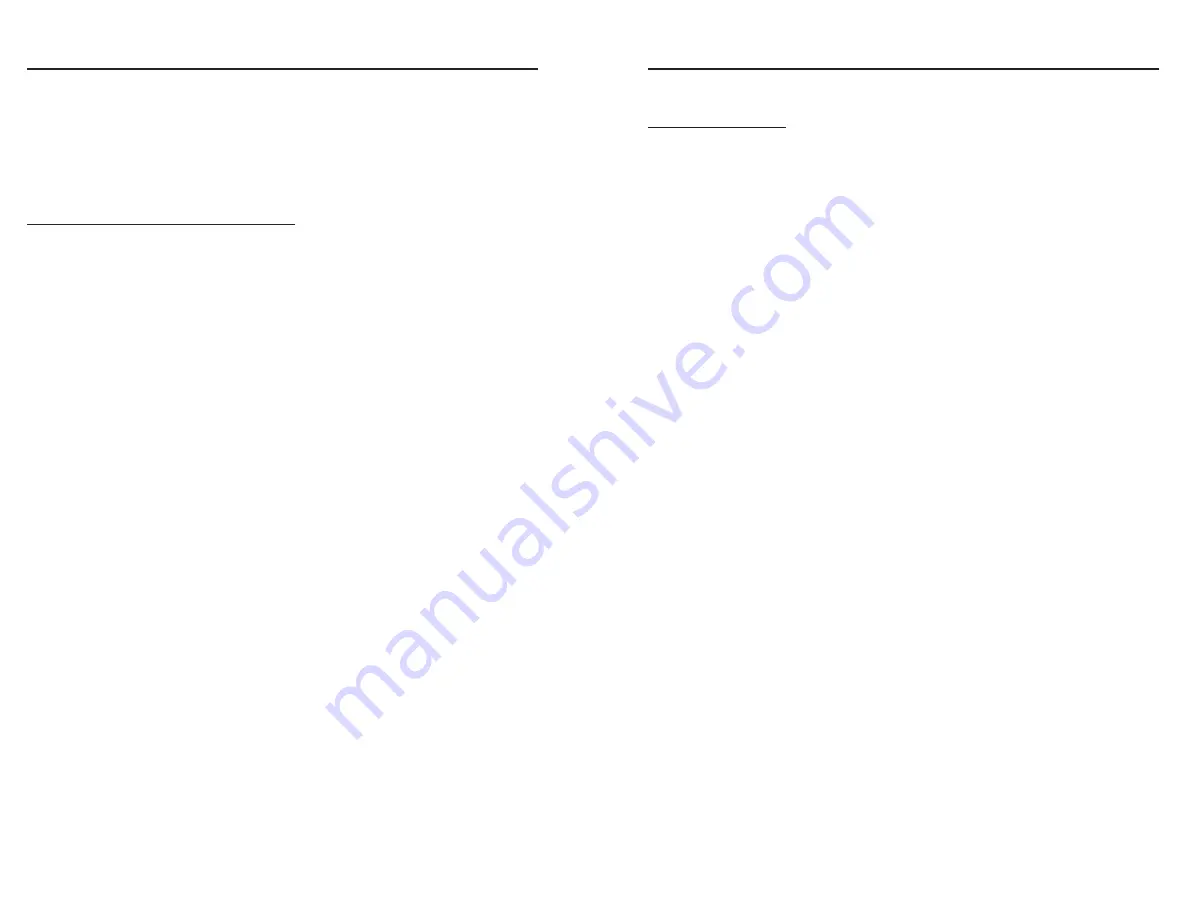
INSPECTION AND MAINTENANCE
T
he Safety Clamps Inspection and Maintenance schedule and procedures
meet and/or exceed the requirements set forth in the ASME B30.20
Below-the-Hook Lifting Devices guideline. The severity of service the clamp
is subjected to will determine the frequency and type of inspection required
for the clamp and will be determined by the clamp owner.
Inspection Before and After Each Use
1. Before using any Safety Clamp, the operator must read and understand
the Operator’s Manual in its entirety.
2. All Safety Clamps should be inspected before and after each use.
Do not use if any components are bent, elongated, gouged, nicked
excessively, worn, and/or damaged. Make sure that nuts, bolts, pins,
and other mechanical fasteners are tightened and secure.
3. Be sure the clamp to be used is the proper clamp for the job. Check
the rated capacity and jaw opening stenciled on the Identi
fi
cation Tag.
Both should equal or exceed the requirements for the load to be lifted.
Warning: Never exceed the rated capacity or use on material that
is not within jaw range of the clamp. Never lift material that does
not meet the minimum rated capacity of the clamp.
4. Do not use the clamp if the Identi
fi
cation Tag or the Warning Tag is
missing or illegible.
5. Inspect the gripping cam(s) (SC-50 or SC-42, Fig. 7) for wear and
defects. Gripping surfaces must be sharp and free of foreign matter.
6. Inspect condition of body for wear, damage and distortion, particularly
in the area of the jaw opening and holes for pins.
7. Inspect the lifting shackle (SC-10, Fig. 7) and all pins for wear and
damage.
8. The lock spring (SC-61, Fig. 7) must have a de
fi
nite amount of tension
when the lock is moved to the lock closed position, with minimal
material in the clamp.
9. Remove from service and tag any clamp in need of repair indicating
the problem area and bring to supervisor’s attention. A full periodic
inspection is to be performed at this time by quali
fi
ed personnel. The
next periodic inspection will be timed from when the clamp is returned
to
service.
10. Make sure that all roll pins are securely in place.
11. Never use a clamp in need of repair.
Safety Clamps, Inc.
Model VL-Channel
8
INSPECTION AND MAINTENANCE
Periodic Inspection
A periodic inspection is to be performed by quali
fi
ed personnel. The
inspection will be performed based on the level of service of the clamp:
Normal Service:
Annual Inspection
Heavy Service:
Semi-Annual Inspection
Severe Service:
Quarterly
1.
Verify and record the model, rated capacity, jaw opening, and
serial number of the clamp which is stenciled on the Identifi cation
Tag.
If the tag is missing or not legible, the serial number is stamped
into the body of the clamp, typically under the gripping pad seat.
Contact Safety Clamps, Inc. and we can identify your clamp and issue
an RGA number to return the clamp to us. We will replace the
Identi
fi
cation Tag at no charge.
2.
Completely disassemble the clamp.
Disassembly directions are on
page
12.
3
Remove all dirt, grease, and other foreign matter
that may inhibit
proper inspection of the clamp body or clamp components.
4.
Clamp Body Inspection
a.) Inspect all welds and all internal and external surfaces for fractures,
wear, and distortion.
b.) Inspect all pin holes for wear and elongation.
c.) Inspect inside the jaw opening for displaced metal and distortion.
d.) Inspect the lock pivot holes for excessive wear.
Warning: Replace lifting clamps containing any fractures,
elongated holes, jaw opening with displaced metal, and/or
distorted jaw openings.
5.
Lifting Shackle (SC-10, Fig. 7) Inspection
a.) Inspect the lifting eye for elongation and wear at the point where the
eye engages the sling attachment.
b.) Inspect the shackle pin hole for wear and elongation.
c.) Inspect the shackle body for bending.
d.) Universal Lifting Shackle: Inspect shackle pivot pin
(SC-14, Fig. 7) and shackle pivot pin hole for wear and distortion.
Note: An elongated shackle eye indicates overloading. An elongated
shackle pin hole indicates wear and possible overloading. A bent
shackle indicates excessive side-loading.
Warning: Replace shackles that are bent, show excessive wear,
or have elongated eye or shackle pin holes.
Safety Clamps, Inc.
Model VL-Channel
9