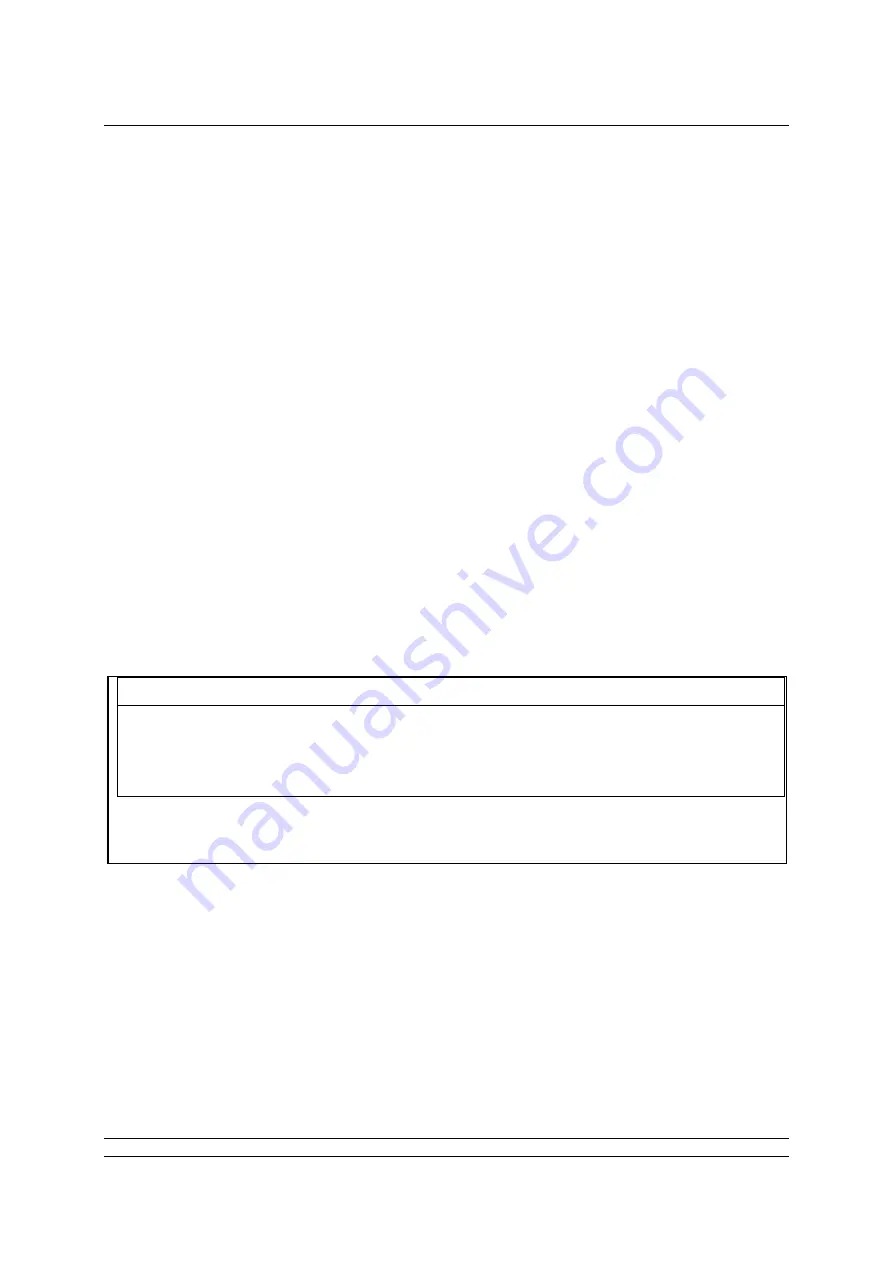
Input and Output Signals
Publication
PUB091-004-00_0918
29 of 64
has the control input applied. Both open and close interlocks are
enabled or disabled at the same time. If interlocking is required in only
one direction, it will be necessary to fit a link between the terminals
associated with the other interlock. Refer to wiring diagram.
Partial Stroke Test
If a network command to perform a partial stroke test is
sent to an IQ3 actuator, it will carry out the test sequence provided the
actuator has been set up to perform partial stroke testing. The
actuator must be set to Remote and be at the correct end limit set for
partial stroking. The actuator will also carry out a partial stroke test if a
signal is applied to the open interlock input, if the Interlock
configuration has been set to Partial Stroke. In both cases, partial
stroke data will be reported over Modbus.
5.1.1
Controls Priority
Since there are three potential sources for control inputs, the actuator and Modbus Module assign a
priority for those occasions when two or more commands are applied simultaneously.
In addition, the remote control hard wired inputs can be used as discrete input signals, to report the
status of other devices or as control inputs. The associated Auxiliary Input Mask parameter must be
set to select the required function. In the case of the hard wired input for ESD this can be configured
either as an ESD/DI-
4 signal or as a ‘Modbus Command Inhibit’ to prevent network control signals
from moving the actuator.
High Priority
Low Priority
Local Stop
Local Close
Hard Wired Close
Modbus Close
Local Open
Hard Wired Open
Modbus Open
Hard Wired ESD
Hard Wired Stop
Modbus Stop
Modbus ESD
Modbus Position
Modbus Partial Stroke
Mechanically interlocked to prevent both at the same time.
The IQ3 can be set so that Local Stop has a higher priority than ESD.
Only one Modbus command is possible at a time.
If a Modbus command is applied while Hard Wired Stop is present, stop is cancelled.
Fig 16:
IQ3 Control Priorities
5.1.2
Modbus Control using Individual Coil commands
The open, close, stop, ESD and DO-1 to DO-4 controls can be written using function code 05 or 15 to
write to single or multiple coils. Writing the value FF00 turns a coil on and 0000 turns it off. The MFU
provides a degree of intelligence in operating the coils for the open, close, stop and ESD functions.
When one coil is turned on, all the others are turned off, so only one can be on at a time. The actuator
will obey the last command it receives, so if two writes using function code 05 follow each other closely
the later one will win.