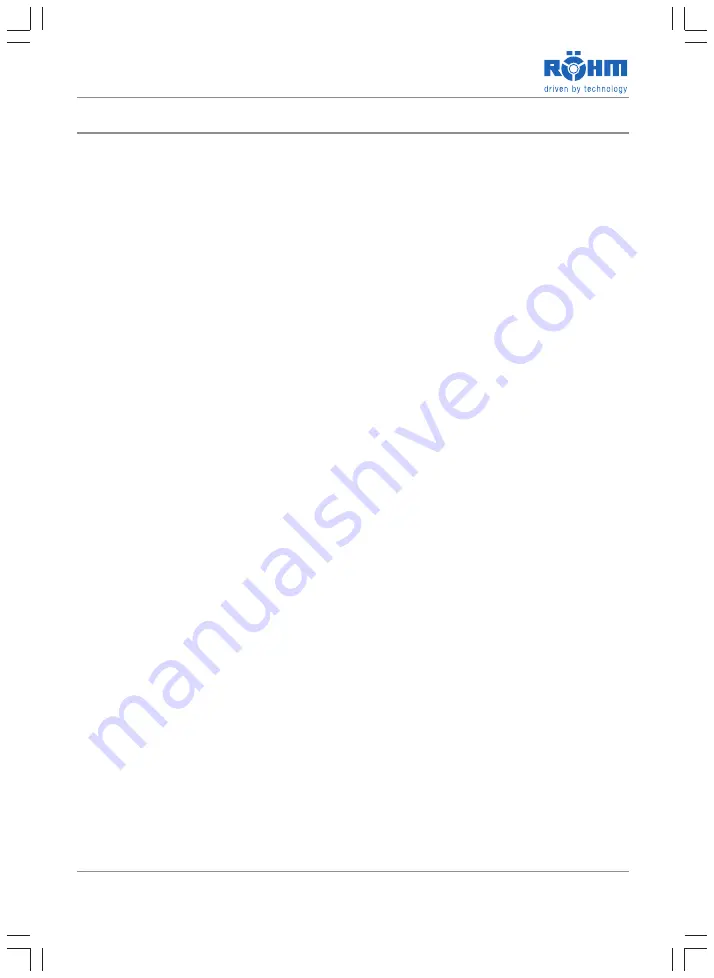
2 | Safety
16 / 48
DURO-A RC
2.6.8
Procedure in the Event of Danger and Accidents
In the event of danger and accidents, it must be ensured that first aid meas-
ures can be taken immediately.
1.
Shut the machine down immediately via the Emergency-Stop button.
2.
Remove the person involved from the danger zone and sit or lay the per-
son down.
3.
Call a doctor.
Ø
Do not make any changes to the accident site.
4.
Administer first aid.
Ø
Stop any bleeding.
Ø
Cool burns.
5.
Report all accidents to a superior.