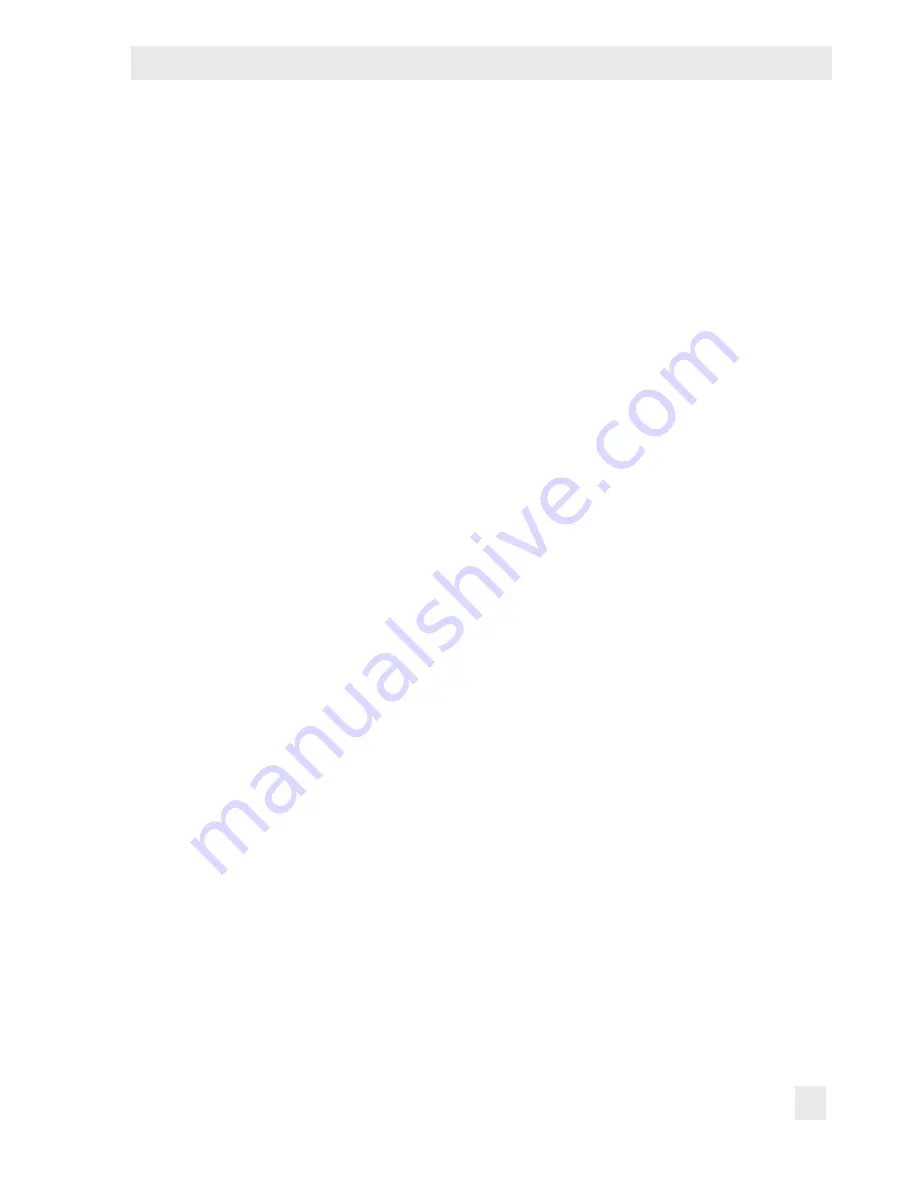
EB 8139 EN
27
Servicing
8. Unscrew the threaded bushing (11) to-
gether with the actuator base (6) from
the valve bonnet (10) using an 24 mm
open-end wrench.
9. Press the threaded bushing (11) out of
the actuator base (6). Replace the slip
washers (38) with new ones.
10. Pull the actuator/plug stem (14) down
out of the valve bonnet (10).
11. Pull all the packing parts out of the pack-
ing chamber using a suitable tool. Clean
the packing chamber thoroughly. Renew
the packing.
12. Slide the plug/actuator stem into the
valve bonnet (10).
13. Carefully slide the packing parts over the
plug/actuator stem into the packing
chamber using a suitable tool. Keep the
correct sequence:
−
Spring (21)
−
Washer (44)
−
V-ring packing (22)
14. Place the top slip washer (38) into the
actuator base.
15. Push the threaded bushing (11) into the
actuator base (6). Make sure that the
O-ring (36) is correctly seated in the
threaded bushing.
16. Place the bottom slip washer (38) on the
valve bonnet (10).
17. Screw the threaded bushing (11) togeth-
er with the actuator base (6) over the
plug/actuator stem (14) onto the valve
bonnet (10).
Tighten the threaded bushing only to the
point where the actuator base (6) can
still rotate on the slip washers (38).
18. Screw tight the retaining screw (60) at
the side to fix the threaded bushing in
place.
19. Slide the washer (43) onto the plug/ac-
tuator stem (14).
20. Place the spring (20) together with the
washer (46) onto the actuator base (6).
21. Slide the piston (3) with piston ring (23)
over the plug/actuator stem (14).
22. Place on the O-ring (33) and washer
(43).
23. Tighten the nut (49) intended for fasten-
ing the piston, while holding the plug/
actuator stem (14) stationary at the flat
-
tened part with an 8 mm open-end
wrench.
24. Put on actuator housing (2) and fasten it
tight onto the actuator base (5) by tight-
ening the screws (47) gradually in a
crisscross pattern.
25. Replace the body gasket (31). See sec-
tion 7.1.
26. Screw the valve bonnet (10) with actua-
tor onto the body (1). Observe tightening
torques.