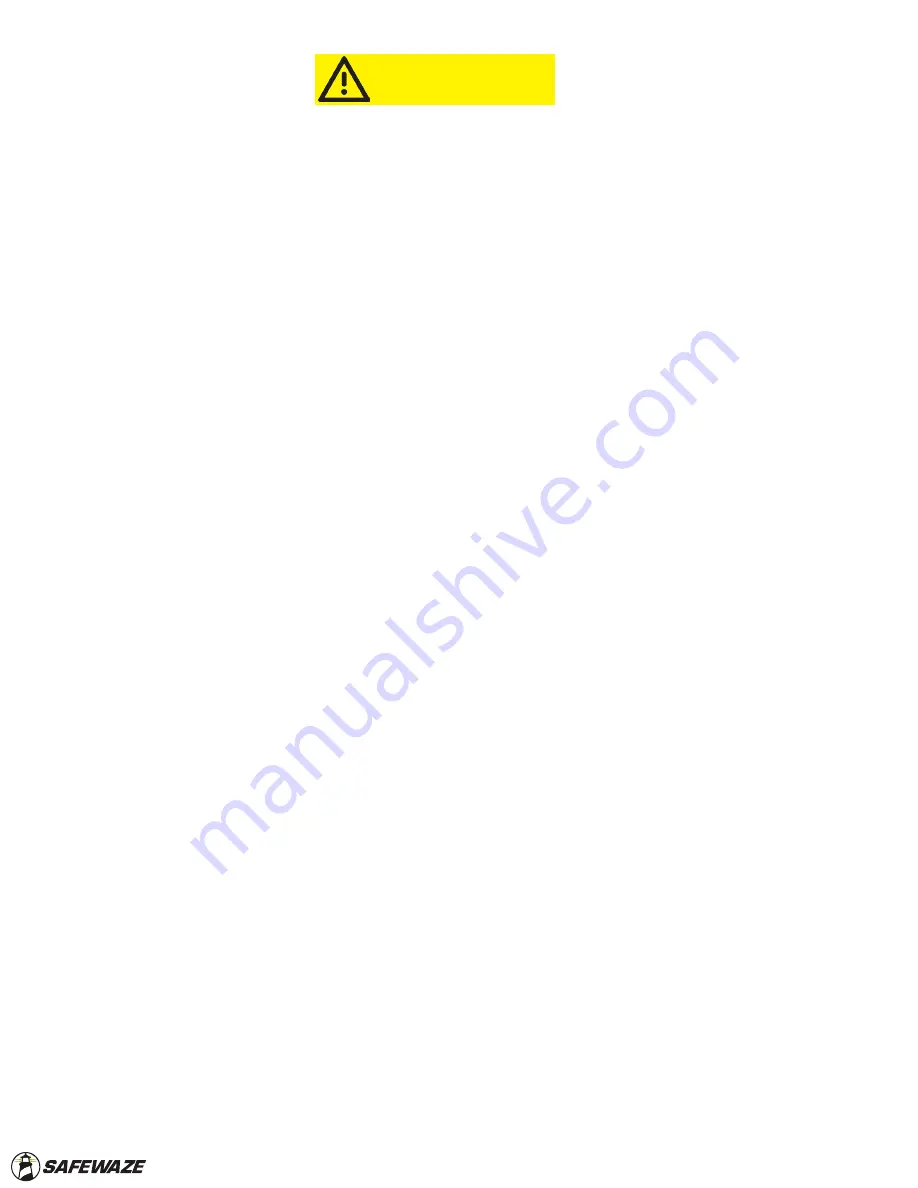
2023 Copyright Safewaze
IMPORTANT
USER INSPECTION, MAINTENANCE AND STORAGE OF EQUIPMENT
MAINTENANCE AND STORAGE
It is essential that the users of this type of equipment receive proper training and instruction including detailed
procedures for the safe use of such equipment in their work application. ANSI/ASSP Z359.2, Minimum
Requirements for a Comprehensive Managed Fall Protection Program, establishes guidelines and requirements
for an employer’s managed fall protection program including policies, duties and training; fall protection
procedures; eliminating and controlling fall hazards; rescue procedures; incident investigations; and evaluating
program effectiveness.
Users of personal fall arrest systems shall at a minimum, comply with all manufacturer instructions regarding the
inspection, maintenance and storage of the equipment. The user’s organization shall retain the manufacturer’s
instructions and make them readily available to all users. See ANSI Z359.2,
Minimum Requirements for a
Comprehensive Managed Fall Protection Program,
regarding user inspection, maintenance and storage of equipment.
1. In addition to the inspection requirements set forth in the manufacturer’s instructions, the equipment shall be inspected
by the user before each use and additionally by a competent person, other than the user, at interval of no more than
one year for:
• Absence or illegibility of markings.
•
Absence of any elements affecting the equipment form, fit or function.
• Evidence of defects in, or damage to, hardware elements including cracks, sharp edges, deformation, corrosion,
chemical attack, excessive soiling, abrasion, alteration, needed or excessive lubrication, excessive aging and
excessive wear.
2. Inspection criteria for the equipment shall be set by the user’s organization. Such criteria for the equipment shall equal
or exceed the criteria established by this standard or the manufacturer’s instructions, whichever is greater.
1. Maintenance and storage of equipment shall be conducted by the user’s organization in accordance with the
manufacturer’s instructions. Unique issues, which may arise due to conditions of use, shall be addressed with the
manufacturer.
3. Equipment shall be stored in a manner as to preclude damage from environmental factors such as temperature, light,
UV, excessive moisture, oil, chemicals and their vapors or other degrading elements.
2. Equipment, which is in need of, or scheduled for, maintenance shall be tagged as unusable and removed from service.
3. When inspection reveals defects in, damage to, or inadequate maintenance of equipment, the equipment shall be
permanently removed from service or undergo adequate corrective maintenance by the original equipment
manufacturer or their designate before return to service.
Record identification information before using this product. Identification information may be found on the
equipment label (See Figure 14). This information should be recorded in the “Inspection Form” located at the
back of this manual (Section 26.0).
Questions regarding the use, care, or suitability of this equipment for your application? Contact Safewaze.
Never exceed the stated maximum capacity of your fall protection equipment.
User must ensure compatibility of components if using fall protection equipment produced by more than one
manufacturer.
Never use equipment that has failed pre-use or other type of inspection. Equipment must be removed from
service if inspection reveals any defects or damage.
Never alter or modify fall protection equipment. Unauthorized modification or alteration of fall protection
equipment can result in serious injury or death.