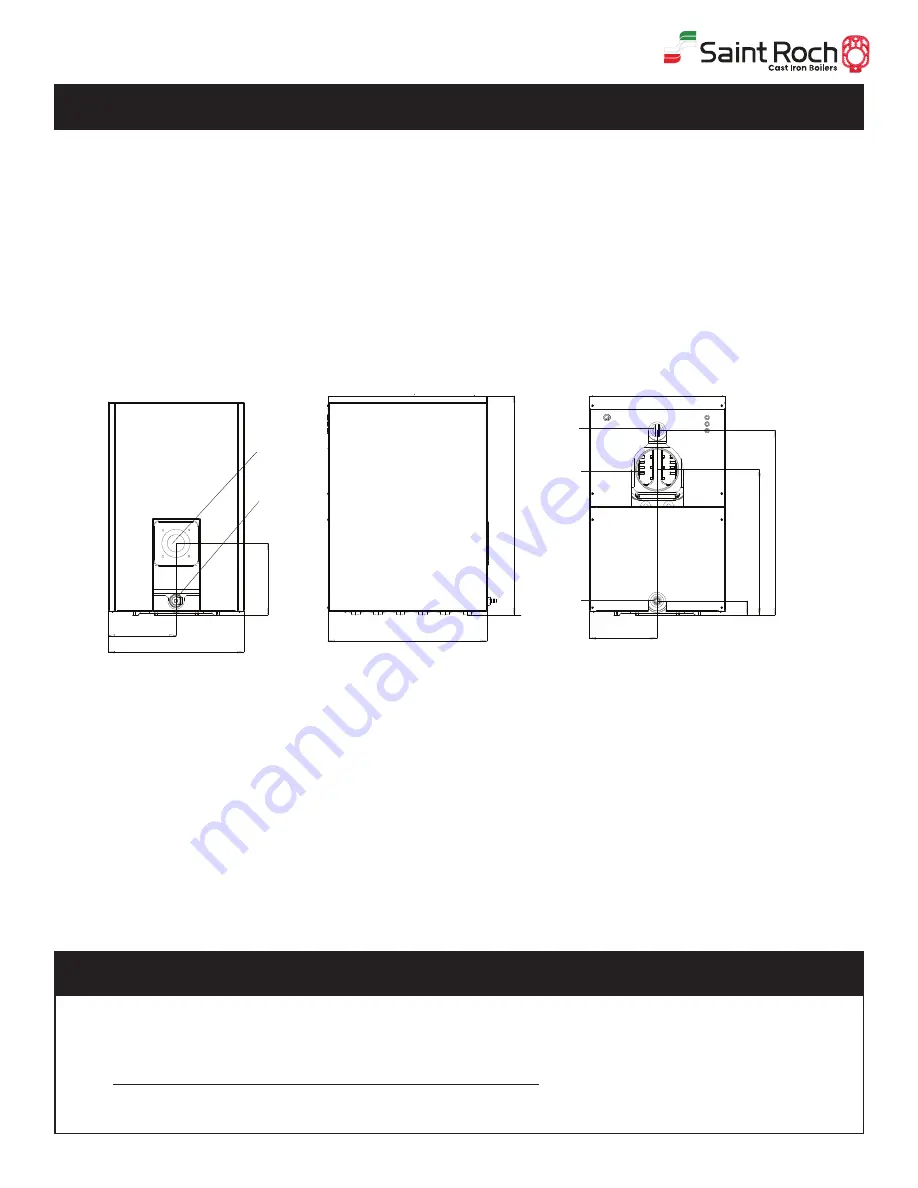
9
www.saintroch.us
732.8 *
W
39.75”
Burner
opening
Ø 5”
Drain cock
Ø 3/4"
Supply
Ø2"
Flue Collar
Ø
Return
Ø2"
24.5”
12.25”
13”
8”
26
1/4
”
33
1/2
”
12.25”
2
1/2
”
4. Installation of Boiler Trim Components
Boiler Tapping Diagram:
1. Install limit control sensor in rear section TOP using 3/4” immersion well. All tapings
and joints should be sealed with piping compound. The limit can be adjusted up to
220
o
F, and should be set to the desired temperature by the installer. The differential is
also adjustable between 5 and 30 degrees. It should be set as close to 30 degrees as
possible to prevent short cycling of the boiler. Run the sensor from behind the control
to the immersion well and fix it according to manufacturer’s instructions.
2. Install Pressure Relief Valve in opposite, manifold using 3” nipple and 3/4” elbow, Pipe
must discharge to the floor.
3. Install 3/4” boiler drain in lower right rear tapping.
4. Install combination pressure/temperature gauge in the manifold. The gauge must be
tightened using a wrench and not your hand.
5. Place the 14” x 24” Cera-fiber blanket on the floor of the combustion chamber of the
boiler
Trim Kit Components
:
1 – Tridicator pressure/temp gauge
1 – ¾” X 3” Nipple
1 – 30 PSI pressure relief valve
1 – ¾” Boiler drain
1 – Cera-fiber Pad for bottom of the combustion chamber
1 – ¾” Plugs
1 – ¾” 90° Elbow
1 –
¾” Electrowell
(Gas systems only)
1-Double acting barometric damper with manual reset spill switch
SAFETY RELIEF VALVE
1. The safety relief valve should be piped into one of the tapings on manifold in the
rear of the boiler
2. The relief valve should be installed using the hardware supplied in the trim kit
without valving between the PRV and the boiler.
3. Pipe the discharge for the safety relief valve with copper tube to the floor and
make sure installation of the pipe conforms to local codes.