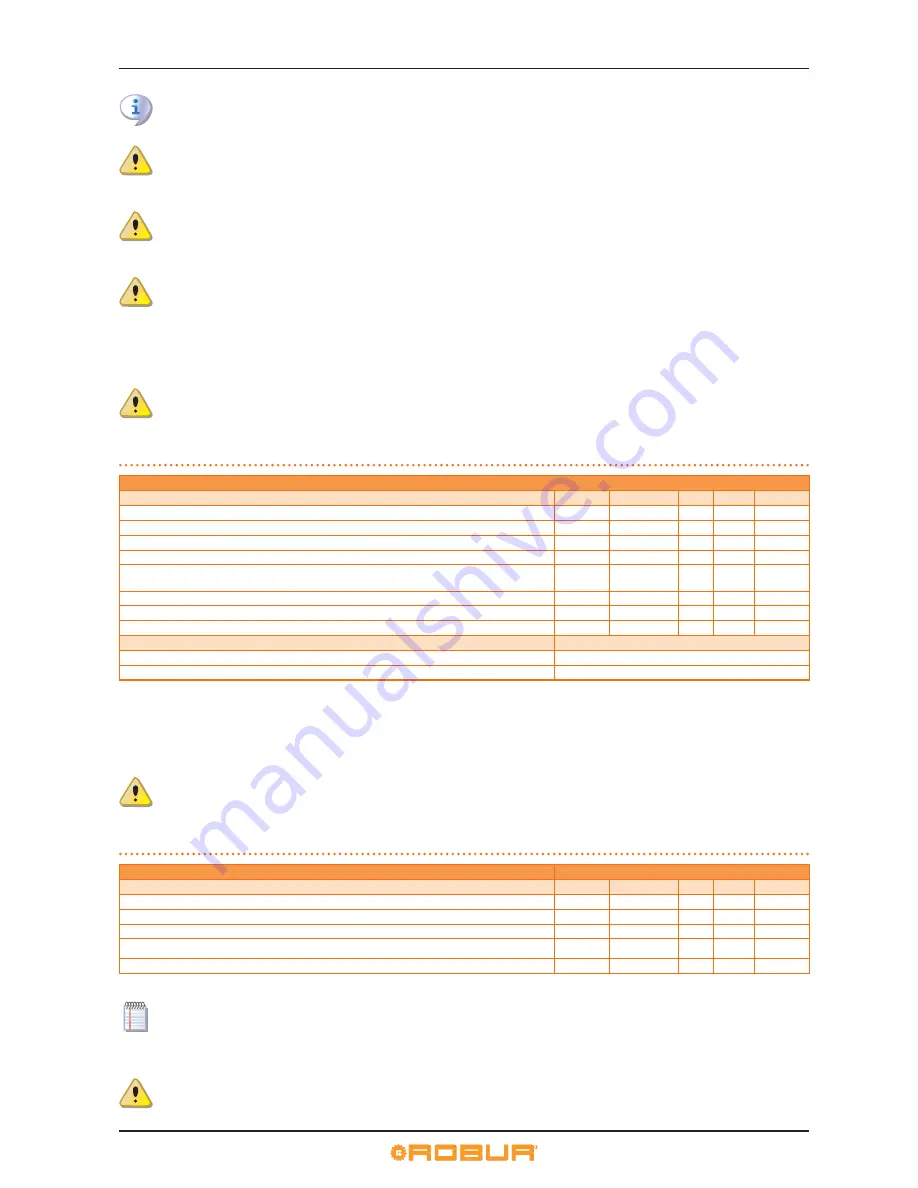
7
INITIAL ACTIVATION AND MAINTENANCE
54
Any operation that regards internal components of units of the appliance must be carried out by an authorized Robur Tech-
nical Assistance Centre (TAC), according to the instructions supplied by the manufacturer.
The "efficiency check" and every other "check and maintenance operation" (see Table 7.2
→
54 and 7.3
→
54), must be per-
formed with a frequency in agreement to current law or, if more restrictive, in respect of what requested by the planner
(builder of the system) or by the manufacturer of the unit.
The liability of CHECKING THE EFFICIENCY AS A FUNCTION OF THE SYSTEM, OF THE FUEL IN USE AND OF THE THERMAL
POWER, to be carried out with the purpose of containing the energy consumption, is in charge to the responsable of the
system.
Before carrying out any operation on the appliance, switch it off via the appropriate on/off command (or via the DDC, if con-
nected and in controller mode) and wait for the shutdown cycle to terminate. When the appliance is off, disconnect it from
the gas and electricity mains, bearing in mind the antifreeze settings, via the external circuit breaker (GS) and the gas valve.
GUIDELINES FOR THE PREVENTIVE MAINTENACE OPERATIONS
In Table 7.2
→
54 are reported the guidelines for the preventive maintenance operations.
If the unit is subject to particularly heavy duty (for example in process plants or in other conditions of continuous opera-
tion), these maintenance operations must be more frequent.
Table 7�2
GUIDELINES FOR THE PREVENTIVE MAINTENACE OPERATIONS
Check of the unit
GAHP-A
GAHP-GS/WS
AY
ACF
GAHP-AR
Visually check of the general condition of the unit and of its air heat exchanger.
(1)
√
√
√
√
Check the correct operation of the device used for monitoring the water flow
√
√
√
√
√
Check the % value of CO
2
√
√
√
check gas pressure to the burners
√
√
Check that the condensate discharge is clean (clear the condensate discharge hole of any blockages)
[If necessary, frequency of the maintenace operation must be increased]
√
√
√
Replace the belts after 6 years or 12,000 hours of operation
√
√
√
√
Check/restore the pressure of the primary hydronic circuit
√
Check/restore the air pressure inside of the expansion vessel of the primary hydronic circuit
√
Check every CCI or DDC(2)
DDC o CCI
Check that the plant is able to achive the setpoint temperature
√
Download the hystorical events
√
1 - It is suggested the cleaning of the air heat exchanger once every 4 years [the optimal frequency of this operation is in any case a consequence of
the installation site].
2 - Check that the plant is able to achive the setpoint temperature.
ORDINARY SCHEDULED MAINTENANCE
Perform the following operations at least once every 2 years.
If the unit is subject to particularly heavy duty (for example in process plants or in other conditions of continuous opera-
tion), these maintenance operations must be more frequent.
Table 7�3
SCHEDULED MAINTENANCE OPERATIONS
TO BE PERFORMED AT LEAST ONE EVERY TWO YEARS
Check of the unit
GAHP-A
GAHP-GS/WS
AY
ACF
GAHP-AR
Clean the combustion chamber
√*
√*
√
√
√*
Clean the burner
√*
√*
√
√
√*
Clean the electrodes of ignition and flame sensing
√
√
√
√
√
Check that the condensate discharge is clean (clear the condensate discharge hole of any blockages)
√
√
√
Replace the silicone gasket
√
*Only in case the analysis of combustion products is non-compliant
In Section 5
→
18 are reported suggestions related to the hydraulic plant.
7�3
CHANGE OF GAS TYPE
The following procedure must be done by a Robur TAC or professionally qualified technician.