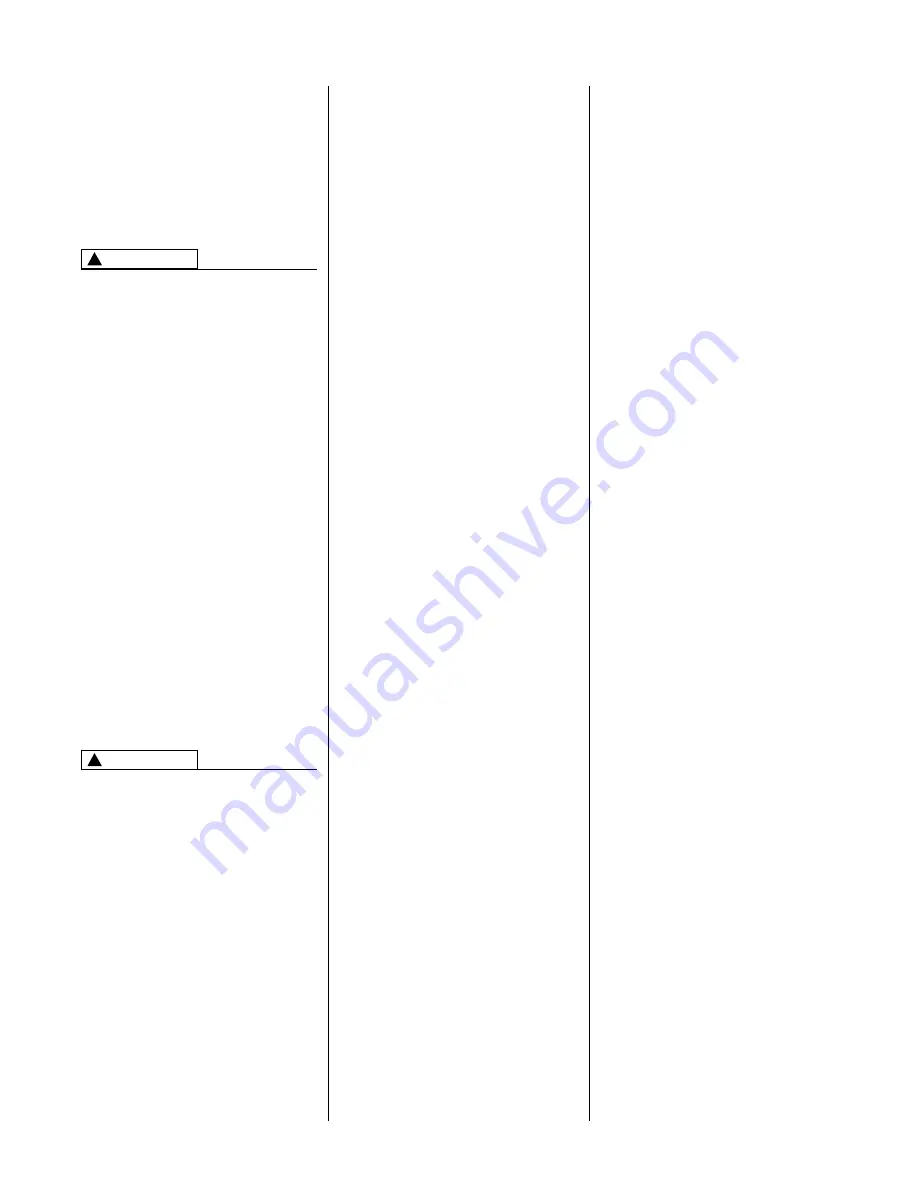
26
DIRECT SPARK IGNITION
LIGHTING INSTRUCTIONS
This appliance is equipped with a
direct spark ignition device. This device
lights the main burners each time the
room thermostat (closes) calls for heat.
See lighting instructions on the
furnace.
TO START FURNACE
1.
BE SURE THAT THE MANUAL
GAS CONTROL HAS BEEN IN
THE “OFF” POSITION FOR AT
LEAST FIVE MINUTES. DO NOT
ATTEMPT TO MANUALLY LIGHT
THE MAIN BURNERS. FAILURE
TO FOLLOW THIS WARNING CAN
CAUSE A FIRE OR AN
EXPLOSION RESULTING IN
PROPERTY DAMAGE,
PERSONAL INJURY OR DEATH.
2. Set the room thermostat to the
lowest setting.
3. Turn the gas control knob to the
“On” position, or move the gas
control lever to the “On” position.
4. Replace the control access door.
5. Turn on the electrical power.
6. Set the room thermostat to a point
above room temperature to light the
main burners. After the burners are
lit, set room thermostat to a desired
temperature.
TO SHUT DOWN FURNACE
1. Set the room thermostat to its
lowest setting.
2. Shut off the gas to main burners by
turning the gas control knob to the
“Off” position, or by depressing the
gas control lever and moving it to
the “Off” position.
SHOULD OVERHEATING OCCUR
OR THE GAS SUPPLY FAIL TO
SHUT OFF, SHUT OFF THE
MANUAL GAS VALVE TO THE
APPLIANCE BEFORE SHUTTING
OFF THE ELECTRICAL SUPPLY.
FAILURE TO DO SO CAN CAUSE AN
EXPLOSION OR FIRE RESULTING
IN PROPERTY DAMAGE,
PERSONAL INJURY OR DEATH.
Sequence of operation with a single
stage thermostat
a. Connect the “W” terminal on the
thermostat to the W2 terminal on the
control board.
b. When there is a call for heat, the “R”
and “W2” contacts close and the
IFC runs a self check routine to
verify that the pressure switch
contacts are open. The limit switch
contacts are constantly monitored.
START-UP PROCEDURES
WARNING
!
WARNING
!
c. The induced draft motor starts on
high until the low pressure switch
contacts close (a maximum of 60
seconds), and then changes to low
speed. After a 30 second pre-purge,
the spark ignitor energizes and the
low stage of the gas valve opens,
lighting the burners.
d. After the gas valve opens, the
remote flame sensor must prove
ignition for one second using the
process of flame rectification. If the
burners do not light, the system
goes through another ignition
sequence. It does this up to 4 times.
(2 tries on low fire and 2 tries on
high fire.)
e. The main blower starts on low
speed 20 seconds after the burners
light. The furnace operates on low
fire for 12 minutes and then, if the
thermostat is not satisfied, shifts to
high fire, causing the draft inducer to
go to high speed, the gas valve to
100% and the main blower goes to
heat speed.
f. When the thermostat cycle ends, the
gas valve closes, and the burners
go out.
g. The draft inducer will continue
running for a 10 second (low speed)
or 5 second (high speed) post
purge.
h. The main blower will run for 90
seconds on high speed or 120
seconds on low speed. (This timing
is field adjustable, for 60, 90, 120 or
150 seconds). See Figure 21 for
switch settings.
Sequence if the system doesn’t light
or doesn’t sense flame:
a. If flame is not sensed within 8
seconds after the gas valve opens,
the valve closes and the ignitor is
de-energized. The induced draft
motor will run for 60 seconds on low,
stop momentarily, and then restart.
b. The ignition process goes through
one more try on low fire. If this fails,
there are two tries on high fire with a
30 second interpurge between trials.
During high fire ignition attempts,
the inducer steps to high speed, the
high pressure switch closes (both
pressure switches are now closed),
and the gas valve steps to 100%.
c. If there is no ignition after the 2nd
trial on high fire, the furnace goes
into soft lockout for one hour.
d. The sequence repeats after a one
hour delay and continues repeating
until ignition is successful or the call
for heat is terminated.
e. To reset the lockout, make and
break power either at the thermostat
or at the unit disconnect switch for 5
to 10 seconds. The furnace will then
go through another set of trials for
ignition.
f. If flame is established and
maintained during the trial for
ignition period and flame is lost, the
gas valve is de-energized, the draft
inducer completes a post-purge of
10 seconds. The indoor blower
motor will be energized and/or
remain energized on low speed for
low fire and heat speed for high fire
for the selected delay off time.
When the inter-purge delay is over,
the control verifies the pressure
switch has opened and then initiates
another ignition trial period. The
control will recycle up to 5 flame
losses (4 re-cycles) within a single
call for heat before going into
lockout.
Sequence of operation with two
stage thermostat
Connect W1 and W2 terminals on the
thermostat to W and W2 terminals on
the control board.
Call for 1st stage heat
a. R and W thermostat contacts close
and the control module runs a self-
check routine. After the control
module verifies that both sets of
pressure switch contacts are open,
the induced draft motor starts on
high until the low pressure switch
contacts close (a maximum of 60
seconds), then changes to low
speed.
b. After a 30 second pre-purge, the
spark igniter energizes and the gas
valve (low stage) opens, lighting the
burners.
c. After the burners light, the remote
flame sensor must prove ignition. If
the burners do not light, the system
goes through another ignition
sequence. It does this up to 4 times
(2 tries on low fire and 2 tries on
high fire).
d. The main blower starts on low
speed 20 seconds after the gas
valve opens. The furnace continues
to run on low until the call for heat is
satisfied or the 2nd stage contacts
close. If the 1st stage call for heat is
satisfied the gas valve closes and
the induced draft motor continues
running for a 10 second post purge
time. the main blower runs for 120
seconds (this timing is field
adjustable). See Figure 23 for switch
settings.
Call for 2nd stage heat after 1st
stage
R and W2 thermostat contacts close,
calling for 2 stage heat. The induced
draft motor then switches to high
speed and the high pressure switch
contacts will close. The gas valve
switches to high fire and the main
blower switches to heating speed.
Содержание (-)GLL Series
Страница 29: ...29 FIGURE 23 COOLING HEAT PUMP OFF DELAY PROFILES ST A0827 01...
Страница 30: ...30 FIGURE 24 COOLING HEAT PUMP ON DELAY PROFILES ST A0828 01...
Страница 31: ...31 FIGURE 25 LOW HEAT OFF DELAY PROFILES ST A0829 01...
Страница 32: ...32 FIGURE 26 HIGH HEAT OFF DELAY PROFILES ST A0830 01...
Страница 37: ...37 FIGURE 32 FILTER RETAINING RODS SIDE RETURN FIGURE 33 DOWNFLOW FILTER INSTALLATION...
Страница 39: ...39 FIGURE 34 INTEGRATED FURNACE CONTROL IFC TROUBLESHOOTING GUIDE FOR UTEC 1095 101...
Страница 40: ...40...
Страница 41: ...41 FIGURE 35 FOR MODELS WITH UT ELECTRONIC CONTROLS 1095 101 INTEGRATED FURNACE CONTROL AND ECM BLOWER MOTOR...
Страница 42: ...42...
Страница 43: ...43...
Страница 44: ...44 CM 1105...