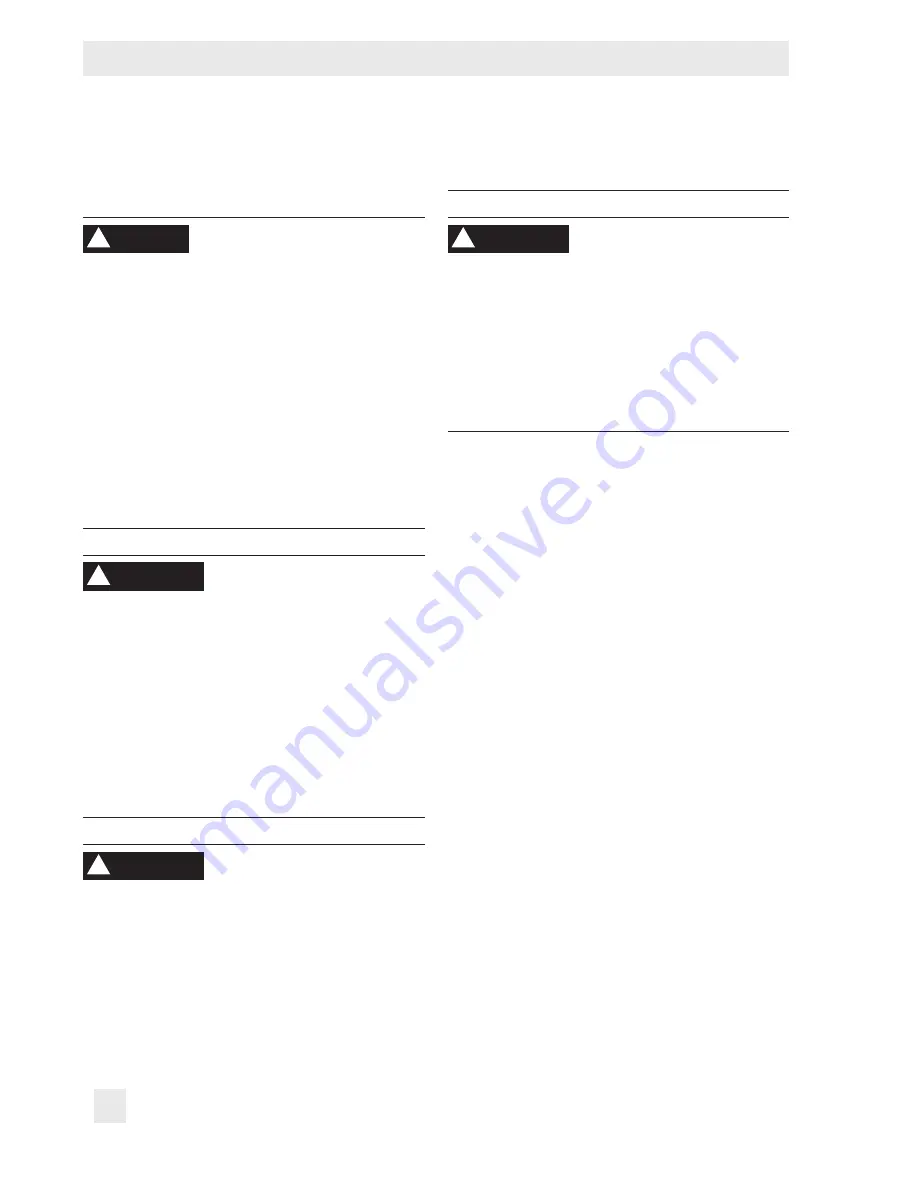
48
EB 8823 EN
Decommissioning and disassembly
9
Decommissioning and
disassembly
Risk of bursting in pressure equipment.
Control valves and pipelines are pressure
equipment. Improper opening can lead to
valve components bursting.
−
Before starting any work on the control
valve, depressurize all plant sections con-
cerned and the valve.
−
Drain the process medium from all the
plant sections concerned as well as the
valve.
−
Wear personal protective equipment.
Risk of personal injury due to sudden escape
of process medium.
The valve has a safety bleed to detect dam-
aged or worn O-rings. The process medium
may escape suddenly and at high pressure.
−
Wear protective clothing, gloves and eye-
wear when working near or on the valve.
−
Do not stay in the range of the safety bleed
longer than necessary.
Risk of personal injury due to residual pro-
cess medium in the valve.
While working on the valve, residual process
medium can escape and, depending on its
properties, may lead to personal injury, e.g.
(chemical) burns.
Wear protective clothing, gloves and eye-
wear.
Risk of burn injuries due to hot or cold com-
ponents and pipeline.
Valve components and the pipeline may be-
come very hot or cold. Risk of burn injuries.
−
Allow components and pipelines to cool
down or heat up.
−
Wear protective clothing and gloves.
9.1
Decommissioning
To decommission the control valve for service
and repair work or disassembly, proceed as
follows:
1. Interrupt the medium flow.
2. Completely drain the pipelines and
valve.
3. Disconnect and lock the pneumatic air
supply to depressurize the actuator.
4.
If necessary, allow the pipeline and valve
components to cool down or heat up.
9.2
Removing the valve from
the pipeline
Version with flanges
1. Put the control valve out of operation (see
section 9.1).
2. Unbolt the flange joint.
3. Remove the valve from the pipeline (see
section 4.2).
DANGER
!
WARNING
!
WARNING
!
WARNING
!
Содержание 3525
Страница 19: ...EB 8823 EN 19...
Страница 25: ...EB 8823 EN 25...
Страница 31: ...EB 8823 EN 31...
Страница 51: ...EB 8823 EN 51...