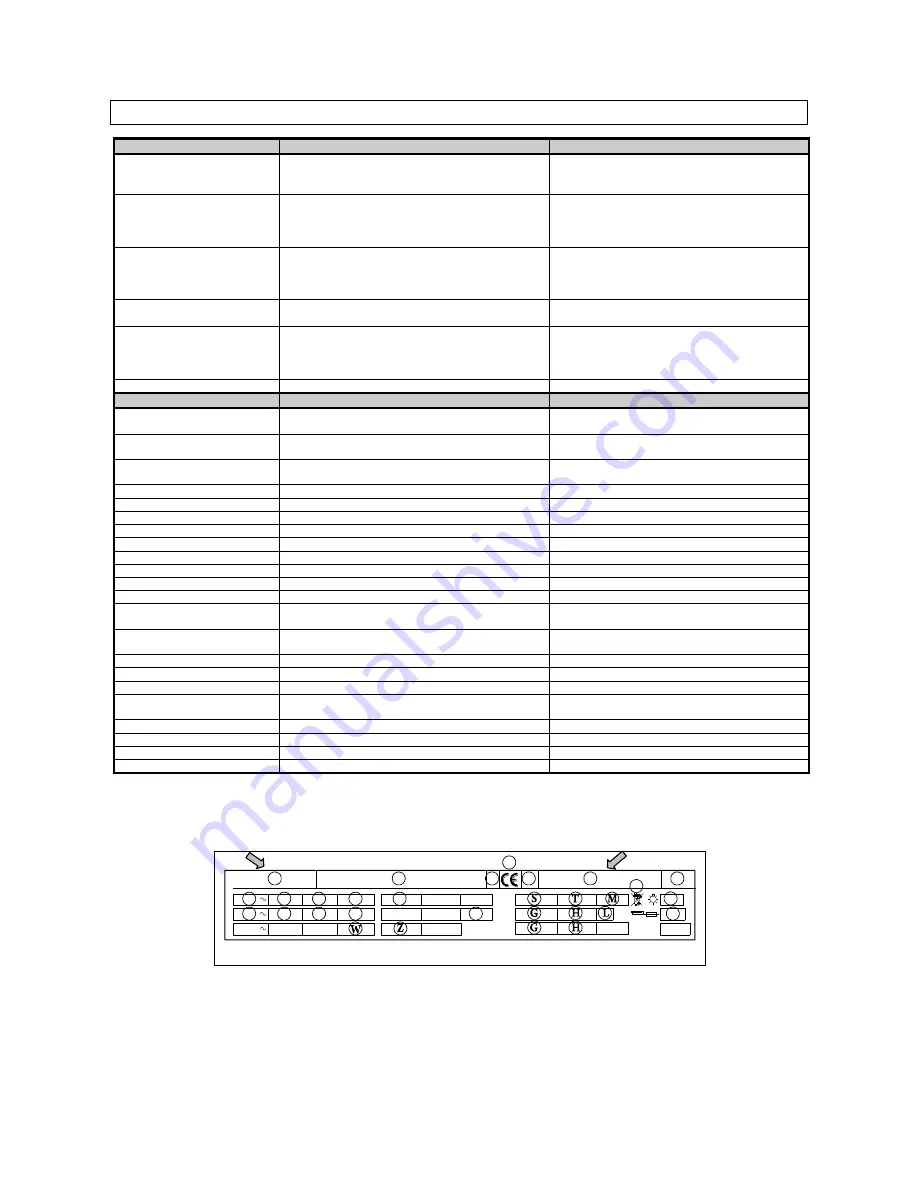
56
3222180_GB
ALARMS TABLE
If the fault is not corrected by following the above instructions ask for skilled assistance and avoid carrying
out any other operations, especially on the electricals. When informing the servicing company of the fault,
state
1
and
5
numbers
(model and serial number).
FAULT
CAUSE
REMEDY
The display board does not
switch on
No power supply
Blown fuse
Loosened connections
Check the connection to the power mains
Replace fuses
(
qualified technician
)
Check connection fitting
Compressor failure
High and Low-pressure pressureswitch on
Clicker on
Contactor failure
Compressor thermal relay on
Qualified technician required
Qualified technician required
Qualified technician required
Qualified technician required
The compressor is working
but the cabinet is not
cooling
Frosted evaporator
No coolant inside the refrigerating system
Delivery solenoid valve failure
Condenser dirty
Open the door and carry out the defrost cycle
Qualified technician required
Qualified technician required
Clean the condenser
Evaporator fans are not
working
Fan failure or short-circuit
Door micro failure
Qualified technician required
Qualified technician required
The condenser fans do not
work
Faulty pressure switch
Faulty fan
Faulty pick-up condenser
Lack of consent from compressor solenoid switch
Qualified technician required
Qualified technician required
Qualified technician required
Qualified technician required
Lack of evaporator defrosting
Incorrect defrosting programming
Check the defrosting cycle programming
ALARM/
EVENT
CAUSE
REMEDY
High temperature alarm
(in conservation)
Room Temp above set value
If the temperature is not within the specified range,
apply to a qualified technician
Low temperature alarm
(in conservation)
Room Temp below set value
If the temperature is not within the specified range,
apply to a qualified technician
Limit temperature alarm
(in chilling/freezing)
Cell or core temperature higher than the set value
If the temperature is not within the specified range,
apply to a qualified technician
Room probe alarm
Room Probe interrupted
Qualified technician required
Evaporator probe alarm
Evap Probe interrupted
Qualified technician required
Condenser probe alarm
Cond Probe interrupted
Qualified technician required
Dirty condenser alarm
Condenser dirty
Clean the condenser
Point needle probe alarm
Needle Probe interrupted
Qualified technician required
Underskin needle probe alarm
Sub-dermis needle probe interrupted
Qualified technician required
External needle probe alarm
External needle probe interrupted
Qualified technician required
Electr.box probe alarm
Electrical panel probe interrupted
Qualified technician required
Electr.box overtemp. alarm
Electrical panel temperature higher than the set value
Qualified technician required
Open door alarm
QC room door open
Door micro faulty
Close the door
Qualified technician required
BlackOut alarm
No power supply
When power is restored, check the max. temperature
reached inside the room
High pressure alarm
Intervention by high pressure switch
Qualified technician required
Low pressure alarm
Intervention by low pressure switch
Qualified technician required
Compressor overload alarm
Compressor thermal relay on
Qualified technician required
Mother board communication
alarm
Communication between the panel board and the
display board interrupted
Qualified technician required
Mother board EEPROM alarm
Data memory corrupted
Qualified technician required
Panel board EEPROM alarm
Data memory corrupted
Qualified technician required
Needle probe 1 alarm
Needle Probe 1 interrupted
Qualified technician required
Needle probe 2 alarm
Needle Probe 2 interrupted
Qualified technician required
N
P
1
2
6
3
4
5
7
R
E
F
A
B
C
D
A
B
C
D