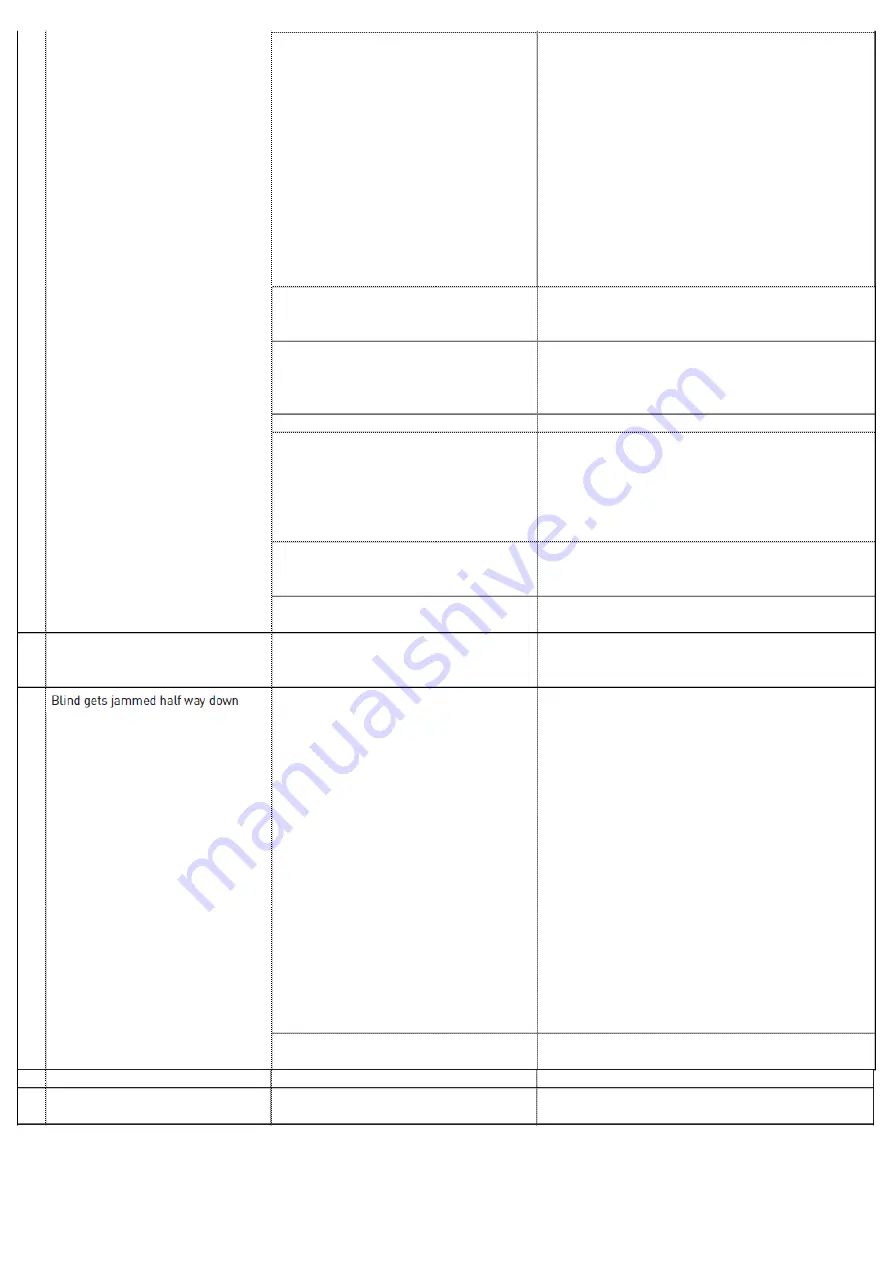
Page
13
of
14
Zipscreen Installation Manual | v4.2| August 2019
2019 ©Copyright All Rights Reserved Rollease Acmeda
2
Troubleshooting continued…
NO. PROBLEM
CAUSE
SOLUTION
1
Prominent smile across fabric
Not enough tension in side guides
Cut new fabric skin and weld zip onto fabric ensuring
temperature is not too hot. Refer to Assembly manual for
welding tips.
Fabric is not installed straight
Ensure fabric is assembled straight onto tube and weight
bar.
2
Ripples along sides of fabric
Blind rolled up for extended
This occurrence is inherent to roller systems and is more
period of time
prevalent in some fabrics. Leave blind down for 1-4 hours –
most ripples should disappear
Fabric not central to system
Remove rivets around the ripple area and reposition inner
rail and secure
Too much tension in inner rails
Check fabric is centred with system. If the fabric is not centred
with the system, centre the fabric. The Side Rails may
need to be removed to correct. If fabric cannot be centred,
check scallop in fabric is large enough for installation
(refer to Assembly manual for scallop sizes). If the fabric at
the scallop is flush with the edge of the tube and the fabric
cannot move sideways any further, increase size of scallop
in fabric.
Fabric is too wide for installation
Check actual installation width dimension matches the
measured blind width.
If the installation width does not match the measured blind
width:
• Correct installation width to match measured blind width
or
• Correct fabric width to correct size (based on actual
installation width)
Note: Tube and weight bar may also require correcting.
If the installation width matches the measured blind width:
Check overall fabric width from external zip edge to external
zip edge and ensure it is W-66mm (W being completed blind
width).
If required, correct fabric width.
Not enough weight in weight bar.
Refer to product specs. Add ballast.
Note: for spring operated blinds, the number of pre-turns
will most likely need to be increased.
Spring operated blinds
It is more common for there to be some ripples in spring
operated blinds.
To reduce the number of ripples evident, pull the blind
down softly and lock into position.
Not enough pre-turns in spring
Increase number of pre-turns on spring.
Installation is not square
Check overall width of U-mounting rail and inner rail is
within 42-62mm.
Check inner rails are level & parallel. If either of the above
checks are not in accordance with specifications, the
installation space requires additional packing. The side rails
or entire systems may need to be removed to correct.
Fabric permanently damaged due to
Replace the fabric and ensure it is handled
inadequate handling during assembly,
with care.
transportation, installation or use
Fabric is not installed straight
Ensure fabric is assembled straight onto tube
and weight bar
3
Small ripples close to weld
Welding temperature is too high on zip
Cut new fabric skin and weld zip onto fabric
ensuring temperature is not too hot.
Refer Assembly manual for welding tips.
4
Weight bar end cap hits Inner Rail
Check there is always approximately 3mm
(0.12”) gap between Weight Bar End Cap and
Inner Rail.
If there is insufficient clearance, check:
• Actual installation width dimension matches
the measured blind
width
• The weight bar length is cut in accordance
with the deductions
outlined by Acmeda
If the installation width does not match the
measured blind width:
• Correct installation width to match measured
blind width
or
• Trim weight bar length to correct size (based
on actual installation
width)
Note: Tube and fabric may also require correcting
Fabric is not installed straight
Ensure fabric is assembled straight onto tube
and weight bar.
5
Spring operated blind is heavy to push up Not enough pre-turns
Increase number of pre-turns on spring.
6
Spring operated blind is stuck and will not Spring pre-tension Idler has not been
Ensure pre-tension Idler is unlocked on both
move
un-locked.
ends of system.
7
Motorised blind jolts during operation
Motor rotates blind continuously whilst a
This occurrence is inherent to the motorised
wind gust causes additional friction in Inner
system and no damage will be caused as a
Rail and stops blind momentarily.
result. If undesired, avoid operating blind in
When force of wind is reduced, the additional
windy conditions.
friction is removed and blind drops.
Not enough weight in weight bar
Add ballast to weight bar.
8
Cannot install inner rail into
Weight bar length is too long
Check actual installation width dimension
blind to feed zip
matches the measured blind width.
If the installation width does not match the
measured blind width:
• Correct installation width to match measured
blind width
or
• Trim weight bar length to correct size (based
on actual installation width)
Note: Tube and fabric may also require correcting
Inner rail length is too long
Check actual installation drop dimension matches the
measured blind drop.
If the installation drop does not match the measured blind
drop:
• Correct installation drop to match measured blind drop
or
• Trim inner rail length to correct size (based on actual
installation
width)
Note: U-mounting rail and L-fixing channel may also
require correcting
9
SB07 Weight Bar lock doesen’t
Latch has not been secured in correct position
Re-install latch so shaft locates into latch.
locate into latch
10 Uneven weight bar
Box is not level, thus weight bar appears
Ensure box is level.
uneven
Inconsistent friction along inner rails
Check inner rails are level & parallel. If the inner rails
are not level and parallel remove rivets from U-mounting
channel, reposition inner rail to reduce tension and resecure
inner rail.
Motorised blind jolts during operation
See Point 7
Zip overturns on itself
This occurrence is inherent to Zipscreen and there isn’t
currently a solution.
Fabric is not installed straight
Ensure fabric is assembled straight onto tube and weight bar.
11 Impact Detection function of
The Automate FT motor Impact Detection
Put the blind up or down, increasing the distance from the
Automate FT motor is not active.
function isn’t active in the first 20cm from
limits and verify if the motor retracts the blind when an
the upper limit and in the last 20cm from
obstacle is detected.
the lower limit.
Impact Detection function has been deactivated
Press P2, Down & Down on the remote and check the
during motor installation.
functionality of Impact Detection again.
Note: For all Automate FT15 Motor information visit the RollEase Acmeda Website:
http://www.rolleaseacmeda.com/au/products/product-detail/external-blind-motorisation-automate-ft15-motor