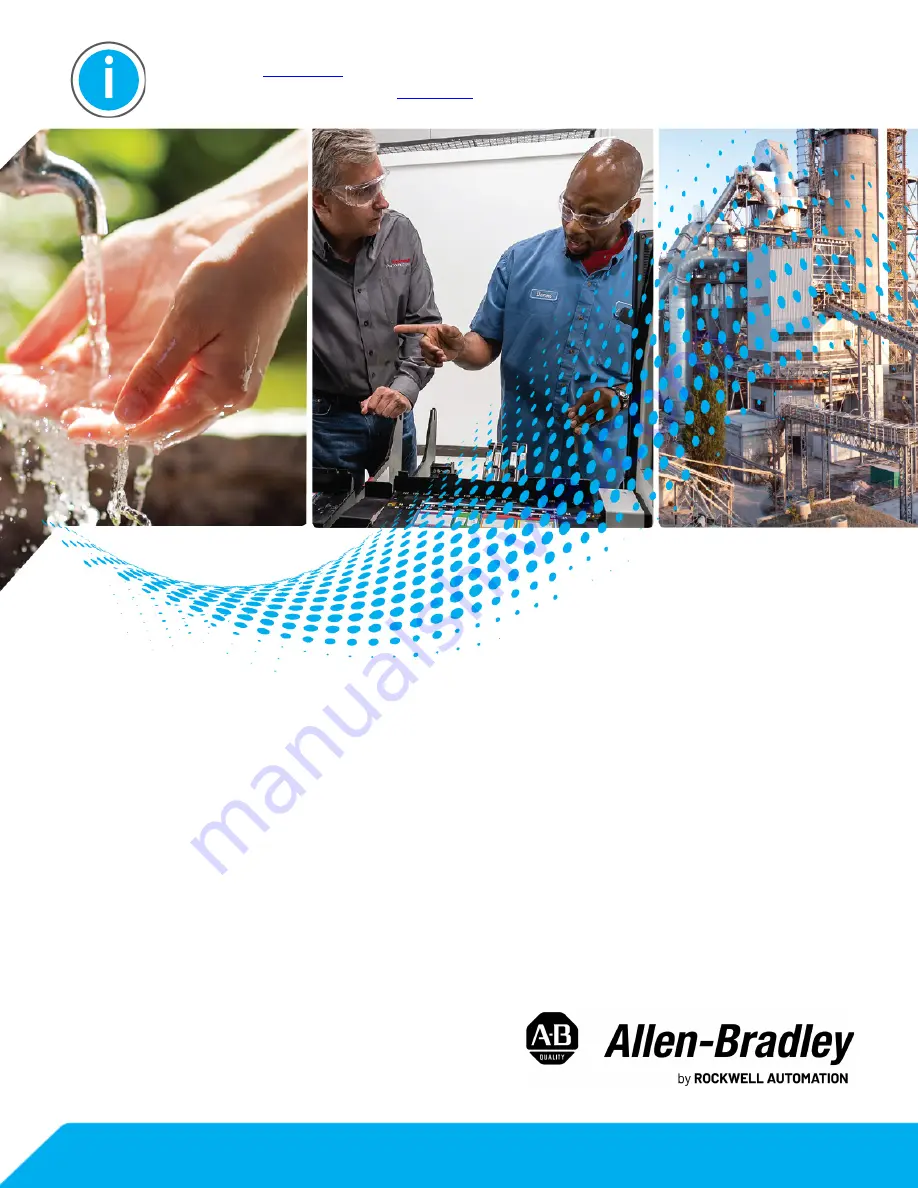
User Manual
Original Instructions
Armor PowerFlex AC Drives
Bulletins 35E, 35S
This manual links to Armor PowerFlex AC Drive Fault Codes Reference Data,
publication
and to Armor PowerFlex AC Drive CIP Objects and Attributes
Reference Data, publication
; download the spreadsheet now for offline
access.