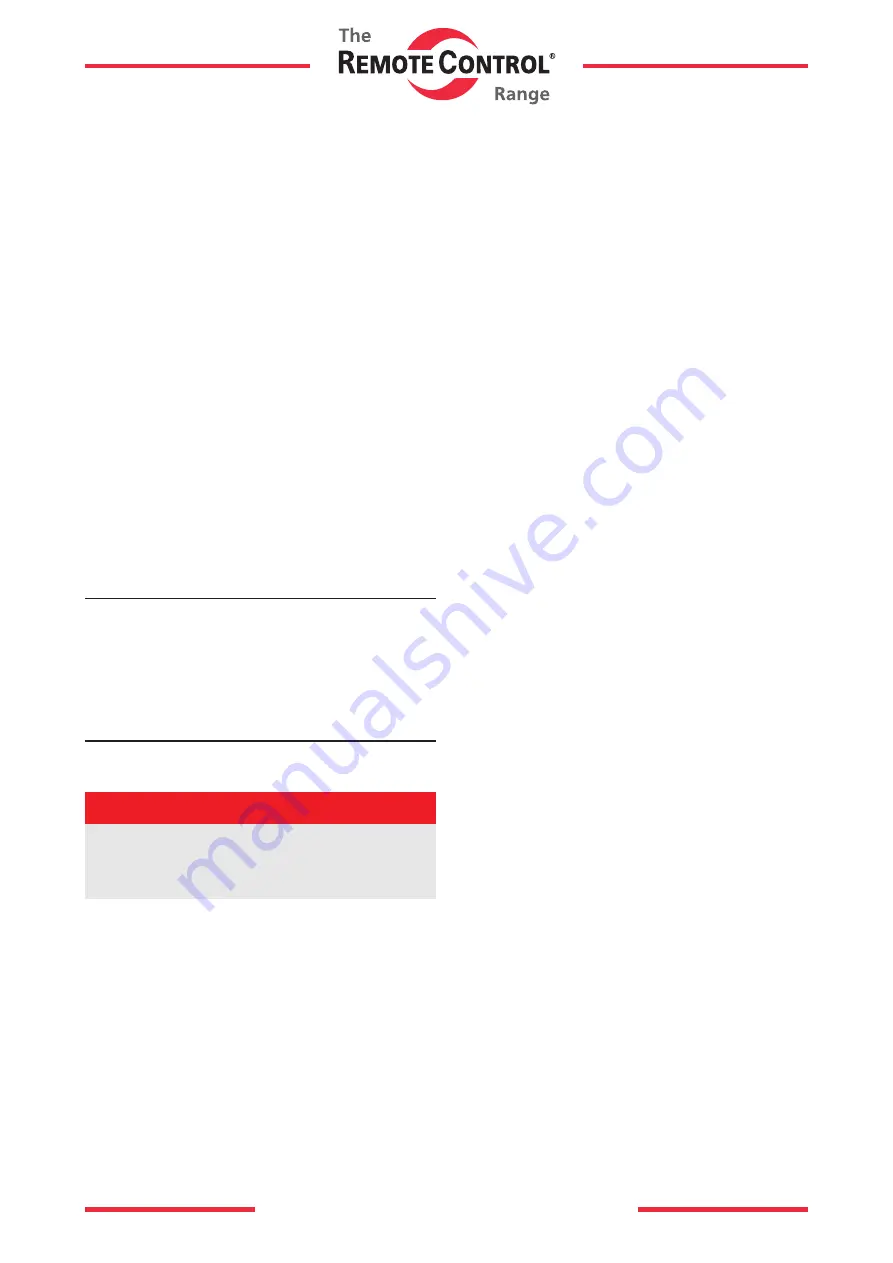
- 6 -
E4L
E4
H
L
H
L
RC210
90
68
120
68
RC220-RC265
90
110
120
110
RC270-RC280,
RC88
100
160
130
160
RCG90-RCG100 155*
200*
185*
200*
Tabell 14pt bold
Bold på rubriker uppe, allt under ska vara regular.
Allt utom spalten med RC-förteckningar ska vara
centrerat i våg och lodrätt. RC-spalten ska vara
vänsterlagd.
Strl på texten varierar beroende på utrymme men
10pt är standard
www.rotork.com www.remotecontrol.se
Trouble shooting
3.
If the motor (6:S1, 7:S) does not operate: Disconnect the
air pipe between motor and steering valve (4:S).
If air flow to the motor is blocked: Check the steering
valve. Push the levers (4:S/10 &13) and at the same time
pressurize the inlet port (4:S/9). The shafts (4:S/3) should
be pushed in about 1,5 mm when the turning direction
changes. If not, then the setting position of the levers on
the shafts should be adjusted with screw 4:S/7.
4.
If the levers (2:S1/5) hook up on the motor shaft (6:S1/5
or 7:S/5) by a change over operation, this depends on an
instantaneously change over operation. The operating
cylinder (GDS1:1/12) has started to change over the turn
-
ing direction from open to close or vice versa, before the
motor has vented and the shaft fully returned to its outer
position. This can be cured like this:
a) Try to avoid instantaneously change over operations,
by allowing a mean time of 1 to 2 seconds to vent the
control valves.
b) Fit the motor with a quick exhausting valve.
c) Introduce some kind of a change over signal time
delay.
5
.
If air blows through the front port of the diaphragm casing
(6:S1/1), the diaphragm is bursted. Change diaphragm
according to instruction.
6.
If the motor operates very quick but with short strokes:
Close the needle valve (GDS1:1/19). Then slowly open
until the motor operates normal. If this doesn’t help, there
is probably dirt in the valve mechanism (6:S1/ and
7:S/17-30).
Unscrew the valve casing (6:S1 and 7:S/31). Carefully
take out and clean the valve mechanism. Be careful when
cleaning the rubberized valve seats. If the motor does not
operate and air blows through the rear exhaust port, carry
out the same procedure as described above for cleaning
the valve mechanism.
7.
Try to manually operate the valve and make sure it does
not seize or jam. Eventually the valve stem might have
seized or the stem gland is over tightened.
Risk for injuries caused by crushing/squeezing and
electrical shocks when the actuator is energized by air
pressure and electricity with its cover off.
WARNING!
The actuator is provided with two lubrication nipples for a
grease gun. When the actuator is in regularly daily opera
-
tion, lubrication should be performed at intervals of some
weeks. It is to be borne in mind however that the inter
-
vals of lubrication are dependent on local conditions, for
example, the frequency of operation, the temperature and
surrounding atmosphere etc.
If the actuator is used only infrequently, it should be lubri
-
cated with grease which doesn´t get hard, or change vis
-
cosity when in contact with the surrounding atmosphere.
The lubrication of the actuators in this case could be
carried out during normal maintenance on the other equip
-
ment. It is recommended that the actuator is inspected at
regular intervals for preventative purposes.
It is not possible to give general instructions as to the
intervals of inspection, as these are dependent on local
conditions. We would suggest the following points could
be checked, and if necessary, lubricated with some drops
of oil.
1) Spindle thread and axle journals of the indicator bridge.
2) The oil holes of the axle journals, 2:S1/ 4+20
3) The pin for the draw-spring, 2:S1/6
4) The case for the ratchet spring, 2:S1/2
5) The stop shoulder, 2:S1/18
1.
Check that air supply is available at the actuator and that
the pressure does not vary too much (See Page 2, Instal
-
lation).
2.
Check the actuator for functional faults. Remove the cover
and make an ocular inspection. Open and close the valve.
It is very important that the increased starting torque is
correctly adjusted. Check that the console (2:S1) oper
-
ates accordingly to the torque diagram (see technical data
sheet).
The motor shaft shall actuate outer part of the operating
lever. If not, see Adjustment of Indicator Bridge (Page 5).
Transport and storage
Keep the actuator in the original packaging until use. The
actuators shall be stored at room temperature and protect
-
ed from dirt and humidity. Air connections must be plugged.
For long storage, exercise actuators annually.
Maintenance