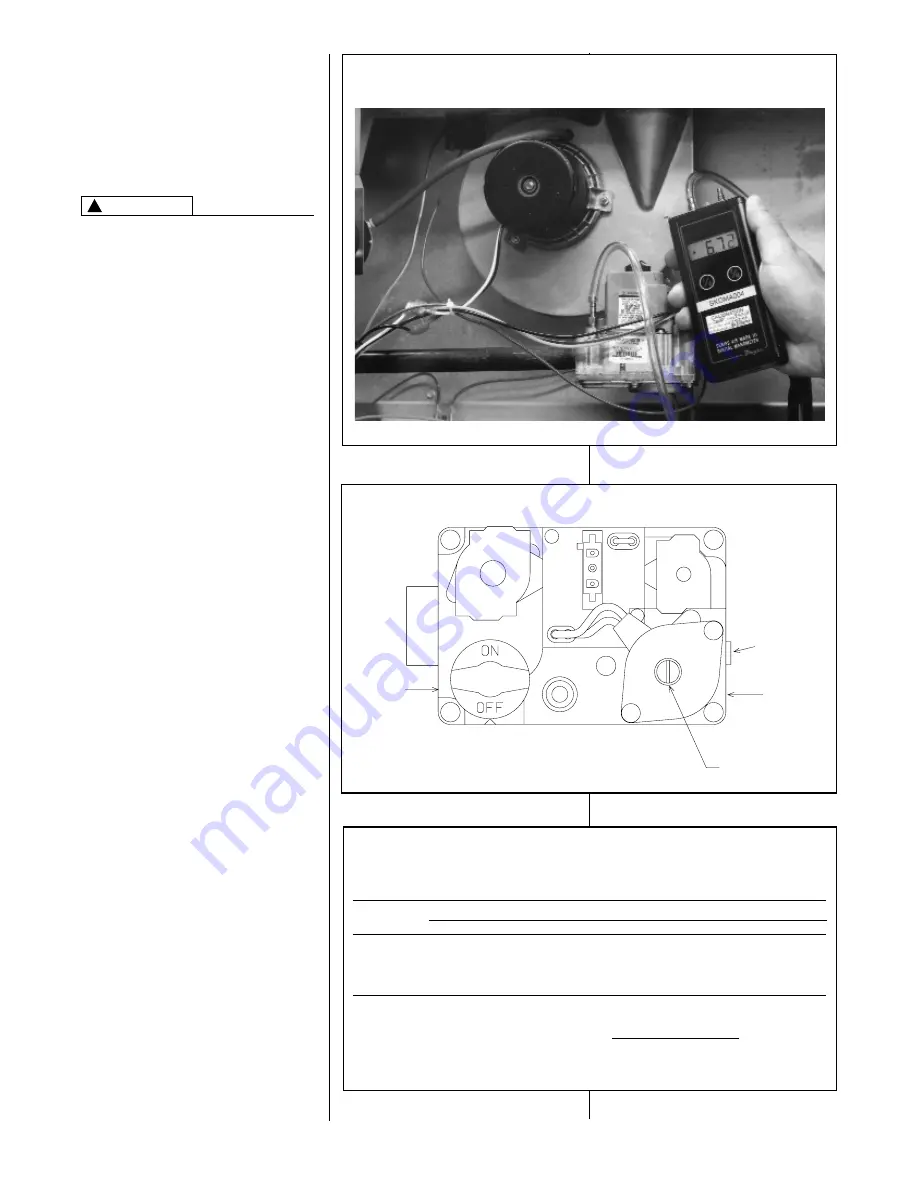
18
SETTING GAS PRESSURE
The maximum gas supply pressure to
the furnace should be 10.5
”
w.c.
natural gas, or 13
”
w.c. LP gas. The
minimum supply gas pressure to the
gas valve should be 5" w.c. natural gas
or 11" w.c. LP gas. A properly
calibrated manometer is required for
accurate gas pressure measurements.
ELEVATIONS ABOVE 2000 FT
REQUIRE THAT THE FURNACE
INPUT RATING BE ADJUSTED AND
THAT THE SIZE OF THE BURNER
ORIFICES BE RE-CALCULATED
BASED ON ELEVATION AND GAS
HEATING VALUE. THE BURNER
ORIFICES MAY (OR MAY NOT)
NEED TO BE CHANGED. SEE THE
SECTION TITLED “HIGH ALTITUDE
INSTALLATIONS” OF THIS BOOK
FOR INSTRUCTIONS.
Manifold Gas Pressure
Measurement. Natural gas manifold
pressure should be 3.5" w.c.; LP gas
manifold pressure should be 10"
w.c.
Only small variations on gas
pressure should be made by adjusting
the pressure regulator.
1. With the gas shut off at the manual
gas valve, remove the pressure
tap plug in the gas manifold or the
gas valve outlet. See Figure 26.
2. Connect a U-Tube manometer to
this pressure tap. See Figure 27.
3. Turn on the gas supply and
operate the furnace in high speed.
4. Note or adjust the manifold gas
pressure to give:
A. 3.5" w.c. for natural gas high fire.
B. 10" w.c. for LP gas high fire.
5. To adjust the pressure regulator
for high fire, remove the regulator
cap located on the
side of the
regulator. See Figure 14.
6. Turn the adjustment screw
clockwise to increasre pressure or
counterclockwise to decrease
pressure.
7. Securely replace the regulator cap
for high fire.
8. Operate the furnace in low speed.
9. Note or adjust the manifold
pressure to give:
A. 1.7" w.c. for natural gas low fire.
B. 4.9" w.c. for LP gas low fire.
10. To adjust the pressure regulator
for low fire, remove the regulator
cap
on the top of the regulator.
See Figure 14.
11. Turn the adjustment screw
clockwise to increase pressure or
counterclockwise to decrease
pressure.
12. Securely replace the regulator cap
for low fire.
TABLE 2
NATURAL GAS PIPE CAPACITY TABLE (CU. FT./HR.)
Capacity of gas pipe of different diameters and lengths in cu. ft. per hr. with pressure drop of 0.3 in. and specific
gravity of 0.60 (natural gas).
Nominal
Length of Pipe, Feet
Iron Pipe
Size, Inches
10
20
30
40
50
60
70
80
1/2
132
92
73
63
56
50
46
43
3/4
278
190
152
130
115
105
96
90
1
520
350
285
245
215
195
180
170
1-1/4
1,050
730
590
500
440
400
370
350
1-1/2
1,600
1,100
890
760
670
610
560
530
After the length of pipe has been determined, select the pipe size which will provide the minimum cubic feet per hour
required for the gas input rating of the furnace. By formula:
Gas Input of Furnace (BTU/HR)
Cu. Ft. Per Hr. Required
=
Heating Value of Gas (BTU/FT3)
The gas input of the furnace is marked on the furnace rating plate. The heating value of the gas (BTU/FT3) may be
determined by consulting the local natural gas utility or the LP gas supplier.
FIGURE 14
TYPICAL GAS VALVE
INLET
PRESSURE
TAP
OUTLET
PRESSURE
TAP
HIGH FIRE
MANIFOLD
PRESSURE
ADJUSTMENT
LOW FIRE
PRESSURE
MANIFOLD
ADJUSTMENT
FIGURE 13
TYPICAL HOSE CONNECTION TO LINE PRESSURE TAP
!
CAUTION
Содержание (-)GLL Series
Страница 29: ...29 FIGURE 23 COOLING HEAT PUMP OFF DELAY PROFILES ST A0827 01...
Страница 30: ...30 FIGURE 24 COOLING HEAT PUMP ON DELAY PROFILES ST A0828 01...
Страница 31: ...31 FIGURE 25 LOW HEAT OFF DELAY PROFILES ST A0829 01...
Страница 32: ...32 FIGURE 26 HIGH HEAT OFF DELAY PROFILES ST A0830 01...
Страница 37: ...37 FIGURE 32 FILTER RETAINING RODS SIDE RETURN FIGURE 33 DOWNFLOW FILTER INSTALLATION...
Страница 39: ...39 FIGURE 34 INTEGRATED FURNACE CONTROL IFC TROUBLESHOOTING GUIDE FOR UTEC 1095 101...
Страница 40: ...40...
Страница 41: ...41 FIGURE 35 FOR MODELS WITH UT ELECTRONIC CONTROLS 1095 101 INTEGRATED FURNACE CONTROL AND ECM BLOWER MOTOR...
Страница 42: ...42...
Страница 43: ...43...
Страница 44: ...44 CM 1105...