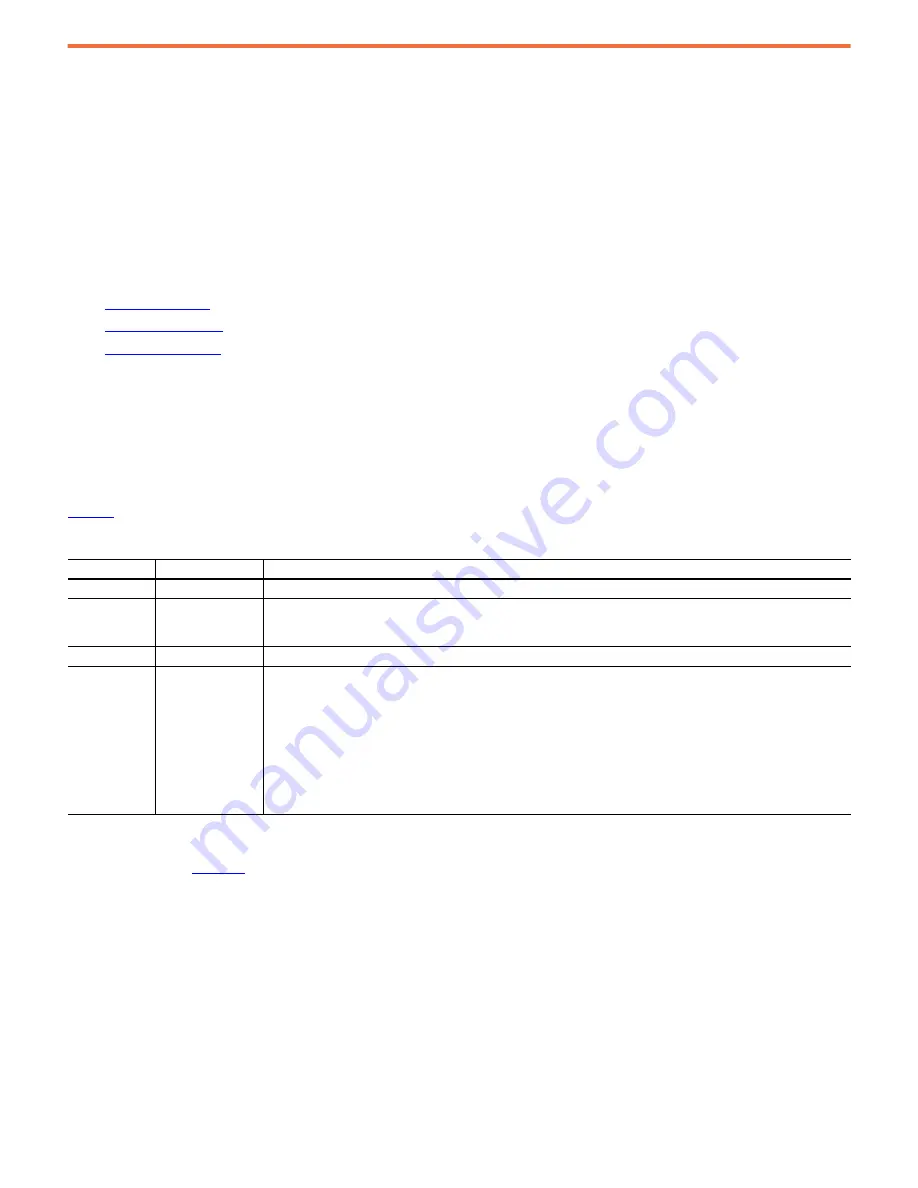
104
Rockwell Automation Publication 750-AT006D-EN-P - January 2022
Chapter 7 Applications
Process PID Controller
The internal PID function provides closed loop process control with proportional and integral control action. The function is used in
applications that require simple control of a process without the use of a separate standalone loop controller. The PID output signal can be
used to adjust the velocity or torque reference signals.
The PID function reads a process variable input to the drive and compares it to a desired reference signal or setpoint that is stored in the
drive. The algorithm then adjusts the output of the PID regulator, which changes drive output frequency to attempt zero error between the
process variable and the setpoint. Process PID parameters are located in Port 9. 0:70 [Application Sel] is used to select the application
parameters available in Port 9. You can set 0:70 [Application Sel] to ProcPID Only (1) or Torque Prove (2). The latter selection supports both
applications.
This section includes:
•
•
•
Modes
The Process PID can be used to modify commanded speed or torque. There are two ways the PID controller can be configured.
•
Speed Trim – The PID output can be added to the master speed or torque reference.
•
Exclusive Control – The PID can have exclusive control of the commanded speed or torque.
shows the parameters needed to configure the process PID controller
Speed Trim Mode
– The PID controller is summed in this mode with a master speed reference to control the process. This mode is
appropriate when the process is tightly controlled and in a stable manner by adding or subtracting small amounts directly to the speed. In
the example shown in
, the master speed reference sets the wind/unwind speed and the dancer potentiometer signal is used as a
PID feedback to control the tension in the system. An equilibrium point is programmed as the PID setpoint, and as the tension increases or
decreases during winding, the master speed is trimmed to compensate and maintain tension near the equilibrium point.
Table 37 - Process PID Controller Parameters
Parameter No.
Parameter Name
Description
9:1
[PID Cfg]
• A set of bits that selects various modes of operation. It can only be changed when the drive is stopped.
9:2
[PID Control]
• A set of bits that dynamically enables and disables the operation of the process PID controller.
• When it is interactively written to and from a network, it must be done through a data link so the values are not written to
memory.
9:3
[PID Status]
• A set of bits that indicates the status of the process PID controller.
9:14
[PID Output Sel]
Selects the mode between speed trim, exclusive control, and torque trim. Parameter values are as follows.
• Not Used (0) – PID output is not applied to any speed reference.
• Speed Excl (1) – PID output is the only reference that is applied to the velocity reference.
– Velocity reference modification applies to both vector and frequency control modes.
• Speed Trim (2) – (Default) PID output is applied to the speed reference as a trim value.
– Velocity reference modification applies to both vector and frequency control modes.
• Torque Excl (3) – PID output is the only reference that is applied to torque reference.
– Torque reference modification applies only to vector control modes.
• Torque Trim (4) – PID output is applied to the torque reference as a trim value.
– Torque reference modification applies only to vector control modes.