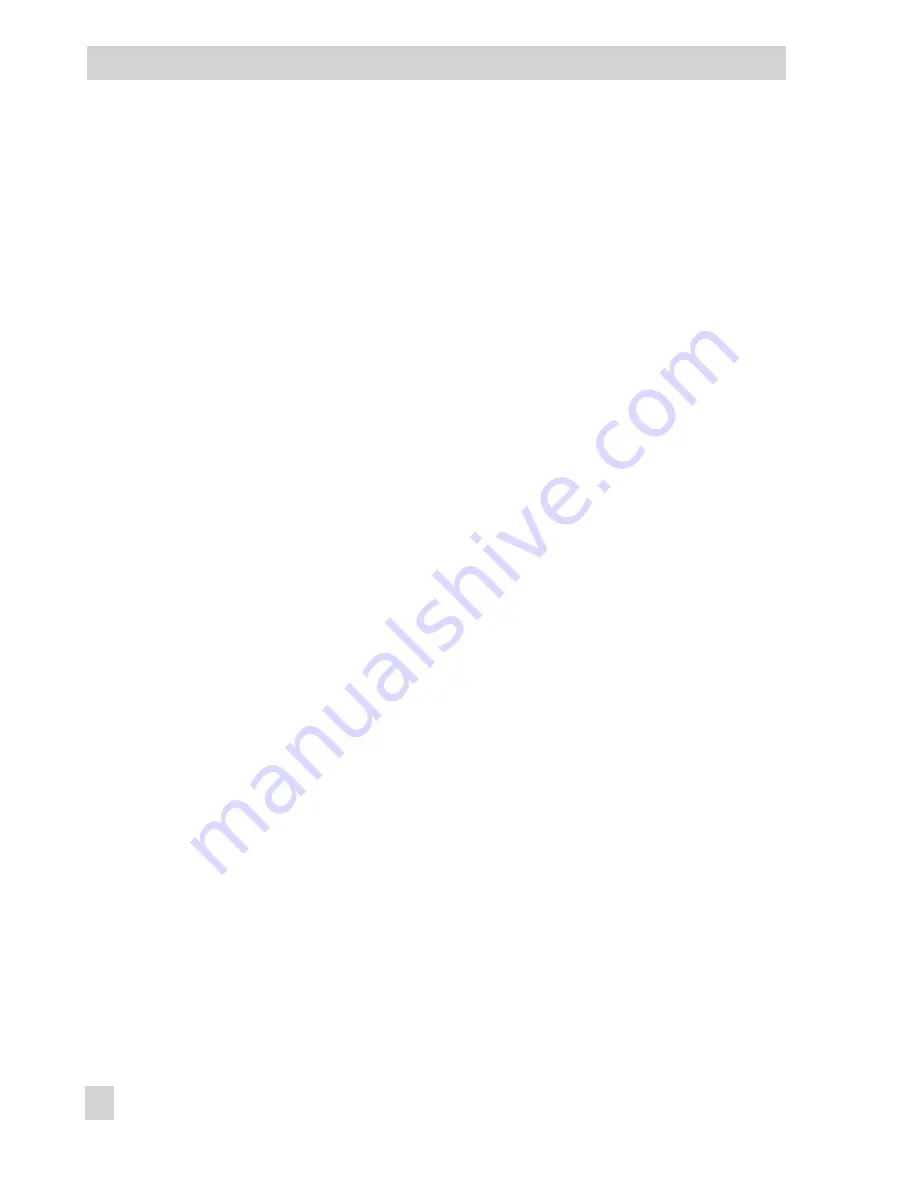
1
Design and principle of
operation
The pneumatic or electropneumatic
positioner ensures a preselected assignment
of the valve stem position (controlled vari-
able x) to the control signal (reference vari-
able w).
The input signal received from a control unit
is compared to the travel of the control
valve, and a corresponding pneumatic sig-
nal pressure (output variable) is produced.
The positioner mainly consists of a pneu-
matic unit including a clamp (10), range
spring (7), diaphragm lever (4) and a
booster (12) with a double plug (13).
The electropneumatic positioner is addition-
ally equipped with an electropneumatic con-
verter (2).
The positioner is designed for direct attach-
ment to SAMSON Type 3277 Actuators.
The control signal from the control unit, pro-
vided it is a pneumatic signal, is applied di-
rectly to the measuring diaphragm (3) as
pressure signal p
e
. Whereas a DC current
input signal in the range of 4 to 20 mA, for
example, is directly passed on to the
electropneumatic converter (i/p converter),
where it is converted into a proportional
pressure signal p
e
.
The pressure signal p
e
produces a force on
the measuring diaphragm (3), which is bal-
anced by the force of the range spring (7).
The deflection of the diaphragm (3) causes
the diaphragm lever (4) to move. The double
plug (13) in the booster (12) follows this mo-
tion, producing a signal pressure p
st
.
The operating direction of the signal pres-
sure, either increasing >> or <> decreasing
when the input signal increases, depends on
the position of the booster which can be ro-
tated by 180°.
A change in either the input signal or the
valve position causes a pressure change in
the booster. The output pressure p
st
of the
booster moves the plug stem to a position
corresponding with the given control signal
(reference variable).
The adjustment screws for ZERO (5) and
SPAN (8) are used to adjust the lower and
upper range value of the input signal.
The range spring (7) must be chosen to
match both the rated valve travel and the
nominal span of the reference variable.
6
EB 8385 EN
Design and principle of operation
Содержание 3760
Страница 24: ...24 EB 8385 EN ...
Страница 25: ...EB 8385 EN 25 ...
Страница 26: ...26 EB 8385 EN ...
Страница 27: ...EB 8385 EN 27 ...
Страница 28: ...28 EB 8385 EN ...
Страница 29: ...EB 8385 EN 29 ...
Страница 30: ...30 EB 8385 EN ...
Страница 31: ...EB 8385 EN 31 ...
Страница 32: ...32 EB 8385 EN ...
Страница 33: ...EB 8385 EN 33 ...
Страница 34: ...34 EB 8385 EN ...
Страница 35: ...EB 8385 EN 35 ...