them.
3. The gap of taper sliding locate too wide - Adjust the tension of bolt in proper.
4. Loosening of chuck - Fasten chuck.
5. Cutter is dull
– Re-sharpen it.
6. Work-piece has not hold firmly - Be sure to tighten work-piece.
•
Micro feed does not work smoothly:
1. Loosening of clutch - Be sure to tighten it.
2. Worm and worm shaft has worried out - Replace with new one.
3. Loosening of hand-wheel fixed screw - Be sure to tighten it.
•
Without accuracy in performance:
1. The balance of the work-piece - must be considerated as the principle balance
while holding work-piece.
2. Often use of hammer to strike work-piece. Forbidden to use hammer to strike
work piece.
3. Inaccurate horizontal table - Cheek and maintain table for keeping accurate
horizontal after a period of use.
•
Excessive vibration:
1. Motor out-of balance. - Balance or replace problem motor
2. Bad motor. - Replace motor.
•
Motor stalls:
1. Over feeding - Reduce feed rate.
2. Dull drill - Sharpen drill and keep sharp.
3. Motor not building up to running speed. - Replace or repair motor. Check fuses in
all three legs on three phase motors and replace if necessary.
3. Bad motor. - Replace motor.
•
Noisy operation:
1. Excessive vibration. - Check remedy under excessive vibration.
2. Improper quill adjustment. - Adjust quill.
3. Noisy spindle. - Lubricate spindle.
4. Noisy motor. - Check motor bearings or for loose motor fan.
•
Drill or Tool heats up or burns work:
1 .Excessive speed. - Reduce speed.
2. Chips not clearing. - Use pecking operation to clear chips.
3. Dull tool. - Sharpen tool or replace.
4. Feed rate too slow. - Increase feed enough to clear chips.
5. Rotation of frill incorrect. - Reverse motor rotation.
6. Failure to use cutting oil or coolant (on steel). - Use cutting oil or coolant on steel.
•
Drill leads off:
1. No drill spot. - Centre punch or centre drill work-piece.
2. Cutting lips on drill off centre. ~ Regrind drill.
3. Quill loose in head. - Tighten quill.
4. Bearing play. - Check bearings and reseat or replace if necessary.
•
Excessive drill run-out or wobble:
1. Bent drill. ~ Replace drill. Do not attempt to straighten.
2. Bearing play. - Replace or reseat bearings.
3. Drill not seated properly in chucks. - Loosen, reseat and tighten chuck.
•
Work or fixture comes loose or spins:
Содержание 40BK
Страница 4: ...3 1 Overall Aspect ...
Страница 18: ...17 8 Spare Parts Part Drawings for model 40BK ...
Страница 19: ...18 ...
Страница 20: ...19 ...
Страница 21: ...20 ...
Страница 22: ...21 ...
Страница 27: ...26 Part drawings for model 40BKS ...
Страница 28: ...27 ...
Страница 29: ...28 ...
Страница 30: ...29 ...
Страница 31: ...30 ...
Страница 32: ...31 ...
Страница 33: ...32 ...
Страница 39: ...38 Fig 2 Drawing for 40 BK Aut Power Feed System ...