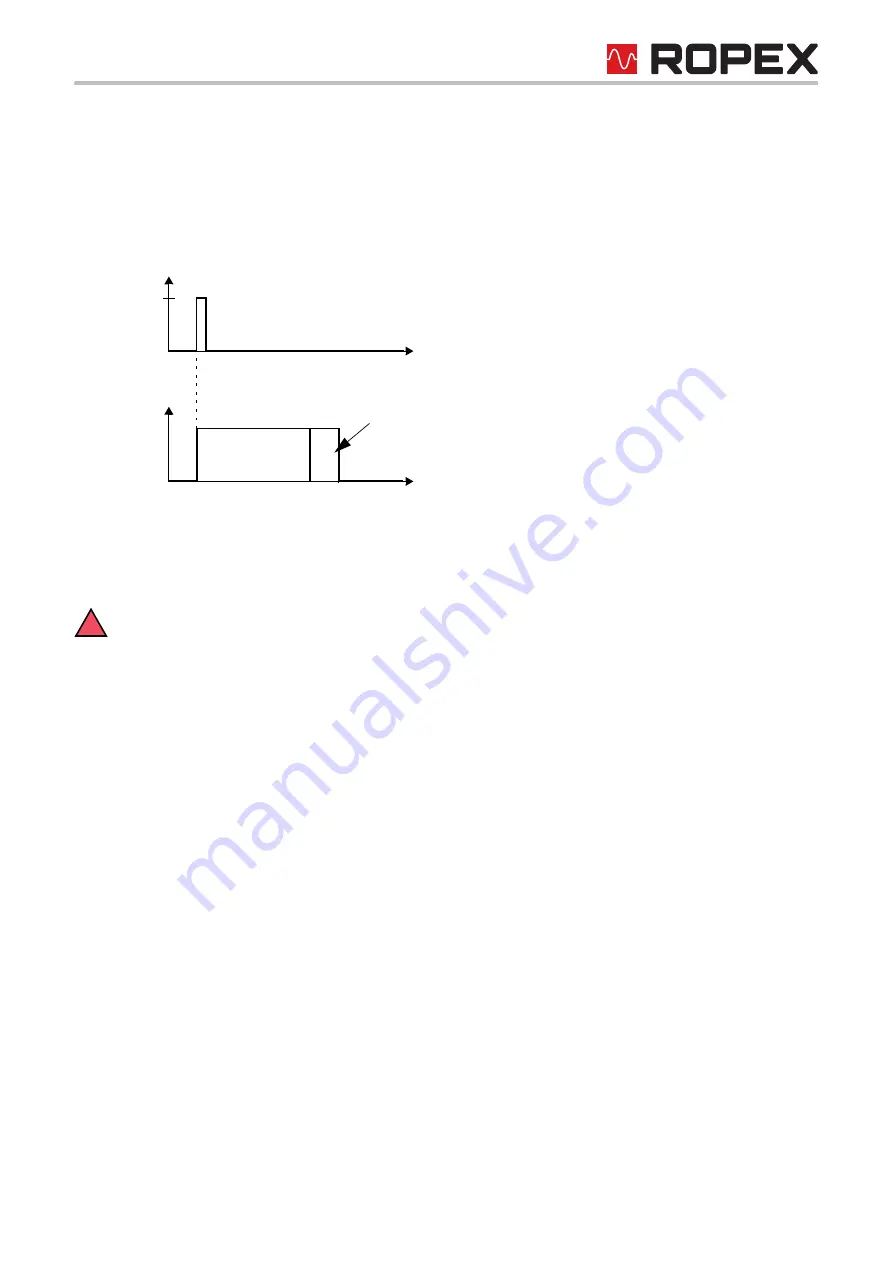
Controller functions
Version 1
RES-406
Page 39
The "OUTPUT" LED blinks repeatedly when the "AUTOCOMP" function is executed and the actual value
output (terminals 17+14) is set to 0…3°C (i.e. app. 0 VDC).
3.
„AUTO“ (as of software revision 105)
With this setting the „AUTOCOMP“ function is activated automatically after the "AUTOCAL" function has been
successfully executed.
The "OUTPUT" LED blinks repeatedly when the "AUTOCOMP" function is executed and the actual value
output (terminals 17+14) is set to 0…3°C (i.e. app. 0 VDC).
The "AUTOCOMP" function must be activated by means of the PROFIBUS parameter data
(
section 7.7 "Parameter data" on page 34) or the DPV1 protocol extension (
protocol extension (as of GSD Version v2.0)" on page 42).
(default setting: AUTOCOMP off)
7.7.11 Temperature diagnosis (as of GSD Version v2.0)
An additional temperature diagnosis can be activated by means of the PROFIBUS parameter data or the DPV1
protocol extension.. The RES-406 checks whether the ACTUAL temperature is within a settable tolerance band
("OK" window) on either side of the SET temperature. The lower (
) and upper (
) tolerance band
limits are the same like in the „Temperature OK“ function (
section 7.6.5 "Temperature OK (TO)" on page 31).
The limits are configured in the factory to -10K and +10K.
If the actual temperature is inside the specified tolerance band when the "START" signal is activated, the temper-
ature diagnosis is activated as well. If the ACTUAL temperature leaves the tolerance band, the corresponding error
code (307 or 308) is indicated and the alarm relay is switched (
section 7.16 "Error messages" on page 49).
Function
AUTOCAL
bit
„AC“
t
t
0
0
AUTOCAL
AUTOCOMP
1
!
Δϑ
lower
Δϑ
upper