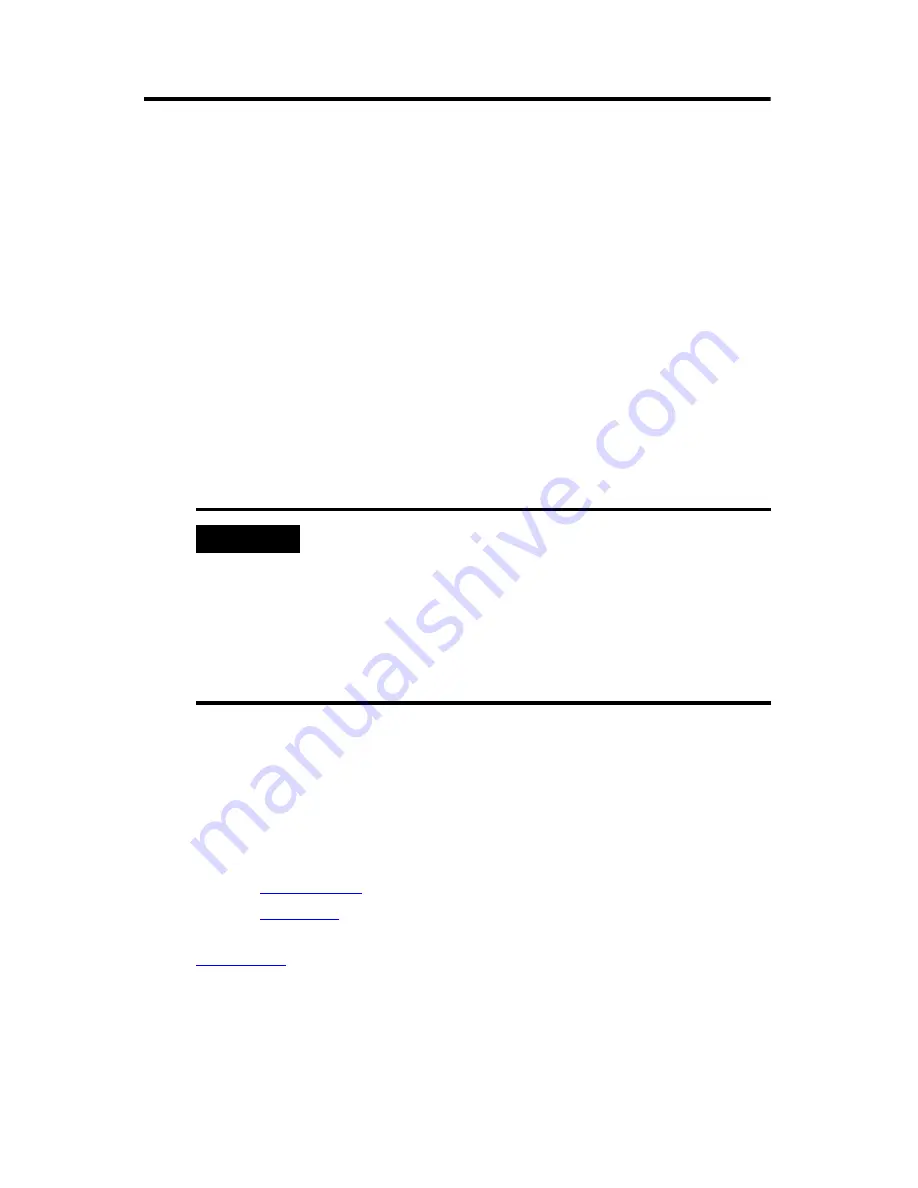
MP-Series Food Grade Servo Motor Installation Instructions
5
Publication MP-IN004D-EN-P — April 2009
• Inspect the motor and seals for damage or wear on a regular basis. If
damage or excessive wear is observed, replace the item.
• If desired, you may seal the motor front flange to the driven equipment by
applying a bead of food grade RTV around the periphery of the joint
between the motor and the machine surfaces. Use of a gasket or RTV on the
mating surfaces is not recommended, as this can cause misalignment of the
shaft and result in damage to the motor and/or driven equipment.
• The brake option on this servo motor is a spring-set holding brake that
releases when voltage is applied to the brake coil. A separate power source
is required to disengage the brake. This power source can be applied by a
servo motor controller or manual operator control.
If system main power fails, holding brakes can withstand occasional use as
stopping brakes. However, this creates rotational mechanical backlash that is
potentially damaging to the system, increases brake wear, and reduces brake
life.
Using Shaft Seals
A seal is installed on the motor shaft to protect the front bearing from fluids or fine
dust that could contaminate the motor bearing and reduce its lifetime. An IP66/IP67
rating for the motor requires the use of shaft seals, connectors, and cables that
provide an environmental seal equal to or exceeding the rating.
• Refer to
Specifications
for a brief description of the IP ratings.
• Refer to
Shaft Seals
to find the catalog numbers of seal kits for your motor.
• Refer to the Kinetix Motion Control Selection Guide, publication
GMC-SG001
, to find environmentally sealed connectors and cables that are
compatible with MP-Series motors.
IMPORTANT
Holding brakes are not designed to stop rotation of the motor shaft, nor are they
intended to be used as a safety device. They are designed to hold a motor shaft
at 0 rpm for up to the rated brake holding torque.
The recommended method of preventing motor shaft rotation is a four step
process: first - command the servo drive to 0 rpm, second - verify the motor is at
0 rpm, third - engage the brake; and fourth - disable the drive.
Disabling the drive removes the potential for brake wear caused by a badly tuned
servo system oscillating the shaft.