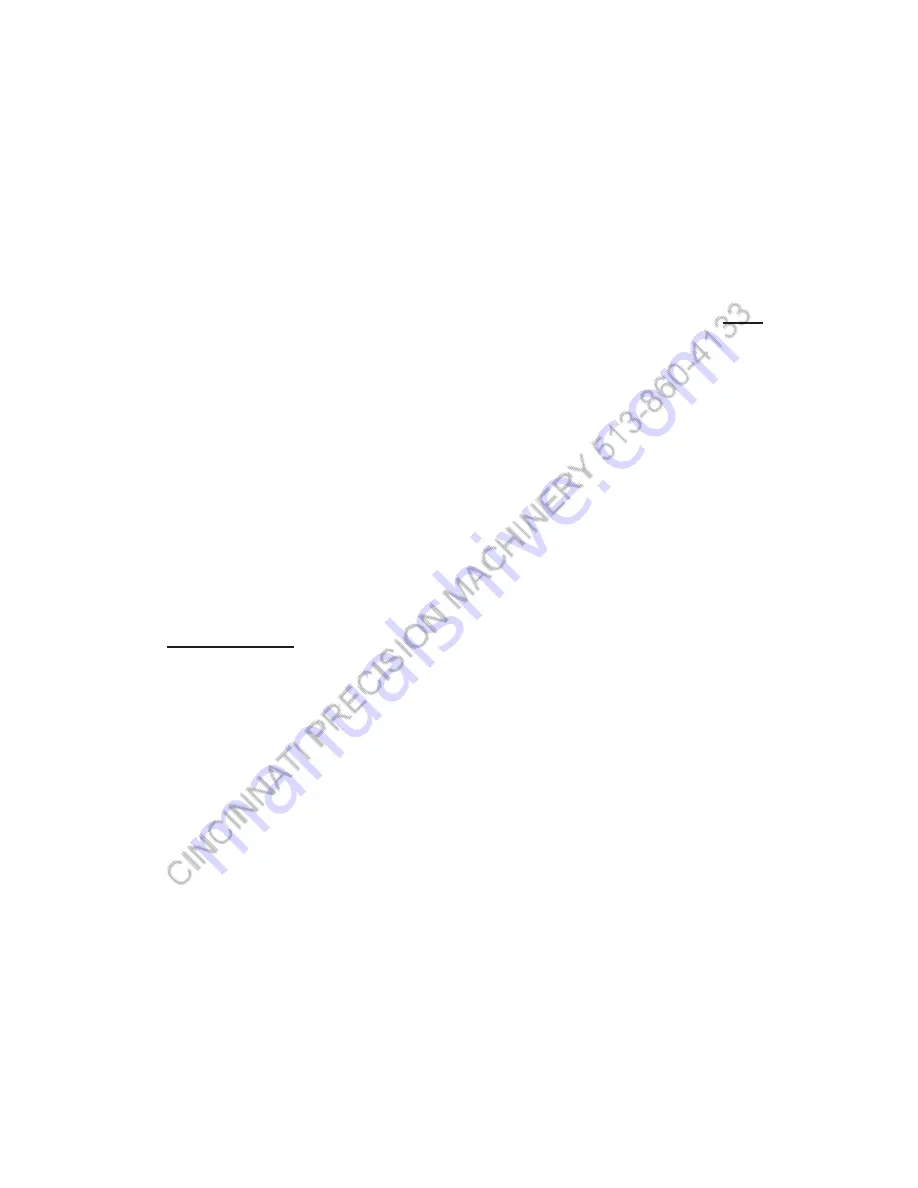
INSTRUCTIONS
MODEL U412 CONNECTICUT FLOOR BRAKE
Level the Brake and shim under the feet to avoid distortion. Fasten firmly in place. The front feet must be
well fastened to avoid tipping when bending force is applied to handles. See special notes on leveling
Floor Model Hand Brakes.
The Model U412 is rated for bending 48” of 12 gauge mild steel, 1 inch flange, with bending angle and
bending bar fastened securely in place. The beam (upper clamping member) may be adjusted to the
rear a maximum of 1 1/8”. When adjusting to bend 12 gauge material, swing the apron up to 90 degrees
and set the beam adjustment to allow a clearance of 3/16” between the apron edge and the radius bar.
For lighter material, a clearance of 1 1/2 to 2 times material thickness should be used. Soft aluminum
may be formed with clearance equal to material thickness.
Rated capacity for stainless steel is 16 gauge. Clearance should be at least twice material thickness.
Removing the bending angle for narrow or offset bends, reduces capacity to 16 gauge mild steel. Re-
moving both bending angle and bending bar reduces capacity to 20 gauge. Avoid using the brake
without the bending bar as much as possible as the bar is made of tough material to protect the apron
edge from wear.
Clamping pressure is controlled by nuts on the lower end of the toggle bolt. This pressure should be
adjusted with a small piece of material to be bent clamped in each end of the machine. Move the nuts so
that the levers (No. 10 & 11), pull against the stops with an equal effort. Excessive clamping pressure is
not required. Use only enough to hold the material firmly in the brake.
These Brakes are not intended for bending rods, wires, multiple thicknesses or across lock seams.
Operations of this type will result in denting the edge of the apron and springing the machine out of line.
Lubricate the moving parts of the machine with light grease or heavy oil. Lasting accuracy depends on
proper lubrication.
SPECIFICATIONS
Length of bed
48”
Capacity on mild steel, 1” flange,
With bending bar and angle in place
12 ga.
With bending angle removed
16 ga.
With bending bar and angle removed
20 ga.
Minimum reverse bend (bar & angle removed)
1/4”
Maximum lift of beam
1 5/8”
Front to rear adjustment of beam
1 1/8”
Finger Widths
3”, 4”, 5”
Maximum depth of box
6”
Shipping weight
1400 lbs.
Packing
Wood skids & blocking
-5-
Содержание U412
Страница 8: ...EXAGGERATED VIEW OF CROWN FROM REAR OF BRAKE FIG I FIG II 8 ...
Страница 9: ... 9 ...
Страница 10: ... 10 ...