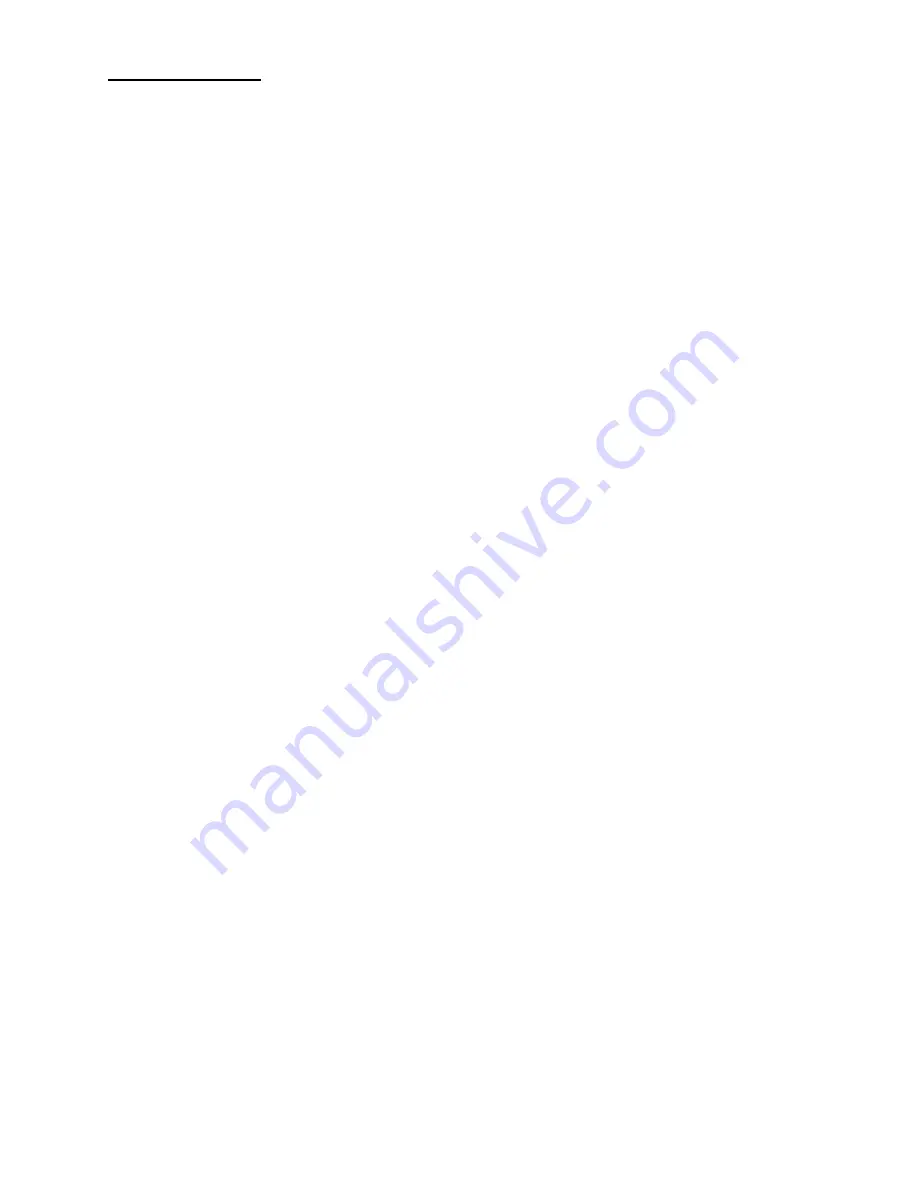
-25-
19.
TROUBLESHOOTING
Machine Always Needs Adjustment
There are several things that can cause your machine to need adjustment.
1. Cutter wheel may be dull. This can cause the key to try to ―float‖ and not cut deep enough in the deepest
cuts. Replace or resharpen the cutter.
2. Carriage spring may be weak or adjusted to light. Replace the spring or adjust the spring.
3. Stylus may be worn. Check it carefully, if there is a groove worn in the stylus you may get deep and shallow
cuts on different brands of keys. For example when cutting Ford double sided keys the ignition key will be
cut high on the stylus and the door key will cut low on the stylus – Schlage C keys are cut more in the mid-
dle of the stylus. This may seem like an extreme case – but it happens every day. Replace the stylus.
4. Carriage shaft and bearings are worn. Check for excess ―wobble‖. Replace the carriage shaft and bronze
Oilite ® bearings.
5. Cutter shaft bearings are worn. Check for any ―wobble‖ or in-out play. Replace the cutter shaft assembly.
6. One key cuts fine and the next doesn’t. You adjust and readjust all the time. The problem may be the car-
riage depth over travel adjustment is set too high. This results in the machine’s inability to cut the deepest
cuts on a key – but shallower cuts are fine. This symptom is more common than you think. Fix the problem
by readjusting the Carriage Over travel Depth Adjustment. See page 22 for Overtravel Adjustment.
7. Again – one key cuts fine and the next one doesn’t. This time it may be the key gauges. Sometimes key
machine operators don’t flip down the full-function key gauges all the way down and the left-hand key gauge
CRASHES into the stylus holder and knocks the key gauges out of position. The key they’re cutting is O.K.
but the next key they duplicate won’t work in the lock. If you ever CRASH the left-hand key gauge into the
stylus holder – fix the key gauges right away. See Key Gauge Adjustment for how to do it. See page 21 for
Key Gauge Adjustment.
8. Keys don’t always work in the lock when gauged off the bottom shoulder stop. This is a common problem
caused by the key blank manufacturers. In recent years many of the key blank manufacturers have stopped
paying attention to the bottom shoulder stop on most key blanks since they are seldom used by the lock cyl-
inder. We’ve seen Schlage C key blanks with variations of up to 15 thousandths of an inch (.015‖) between
top and bottom shoulder positions – between keys taken from the same box. It happens more often than
you think. The solution? Don’t bottom shoulder gauge your keys anymore.
Cutter Stalls Out
There are six possible causes for this problem.
1. You are cutting keys from Tip-to-Bow. This one can fool you if you’re not careful. Cutting keys from tip to
bow will work when you cut only shallow keys—sometimes a shop can cut keys all day long and never hit
upon a key with a deep cut. You think everything is O.K. when all of a sudden your cutter stops dead half-
way along the key. The problem? The deep cut put the cutter into the key past the cutter tooth area on the
left side of the cutter—you just reinvented the disk brake!
SOLUTION—ALWAYS CUT FROM BOW-TO-
TIP.
2. Oil on the belt and pulleys. Clean the pulleys with safety solvent and install a new drive belt.
3. Left-hand nut securing the cutter wheel isn’t tight.
4. Belt tension needs to be increase and/or replaced the drive belt.