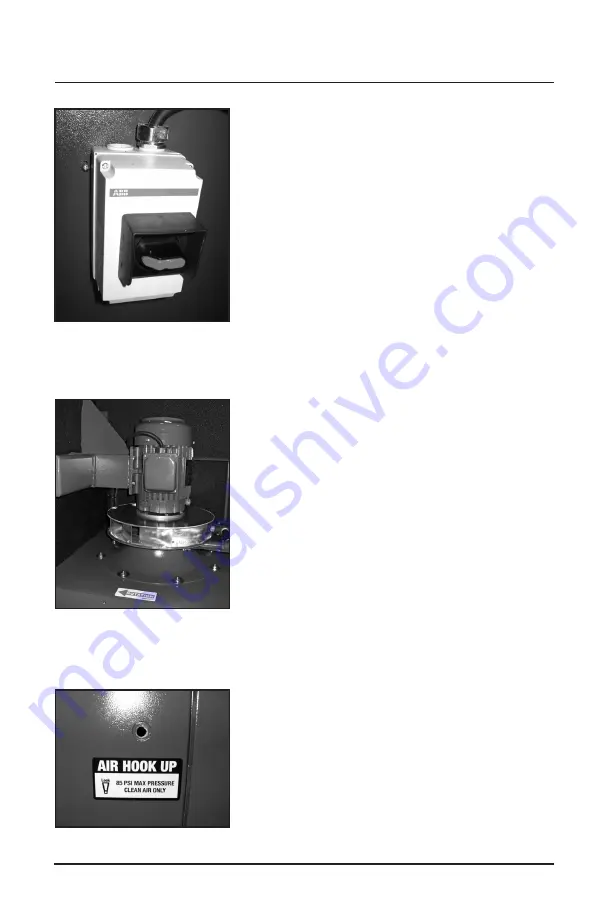
VENTBOSS
•
SERIES 300 SPACE SAVER COLLECTORS OWNER’S MANUAL
13
SECTION 500
INSTALLATION
FIGURE 3
Electrical Hook Up
To operate your new VentBoss Series 300 collector, you
will simply need to place it in positon and connect your
460 Volt, 3 phase power supply to the provided Electrical
Disconnect shown (Figure 3).
Electrical connections should only be done by a
licensed electrician and in accordance with NEC and all
applicable local codes.
IMPORTANT:
when the motor is started for the first time,
it is essential that the direction of the blower wheel is
checked. (Figure 4) When looking down through the
outlet grille on the top of the unit, the blower wheel
must be rotating in a clockwise direction, also shown
by a sticker adjacent to the blower wheel. If it is
running in reverse, air will still be drawn through, but
at a fraction of the designed volume, and will produce
excessive noise and potentially vibration. To correct
this reverse rotation of the blower wheel, swap the
terminal attachment position on 2 of the 3 phase wires
connected to the Disconnect.
Amperage requirements of all models are found in the
Equipment Specifications Sheets.
Compressed Air Hook-Up
IMPORTANT!
The VentBoss unit needs a clean, oil-free,
dry compressed air source, 85 PSI MAXIMUM.
Many problems can be traced back to the presence
of oil or water in the compressed air system. If
contamination is present, both the filter cartridges and
pulse cleaning system will be damaged.
An appropriately sized quick fit air-line connector will
need to be threaded into the provided 1/2” NPT adapter.
A permanent line can be directly connected to the accu-
mulator tank or a shop air hose can be used when pulse
cleaning the filters. (Figure 5)
FIGURE 4
FIGURE 5
Содержание VentBoss 300 Series
Страница 2: ......
Страница 20: ......
Страница 21: ...APPENDIX A FUME ARM INSTALLATION OPERATION MAINTENANCE ...
Страница 32: ... 2017 RoboVent 37900 MOUND ROAD STERLING HEIGHTS MICHIGAN 48310 USA 855 558 VENT WWW VENTBOSS COM ...