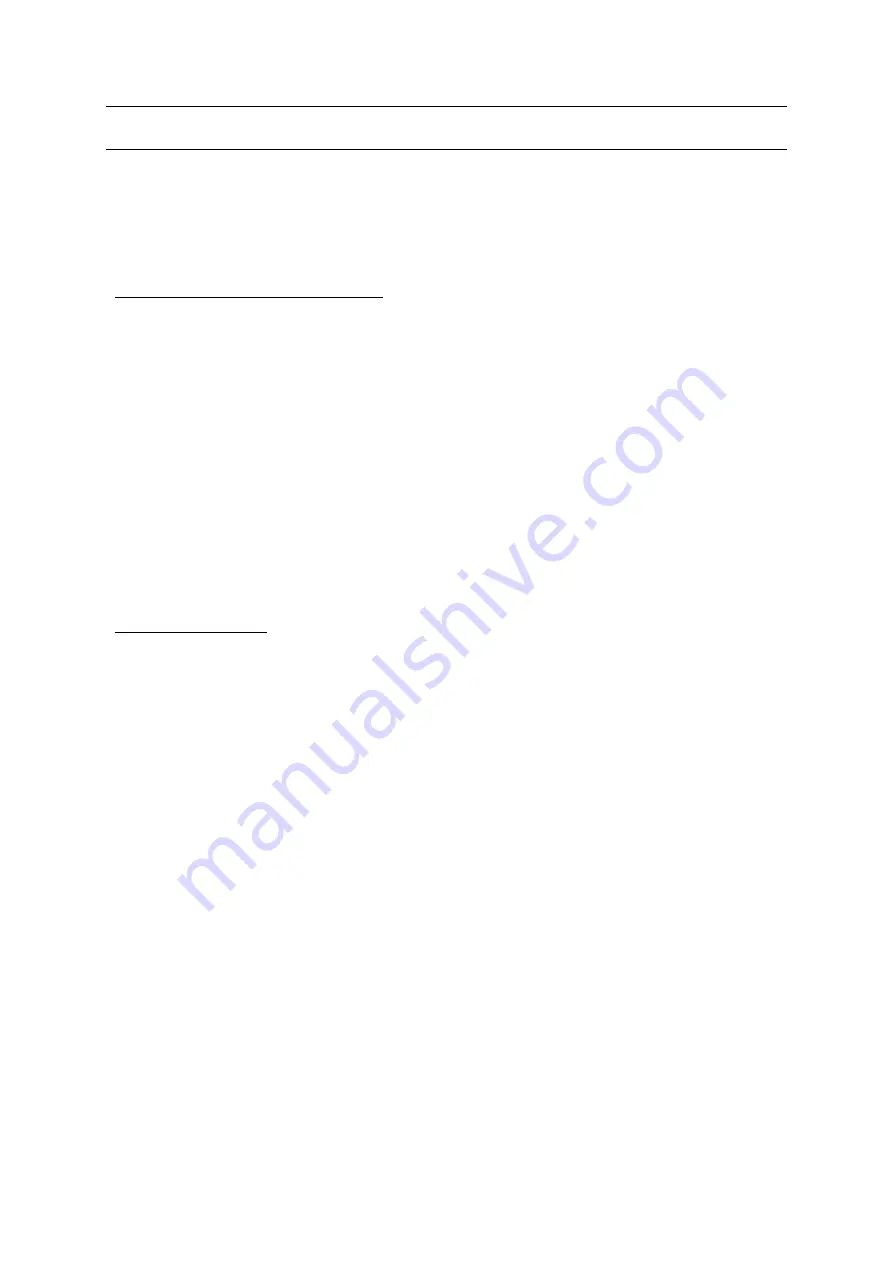
Pakscan IIS Technical Manual Issue 1.0
Publication S130E 61
10. COMMISSIONING THE SYSTEM
IMPORTANT SAFETY PRECAUTIONS
In order to fully commission the Pakscan Loop it is necessary to ensure that all the system's valves are allowed
to be opened and closed. Also any ancillary devices such as pumps and stirrers must be allowed to operate.
Without this capability it is impossible to check all the functions of the total system.
It may be that valve movement and pump operation is not permissible as the plant may already be operational
in a manual mode. In this case it will only be possible to test out parts of the Pakscan system. However if the
connected field units are to operate devices on a 'live' plant it is vital to secure the connected equipment into a
safe state. Make sure that the connected actuators are in Local control or locked in 'Hand' (as this will prevent
them from moving under Pakscan control) and any other plant equipment connected to field units is either able
to be operated safely, or that the outputs are prevented from operating the connected equipment. Don’t forget
that an actuator set to Local will still respond to an ESD signal and may move the valve. It is also advisable to
ensure that all the connected equipment is safe, for example in Local Stop, whenever the loop is re-configured.
The plant should only be returned to its original state once the loop is operating correctly.
Commissioning of sequences should only be attempted after the loop has been successfully commissioned.
BEFORE YOU START
In checking the loop resistance and capacitance the operating loop baud rate was determined. This baud rate
must be set as the operating speed for ALL the connected field units. Note that the 'Doubling' option described
in 9.3 above is an independent function, the baud rate selection is made on the cable parameters present.
Set all the field units to match the master station Loop Baud Rate.
10.1 Checking Individual Field Units.
Use a Paktester to verify that each and every field unit is correctly set for Baud rate and Address. Where there
are options for the setting of the field unit make sure these are adjusted correctly. Refer to the Paktester
manual (R5161-016) for information regarding these adjustments. All field units, including those simply used
for full open and full close duty, report analogue values for valve position. The Analogue Update Time and
Deviation settings should be set to turn off this reporting, or to maximum. If these parameters are not correctly
set then the field unit will be sending analogue messages far to often and slow down the remaining data
comms.
Pay particular attention to selecting the correct function for General Purpose field units, and also for the
settings for Analogue Update times and Deviation settings for all field units where analogue data is collected.
Make sure that no two field units on the loop have the same address, and that no field unit has an address set
higher than that selected as 'the highest address' - see section 9.3.
When setting and checking a field unit remember that the Paktester will only communicate to one field unit at
a time, the one to which it is connected. Also remember that the address and baud rate can only be altered if
the field unit is in loopback.
Содержание Pakscan IIS
Страница 1: ...Publication S130E Issue 1 0 23 June 1996 Pakscan IIS Master Station Technical Manual...
Страница 4: ...4 Publication S130E Issue 1 0 Pakscan IIS Technical Manual...
Страница 8: ...8 Publication S130E Issue 1 0 Pakscan IIS Technical Manual This page is intentionally left blank...
Страница 12: ...12 Publication S130E Issue 1 0 Pakscan IIS Technical Manual This page is intentionally left blank...
Страница 60: ...60 Publication S130E Issue 1 0 Pakscan IIS Technical Manual This page is intentionally left blank...
Страница 68: ...68 Publication S130E Issue 1 0 Pakscan IIS Technical Manual This page is intentionally left blank...
Страница 72: ...72 Publication S130E Issue 1 0 Pakscan IIS Technical Manual This page is intentionally left blank...
Страница 83: ...Pakscan IIS Technical Manual Issue 1 0 Publication S130E 83 This page is intentionally left blank...