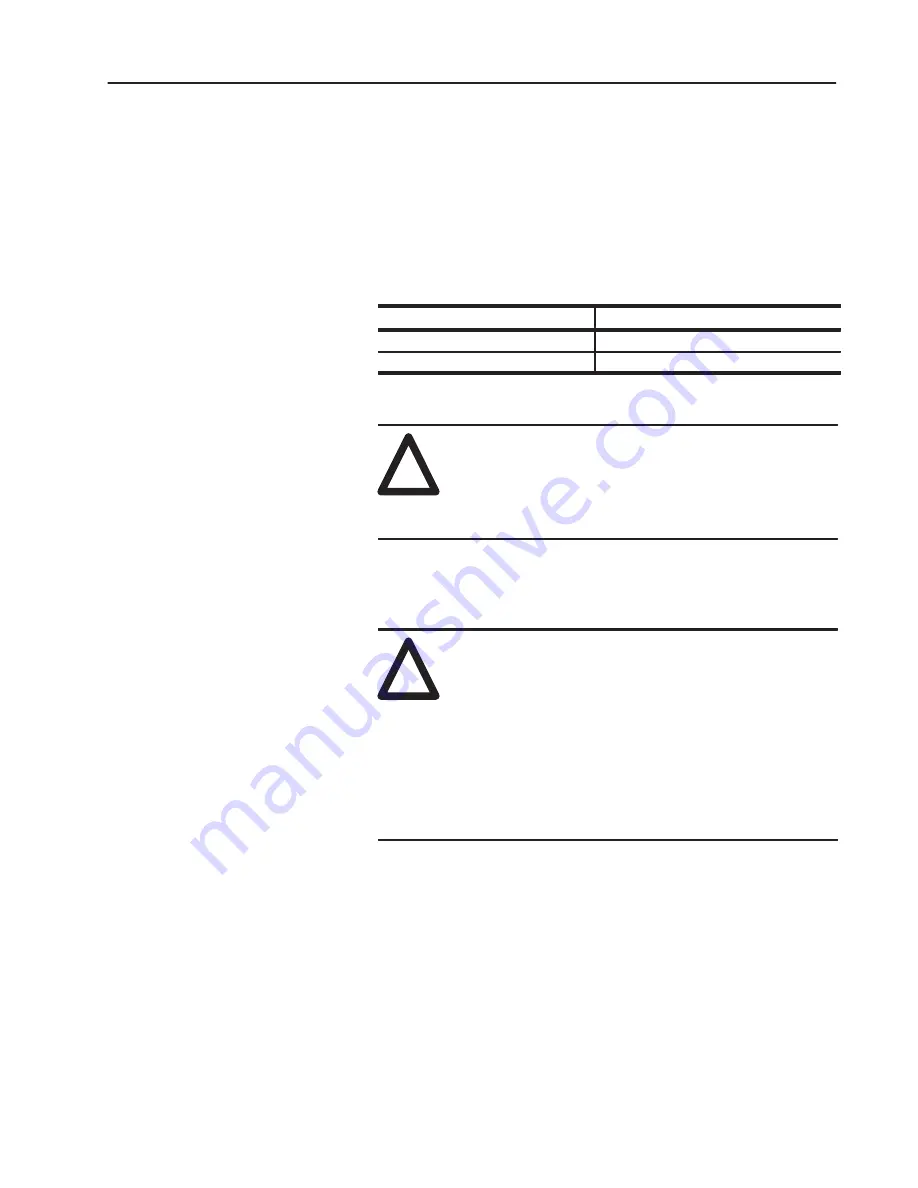
5–51
Part Replacement Procedures
Publication 1336 IMPACT-6.8 – November, 2002
Replacing Converter Diodes
The Converter Bay is configured to each order. The steps and
illustrations in this procedure are typical. Six Converter Diodes are
located on the Bridge Heat Sink in the Converter Bay.
Refer to Table 5.B for replacement diode numbers.
Table 5.B
Diode Numbers
Use this catalog number:
With:
1336-BK-SP9A
480V
1336-BK-SP10A
575V
Removal
!
ATTENTION: Wear a wrist-type grounding strap
when servicing 1336 IMPACT drives. Failure to
protect drive components against ESD may damage
drive components. Refer to Electrostatic Discharge
Precautions at the beginning of this chapter.
1. Remove power and check for zero voltage in the drive. Refer to
Opening the Drive Enclosure in Chapter 3, Access Procedures.
!
ATTENTION: Disconnect and lock out power from
the drive before disassembling the drive. Failure to
disconnect power may result in death or serious injury.
Verify zero bus voltage by measuring the voltage
between the Negative Capacitor Bus and both ends of
all three bus fuses. An open fuse does not show voltage
across both ends of the fuse. Failure to measure voltage
at both ends of the fuses may result in death or serious
injury. Refer to Figure 3.5. Do not attempt to service the
drive until the bus voltage has discharged to zero volts.
Important: Before you remove connections and wires from the
drive components, mark the connections and wires to
correspond with their component connections and
terminals to prevent incorrect wiring during assembly.
2. Remove the L-shaped bus bar that is located over the thermal
switch you need to replace. (Remove the the flex bus from the
L-shaped bus bar if necessary.)
3. Remove the two bus bars that are over the Converter Diode.
Содержание Allen-Bradley IMPACT 1336 Series
Страница 1: ...Troubleshooting Manual 1336 IMPACT Adjustable Frequency AC Drive 519 597 kW 700 800 HP ...
Страница 8: ...Table of Contents vi Publication 1336 IMPACT 6 8 November 2002 This Page Intentionally Left Blank ...
Страница 100: ...4 18 Component Test Procedures Publication 1336 IMPACT 6 8 November 2002 This Page Intentionally Left Blank ...
Страница 154: ...5 54 Part Replacement Procedures Publication 1336 IMPACT 6 8 November 2002 This Page Intentionally Left Blank ...
Страница 174: ...7 14 Schematics Publication 1336 IMPACT 6 8 November 2002 This Page Intentionally Left Blank ...
Страница 175: ...Notes Publication 1336 IMPACT 6 8 November 2002 ...
Страница 176: ...N 2 Publication 1336 IMPACT 6 8 November 2002 ...
Страница 177: ...N 3 Publication 1336 IMPACT 6 8 November 2002 ...
Страница 178: ...N 4 Publication 1336 IMPACT 6 8 November 2002 ...
Страница 179: ...N 5 Publication 1336 IMPACT 6 8 November 2002 ...
Страница 180: ...N 6 Publication 1336 IMPACT 6 8 November 2002 ...
Страница 181: ...N 7 Publication 1336 IMPACT 6 8 November 2002 ...
Страница 182: ...N 8 Publication 1336 IMPACT 6 8 November 2002 ...
Страница 183: ...N 9 Publication 1336 IMPACT 6 8 November 2002 ...
Страница 184: ...N 10 Publication 1336 IMPACT 6 8 November 2002 ...
Страница 185: ...N 11 Publication 1336 IMPACT 6 8 November 2002 ...
Страница 186: ...N 12 Publication 1336 IMPACT 6 8 November 2002 ...
Страница 187: ...N 13 Publication 1336 IMPACT 6 8 November 2002 ...
Страница 188: ...N 14 Publication 1336 IMPACT 6 8 November 2002 ...
Страница 194: ...Index I 6 Publication 1336 IMPACT 6 8 November 2002 This Page Intentionally Left Blank ...
Страница 195: ......