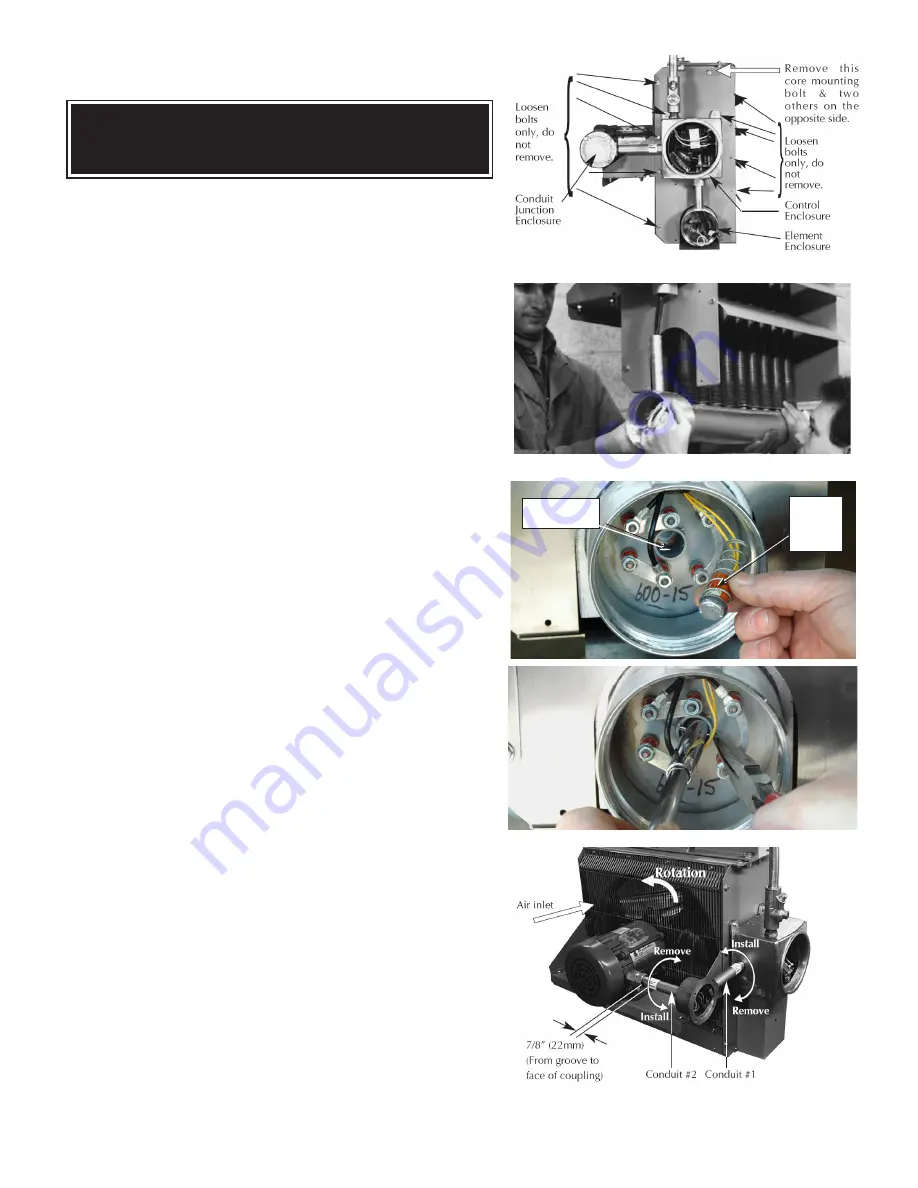
- 12 -
REPAIR & REPLACEMENT
1. After repairing any component:
a. check that electrical connections are correct and secure (see Figure 8),
b. remove any foreign material from enclosures,
c. install and secure all covers,
d. ensure that all fasteners are tight,
e. remove all foreign objects from heater, and
f. ensure air exits through louvers and fan rotates counterclockwise when
viewed from rear of heater (see Figure 13).
C O R E
The heater core is vacuum charged and not field repairable.
For core removal:
1. Remove cabinet bottom and element enclosure cover.
2. Disconnect all wires entering element enclosure (see Figure 9).
3. Slightly loosen all cabinet bolts shown in Figure 9, to prevent the core
from binding.
4. With an assistant supporting the weight of the core, remove the 3 core
mounting bolts. Carefully lower the core out of the cabinet (see Figure
10).
5. To return core to factory, use crate supplied with exchange core to protect
the element terminals and plate threads.
6. To reinstall, lift the core up into cabinet while an assistant guides the
element wires into the element enclosure conduit.
7. Position the core and tighten the 3 core mounting bolts. Tighten the
remaining cabinet bolts.
T E M P E R AT U R E H I G H - L I M I T
1. Remove temperature high-limit assembly and clean the inside of the
thermowell (see Figure 11). A clean thermowell will ensure good thermal
contact.
2. Use only a factory supplied temperature high-limit to ensure safe operation.
(refer to the instructions that accompany the replacement Temperature
High-Limit kit).
3. Reinstall the temperature high-limit assembly with the snap ring and spring
into the thermowell without damaging the insulating tube. Secure in place
with the cotter pin (see Figure 12).
MOTOR, FAN & FAN GUARD
1. Remove bolts holding the motor to the motor mount. On units with a built
in thermostat, remove the bolts on the back of the thermostat enclosure.
2. Remove conduit #1 located between motor junction box and control
enclosure by turning it in the direction illustrated (see Figure 13).
Note conduits #1 and #2 are not interchangeable and have left hand threads on
one end, this end is indicated by a machined groove.
3. Remove the 2 piece fan guard assembly (see Figure 14).
4. Lift the motor assembly off the motor mount.
5. Before removing the fan, measure and record the location of the fan hub on the
motor shaft (see Figure 15). If difficult to remove, use a gear puller on the fan hub.
6. To reassemble, place motor assembly onto motor mount and fasten the fan guard
to cabinet.
7. Simultaneously engage and tighten both ends of conduit #1 into enclosures.
Leave a 1/16” to 3/16” (1.6 to 4.8 mm) gap between the motor and fan guard (see
Figure 16). Adjust conduit #2 to center the fan in the shroud.
8. To ensure a minimum 5 thread engagement, threaded ends of conduits must
protrude a minimum of 1/16” (1.6mm) into enclosures. The groove on conduit #2
must not be more than 7/8” (22mm) from motor coupling (see Figure 13).
9. Bolt motor to motor mount. Manually spin the fan blade to ensure fan rotates freely.
10. Air must exit through louvers and fan must rotate counterclockwise when viewed
from rear of heater (see Figure 13).
FIGURE 13
FIGURE 12
FIGURE 11
FIGURE 10
FIGURE 9
3/32”
(2mm)
Drop
Thermowell
WARNING
Disconnect heater from power supply at fuse box before opening enclosures or
servicing heater. Lock the switch in the “OFF” (open) position and/or tag the switch to
prevent unexpected power application.
Содержание FX4 Series
Страница 14: ... 14 NOTES ...
Страница 15: ... 15 NOTES ...