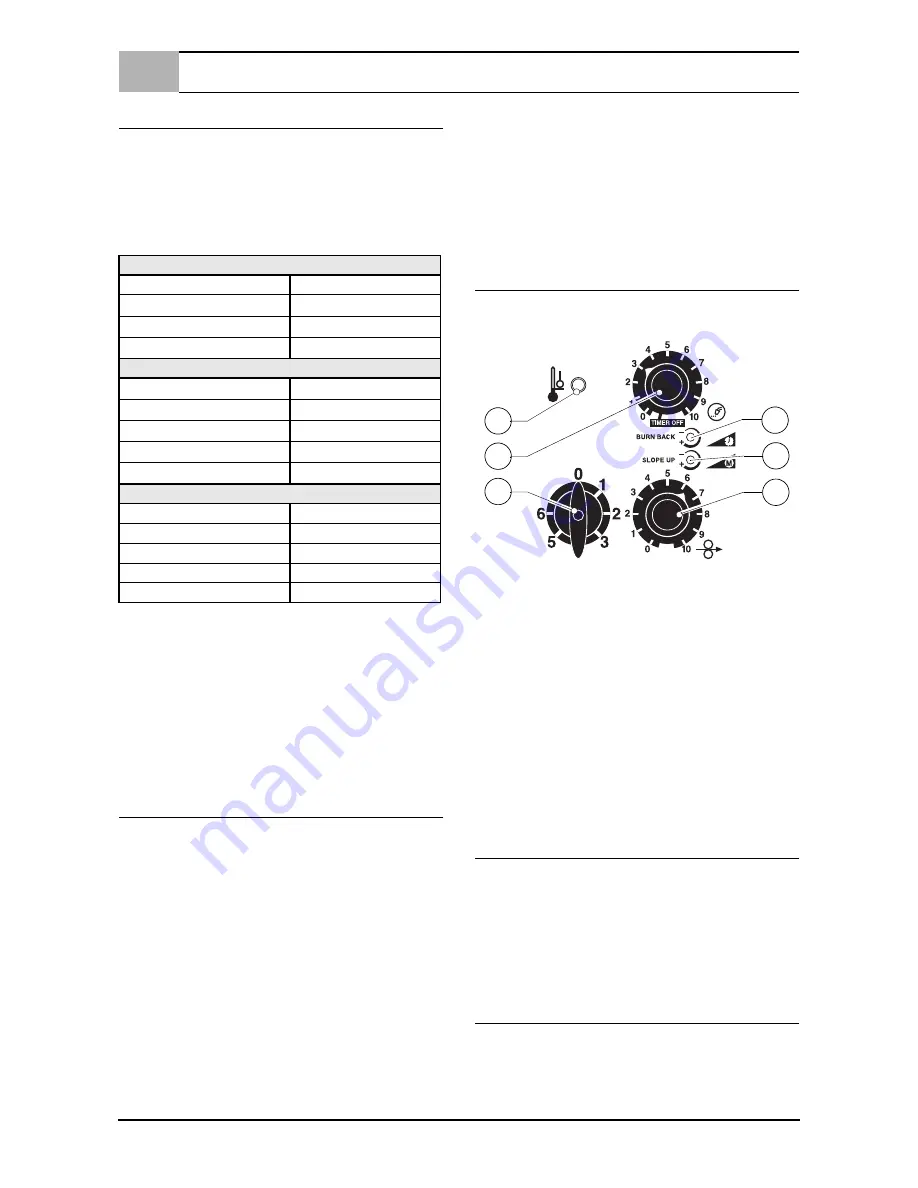
DESCRIPTION AND TECHNICAL DATA
3 EN
EN
1.0
DESCRIPTION AND TECHNICAL DATA
1.1
DESCRIPTION
MIG welders which can weld flux cored gasless wire or with gas
for the welding of mild steel, stainless steel and alumini um. MIG/
MAG welder swhich can weld mild steel, stainless steel and alu-
minium.
1.2
TECHNICAL DATA
DATA PLATE
1.3
DUTY CYCLE AND OVERHEATING
Duty cycle is the percentage of 10 minutes at 40°C ambient tem-
perature that the unit can weld at its rated output without overheat-
ing. If the unit overheats, the output stops and the over
temperature light comes On. To correct the situation, wait fifteen
minutes for unit to cool. Reduce amperage, voltage or duty cycle
before starting to weld again. Example: 140A-20% it means that
the duty cycle at 140A is 2’ with a pause of 8’.
1.4
VOLT-AMPERE CURVES
Volt-ampere curves show the maximum voltage and amperage
output capabilities of the welding power source. Curves of other
settings fall under curves shown. See page IV.
2.0
INSTALLATION
IMPORTANT: ALWAYS READ SAFETY STANDARDS CARE-
FULLY PRIOR TO CONNECTING, PREPARING OR USING
THE EQUIPMENT.
2.1
CONNECTING THE POWER SOURCE TO THE POW-
ER SUPPLY
THE FOLLOWING OPERATION MUST BE PERFORMED BY A
QUALIFIED TECHNICIAN.
BEFORE CONNECTING THE POWER SOURCE, check that
the power supply corresponds to machine Amp and voltage
specifications (see technical data table).
Always earth the equipment using the YELLOW-GREEN wire.
Any extension cords connected to power wiring must be at least
equal to the machine wiring size.
CHECK that the socket is sufficiently protected by fuses and cir-
cuit breakers. Connect an approved type plug to the machine
power leads commensurate to the machine type.
2.2
POWER SUPPLY
The preset power supply specifications of the machine are shown
on the adhesive label near the power supply cable, as well as on
the table on the power source.
2.3
PREPARING FOR USE
In concomitance with the critical conditions of the mains supply,
the power supply to the welder could cause interference to the
supply of other electrical equipment in the vicinity. Always assess
the extent and consequences of interference (e.g. to computer
and general electronic equipment malfunctioning) prior to com-
mencing work.
3.0
FUNCTIONS
3.1
FRONT PANEL
Picture 1.
1.
Wire speed regulator.
2.
Welding time regulator.
3.
ON and power selector.
4.
Thermal protection
5.
Wire feed motor acceleration time control potentiometer.
6.
Control potentiometer to regulate time during which welding
power is maintained after the relative shutdown signal. In
practice, at the end of welding, if this time is too short, the
wire remains stuck in the bath or protrudes too far from the
torch contact tube; otherwise, if the control time is too long,
the wire remains stuck in the torch contact tube, often caus-
ing damage to the latter.
NOTICE: GENERAL SWITCH (REF. 3 - PICTURE 1 PAGE 3.)
WOULDN’T ACT DIRECTLY ON THE THERMAL PROTECTION
LED (REF. 4 - PICTURE 1 PAGE 3.) . THAT WOULD SWITCH
ON ONLY IN CASE OF THERMOSTATIC PROTECTION MEA-
SURE. IN THIS PHASE WELDING IS NOT POSSIBLE UNTIL
THE PILOT LAMP GOES OFF AGAIN.
4.0
BASIC INFORMATION REGARDING MIG
WELDING
MIG WELDING PRINCIPLES
MIG welding is autogenous, i.e. it permits welding of pieces made
of the same metal (mild steel, stainless steel, aluminium) by fu-
sion, while granting both physical and mechanical continuity.
The heat required for melting is generated by an electric arc that
strikes between the wire (electrode) and the piece to be welded.
A shield gas protects both the arc and the molten metal from the
atmosphere.
5.0
CONNECTION AND PREPARATION OF
EQUIPMENT FOR WELDING
CONNECT WELDING ACCESSORIES CAREFULLY TO AVOID
POWER LOSS OR LEAKAGE OF DANGEROUS GASES.
CAREFULLY FOLLOW THE SAFETY STANDARDS.
Check gas outlet; turn gas cylinder knob to regulate flow.
PRIMARY
Single phase supply
230 V
Frequency
50 Hz / 60 Hz
Effective consumption
7,5 A
Maximum consumption
24 A
SECONDARY
Open circuit voltage
18 ÷ 32 V
Welding current
30 ÷ 170 A
Duty cycle 18%
140 A - 21V
Duty cycle 60%
75 A - 18 V
Duty cycle100%
60 A - 17 V
Protection class
IP 21
Insulation class
H
Weight
Kg 38,5
Dimensions
440 x 670 x 750
European Standards
EN 60974.1 / EN 60974.10
1
6
5
4
3
2