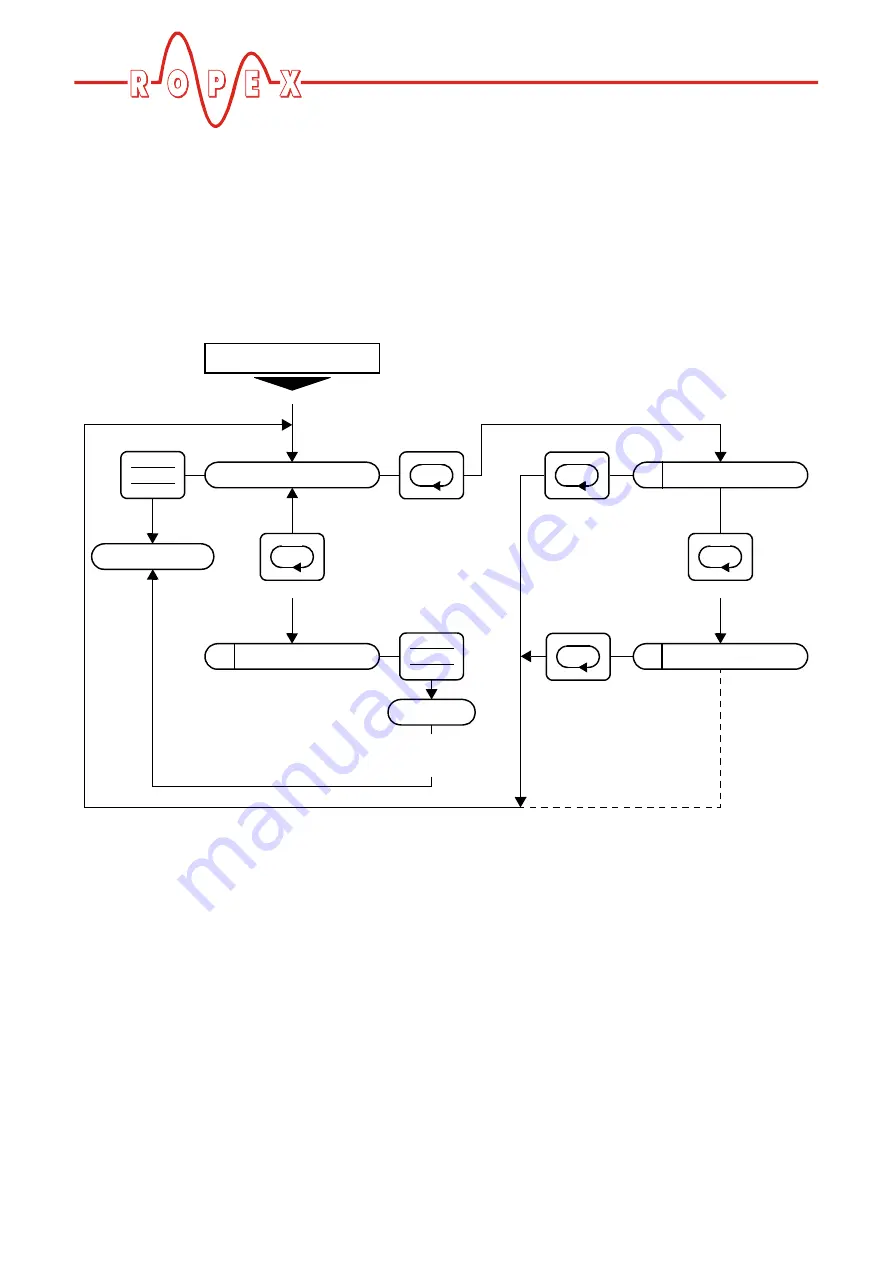
Controller functions
Page 30
RES-430
10.3.2 Navigation in menus with an alarm
If an alarm is signaled, the controller switches to the
Alarm menu. Some faults can be acknowledged by
pressing the "RESET" key (
ª
ª
ª
ª
monitoring / alarm output" on page 42). In this case, the
controller switches back to the home position.
If the fault can be rectified by executing the AUTOCAL
function, you can select the "AUTOCAL" menu step
directly by briefly pressing the "MENU" key (<2s). You
can then activate the "AUTOCAL" function by pressing
the "ENTER" key (
ª
calibration (AUTOCAL)" on page 35).
If you press the "MENU" key for longer than 2s in the
Alarm menu, you are taken directly to the configuration
level (starting at step 201). You can return from the
Configuration menu to the Alarm menu either by
pressing the "MENU" key for longer than 2s or by not
pressing any keys for 30s.
201
Language
Alarm
<2s
>2s
<2s
Alarm
automatically
after 30s
>2s
or
automatically
after 30s
>2s
or
ENTER
HAND
RESET
ENTER
HAND
RESET
Home position
End of
Autocal
107
202
Factory settings