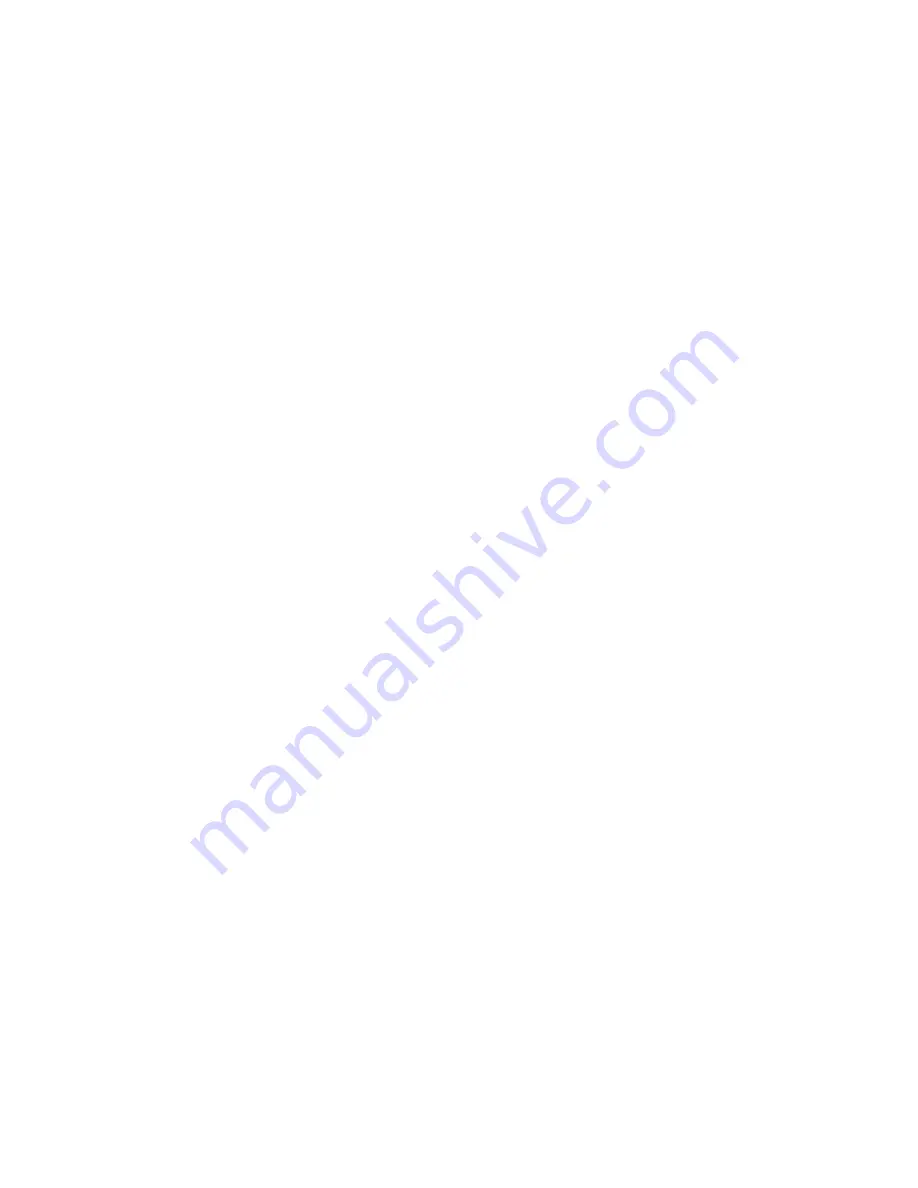
Page 20
DC SIDE CONNECTIONS
The DC input power to the inverter is derived from deep cycle batteries of the
required capacity. Read under
“Specifying Batteries, Chargers and Alternators” on
page 14
for details on sizing and charging of batteries.
Preventing input over voltage
It is to be ensured that the input voltage of the inverter does not exceed 16.5 VDC for
PST-30S-12A or 33 VDC for PST-30S-24A to prevent permanent damage to the inverter.
Please observe the following precautions:
•
Ensure that the maximum charging voltage of the battery charger / alternator / solar charge
controller is below 16.5 VDC for PST-30S-12A or 33 VDC for PST-30S-24A
•
Do not use unregulated solar panels to charge a battery. Under cold ambient temperatures,
the output of the solar panel may exceed 18 V for 12V system or 36 V for 24V system. Always
use a charge controller between the solar panel and the battery.
•
When using Diversion Charge Control Mode in a charge controller, the solar / wind / hydro
source is directly connected to the battery bank. In this case, the controller will divert excess
current to an external load. As the battery charges, the diversion duty cycle will increase.
When the battery is fully charged, all the source energy will flow into the diversion load
if there are no other loads. The charge controller will disconnect the diversion load if
the current rating of the controller is exceeded.
Disconnection of the diversion load may
damage the battery as well as the inverter connected to the battery due to high voltages
generated during conditions of high winds (for wind generators), high water flow rates
(for hydro generators) or cold temperatures (for solar panels). It is, therefore, to be ensured
that the diversion load is sized correctly to prevent the above over voltage conditions.
•
A series type of charge controller connects the solar / wind / hydro charging source directly
to the battery through the series connected switching MOSFET(s). The battery is a capacitive
type of load and will thus, dampen the input voltages of the charging source due to its
capacitive loading effect. As the inverter is connected to the battery bus, it will see the
voltages of the charging source as conditioned by the battery.
Please ensure that the inverter
is connected to the battery bus only after the battery is connected to the battery bus or the
inverter is disconnected from the battery bus first before removing the battery from the
battery bus. If the inverter is connected to the battery bus without the battery connected to
the battery bus, the inverter will be fed with the high open circuit voltages from the solar /
wind / hydro and will damage the inverter permanently
•
Do not connect the inverter to a battery system with a voltage higher than the rated battery
input voltage.
Preventing reverse polarity on the input side
When making battery connection on the input side, make sure that the polarity of
battery connection is correct (Connect the positive of the battery to the positive
terminal of the inverter and the negative of the battery to the negative terminal of
the inverter). If the input is connected in reverse polarity, DC fuse(s) inside the inverter
will blow and may also cause permanent damage to the inverter
Connection from the batteries to the DC input side of the inverter – cable and fuse
sizes
The flow of electric current in a conductor is opposed by the resistance of the
conductor. The resistance of the conductor is directly proportional to the length of
the conductor and inversely proportional to its cross-section (thickness). The resistance
in the conductor produces undesirable effects of voltage drop and heating.
Thus,
thicker and shorter conductors are desirable
. The size (thickness / cross-section) of the
conductors is designated by AWG (American Wire Gauge).
Please note that a smaller
AWG # denotes a thicker size of the conductor up to AWG #1.