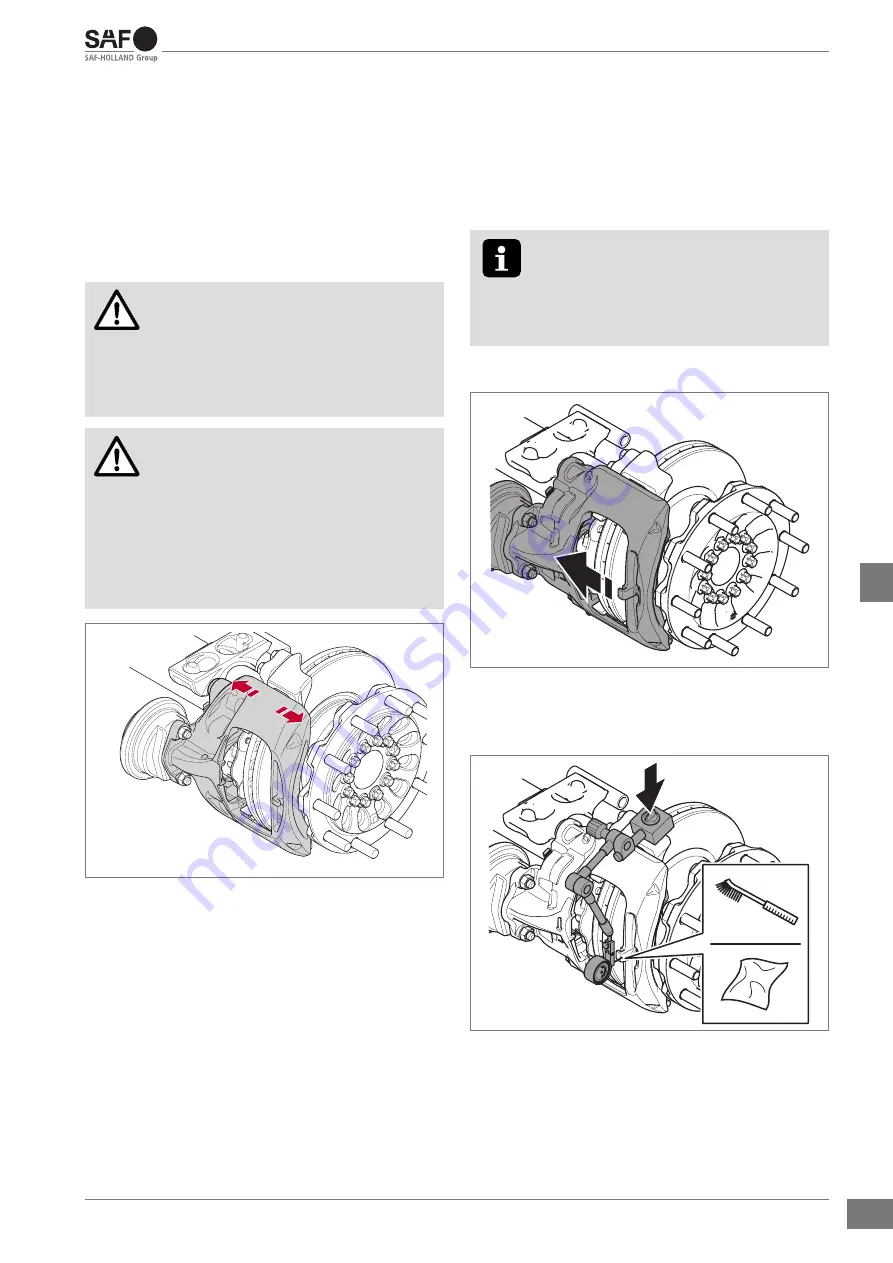
4 Inspection procedures
21
en
XL-SA30000RM-en-DE Rev A • 02.2016 • Errors and changes excluded © SAF-HOLLAND
5. If OK then manually retract the thrust plate by
rotating the reset shaft anti-clockwise with the
Torx 55. Continue rotating until the position re-
quired to refit the brake pads is reached.
6. Once the inspection is completed satisfactorily,
conclude by reading and following chapter
4.3.11 Checking the slide function
Danger!
Wear respiratory protection in order to avoid inhaling
particles which can be hazardous to health! Brake
pad wear produces dust which can cause lung dam-
age!
Caution!
●
Take care when using chemicals and/or cleaning
tools (e.g. knives, brushes, etc.). This to avoid
damage or displacement of hoses, seals and
other components.
●
Use a vacuum cleaner to clean the surfaces. Do
not use compressed-air.
Fig. 31 -
Free mobility of the brake calliper, must be able to slide
freely on the guide pin.
prior to inspecting the
slide function.
2. Once the brake pads are removed, move the
brake calliper by hand back and forth to check its
movement,
3. If the movement is restricted in any way, the cause
must be determined, see chapter
.
4.
If the fault finding concludes that the slide function
needs to be replaced, follow chapter
ing the slide function assembly“
.
5. Once the inspection is completed satisfactorily,
conclude by reading and following chapter
.
Note:
Restriction of the slide function can lead to opera-
tional impairment, e.g. hot brakes and uneven brake
pad wear.
4.3.12 Measuring the bearing clearance
Fig. 32 -
Inside position of the brake calliper
1. Move the brake calliper by hand as far as possible
in the direction of the arrow,
Fig. 33 -
Dial gauge on the brake calliper
2. Clean the measuring point and place the dial
gauge on the support (arrow).