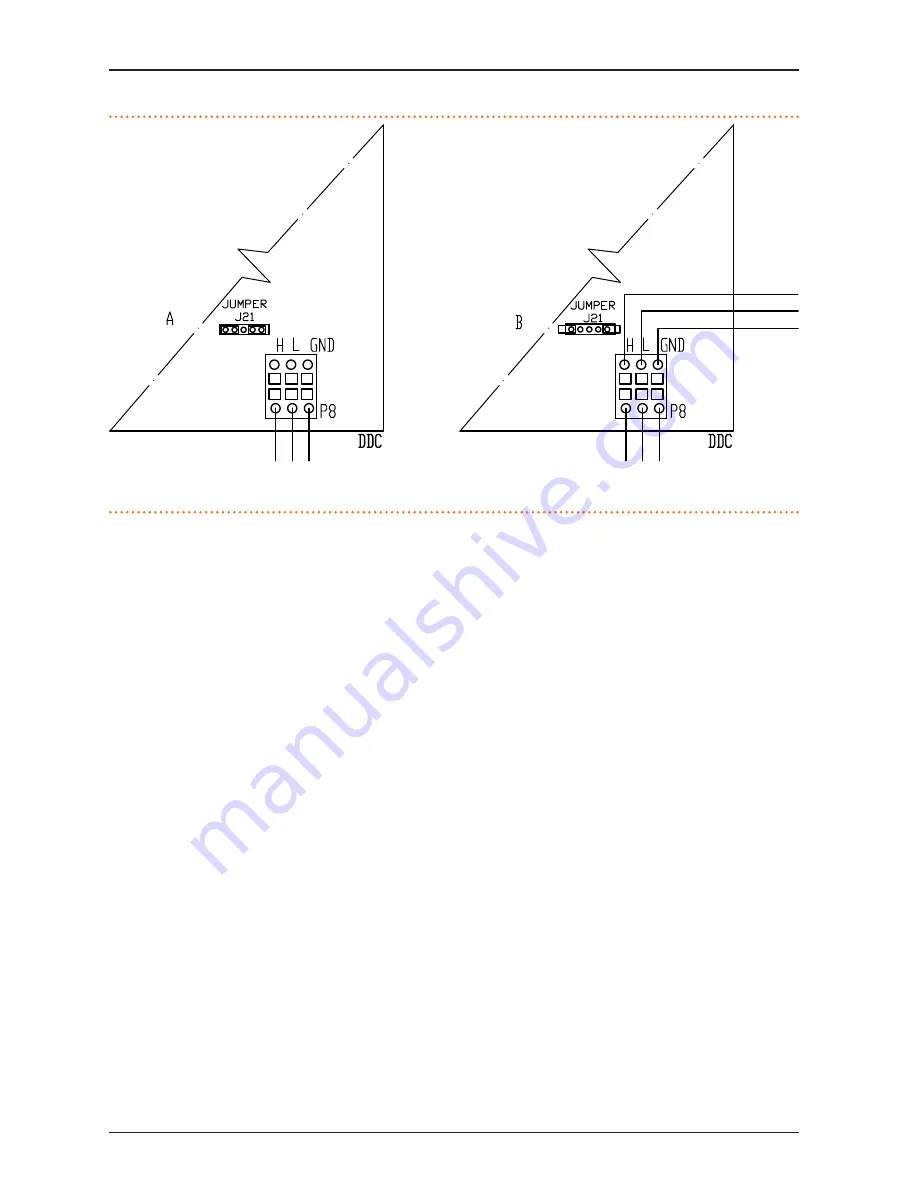
6
ELECTRICAL INSTALLATION
Installation, user and maintenance manual – AY Condensing line, AY Series
45
Figure 6�14 – detail wires and jumpers J21 - terminal/intermediate node CCI/DDC
Detail terminal and intermediate node: jumpers position J21: "closed" - "open".
LEGEND
DDC
CCI/DDC
J21
Jumper CAN-BUS in CCI/DDC board
A
detail case "terminal node" (3 wires; J21=jumper "closed")
B
detail case "intermediate node" (6 wires; J21=jumper "open")
H,L,GND
data signal wires
2.
Prepare the orange connector (remove from envelope).
3.
Cut a length of cable, long enough to allow it to be installed without kinking.
4.
Having chosen one end of the length of cable, remove the sheath from a length of approximately 70-80 mm, taking care not
to cut the wires contained inside, the shielding (metallic shield and/or aluminium sheet) and, if present, the bare connector in
contact with the shield and the wires contained within.
5.
Roll the shielding and connect it to a 4-mm eyelet terminal, as illustrated in Figure 6.13
→
44, details C and D. Now proceed as
follows:
6.
Connect the three coloured wires to the orange connector, as shown in detail "A" in the figure. Observe the terminal markings
L, H, GND (on the DDC at the base of the socket "P8") which are given both in Table 6.2
→
43, and in the figure:
▶
if the DDC is an intermediate node on the network, also complete step "7";
▶
if the DDC is a terminal node, skip directly to step "8".
7.
Intermediate nodes only: repeat the operations from step "1" to step "4" for the other length of CAN bus cable required. Now
proceed with step "5" and, to connect the cable to orange connector, refer to detail "B" in the figure. Then proceed to point "8".
8.
Fit the orange connector, with the wires attached, first through the slot in the DDC’s cover and then into the socket on the
DDC itself.
9.
Use the rear cover bolts located near the CAN BUS socket to secure the 4-mm eyelet (or 2 eyelets) (detail D, Figure 6.13
→
44).
The cable should be secured against pulling out.
Step B: connect the CAN-BUS cable to the appliance
The CAN BUS cable must be connected to the orange socket on the machine’s on-board controller (see detail "D" in Figure 6.15
→
46).