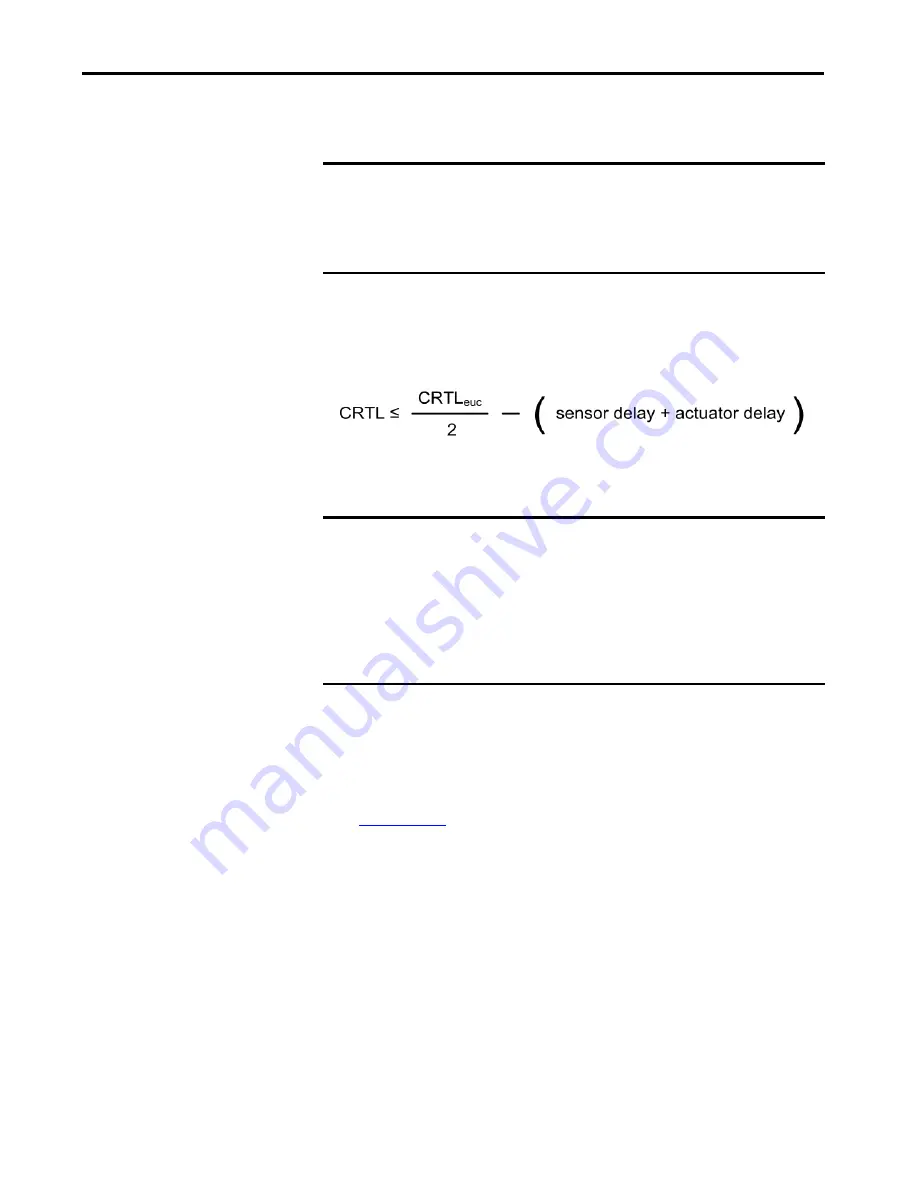
Rockwell Automation Publication 1715-RM001A-EN-P - June 2019
35
Using 1715 Hardware in a ControlLogix SIL 2 System
Chapter 4
In a 1715 system, the CRTL value is assigned to individual modules during
module configuration.
Use the following method to confirm whether the default value is acceptable or
you must change the CRTL value for your application.
This equation governs the value of CRTL for the I/O connections:
Setting up 1715 SIL 2 Periodic Task Configuration
The most important recommendation is that the task period be set at a rate that
allows the overall process safety time of the safety function to be met. See Table
48 in
for the no fault worst case reaction time formula.
• In the ControlLogix task configuration dialog, set the task period
according to the project needs and consider the following:
a. Leave time for other controller tasks to complete. Even if you do not use
any other tasks there are still other internal tasks running, like
communications. In other words, if the SIL 2 periodic task is set too
low, it is possible to use up all the processing time.
b. The advantage of a lower task period is that it increases the number of
times the Add-On Instruction is scanned; thus processing packets at a
faster rate.
IMPORTANT
It is recommended that the CRTL remain at the default of four times the RPI so
that one invalid packet does not put the system into the safe state. For
example, if the RPI = 120 ms, then consider 480 ms as the minimum CRTL. The
information in the next section helps determine the maximum setting for the
CRTL.
TIP
CRTLeuc is the process safety time for the equipment under control (euc).
EXAMPLE
Consider a system function using one sensor and one actuator given the
following parameters.
• CRTLeuc: 10,000 ms
• Sensor Delay: 250 ms
• Time for actuator (an ESD valve) to fully operate: 1750 ms
In this example, the setting of CRTL for the I/O connections is less than or equal
to 3000 ms.