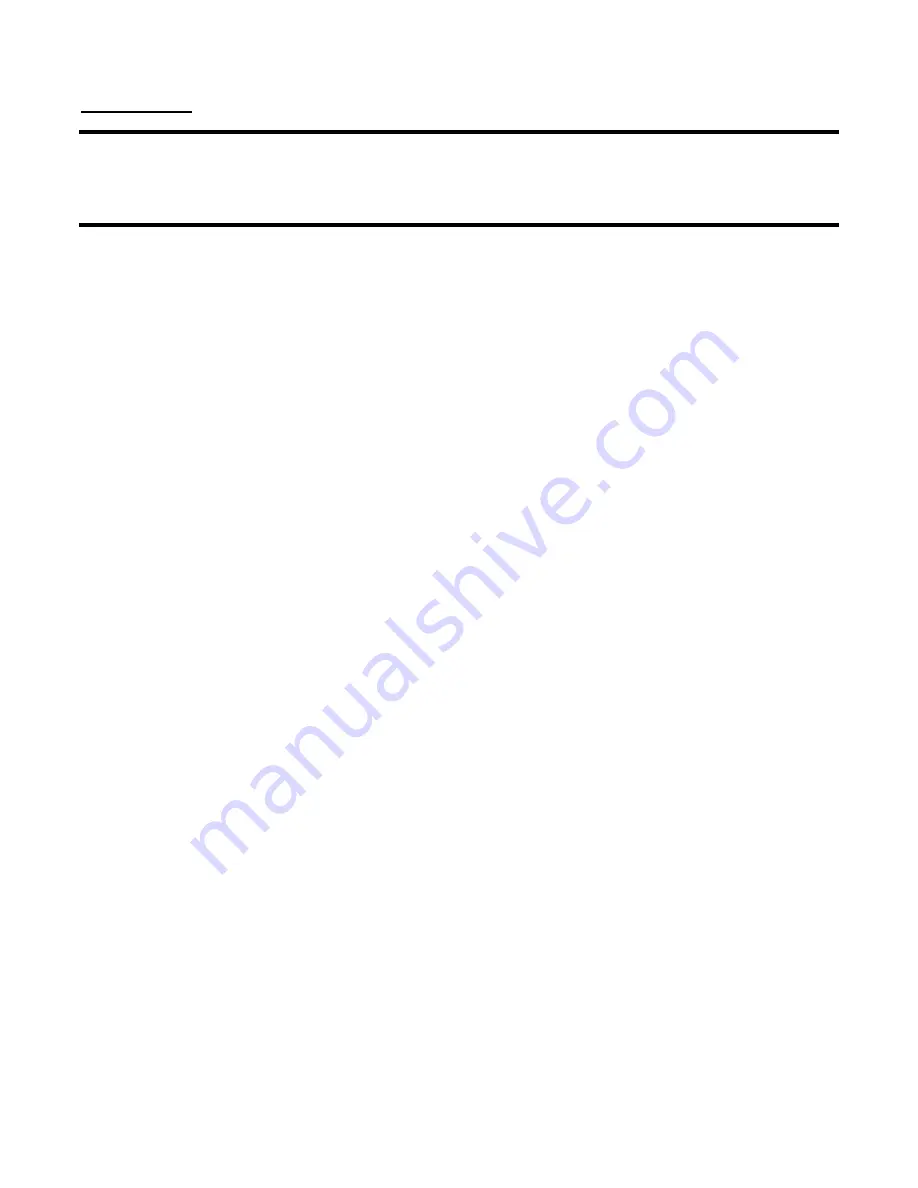
EPV SERIES CONDENSING WATER BOILER
34-501 07/13
16
MAINTENANCE
CARBON MONOXIDE WARNING: An annual or seasonal combustion checkout must be performed by a
qualified service agency to ensure safe operation. Failure to maintain proper combustion can result in
injury or death.
CAUTION: Be sure manual valves and burner electrical switch are turned off before removing any part for
service or cleaning. Do not push relay contacts in manually; accidental opening of main automatic valve
can result. Ensure there is no pressure on the vessel prior to disassembly of any water carrying
component to prevent serious injury.
1.
A preventive maintenance is recommended to assure a long, trouble-fee life of the boiler. Refer to ASME
Section VII for a comprehensive plan for boiler operation, maintenance and lay-up.
A table of periodic safety inspections is attached to this manual for ease of reference by the building
service technician or licensed equipment operator (Table 501-2, page 19). Since boiler designs vary,
only some of these listed inspections may be appropriate for your particular model.
2.
Proper water treatment is critical to prevent corrosion as well as to reduce scale, both of which will reduce the
life of the boiler. Hydronic heating systems, steam heating systems and process steam systems all have
different treatment requirements. The makeup of the water, just as the blowdown, will vary with each
application. Rely on the recommendation of the water consultant.
SINCE RIVERSIDE HYDRONICS CANNOT CONTROL THE USE OF THE BOILER, WATER CONDITIONS OR
MAINTENANCE, THE WARRANTY ON THE BOILER DOES NOT COVER POOR PERFORMANCE,
STRUCTURAL FAILURE OR LEAKING DUE TO AN EXCESSIVE ACCUMULATION OF SCALE. HOWEVER,
SHOULD A FIRETUBE LEAK FOR ANY REASON, CONSULT THE FACTORY FOR INSTRUCTIONS.
3.
Examine the venting system at least monthly for proper connections, alignment, or the presence of corrosion.
If corrosion appears, the boiler must not be operated until the corroded vent section(s) is replaced.
4.
Oil the blower motor and wipe oil and dust from the burner at regular intervals. The static fan will collect dust
from the air during operation. Clean the screen and fan blades if necessary. The burner should be cleaned
each year. Inspect all parts and make replacements when necessary. Check wiring for loose connections and
burned wires.
WARNING: Turn off all electrical service to the appliance when accessing the controls located inside the
control cabinet. The cabinet contains high voltage wiring and terminals. If the electrical service is not
turned off and these wires or terminals are touched, a dangerous shock causing personal injury or loss of
life could occur. Close the control cabinet before restoring electrical service to the appliance.
5.
Periodic inspections and check-out of the burner ignition system, control system and fuel valve operation (for
tight close-off) should be made. Refer to the burner installation instructions for inspection recommendations.
6.
Inspect operating controls to ensure they are level, especially those containing mercury switches. Make sure
connecting tubing is not kinked or damaged on remote bulb thermostats.
7.
The pressure safety valve should be checked at regular intervals by manually opening the valve. The openings
inside the valve may become restricted by a buildup of scale and become inoperative. If the valve does not
open and close properly, it must be replaced. Shut down boiler, relieve internal pressure, and replace safety
valve with a like kind or one meeting the requirements stated on the rating decal located adjacent to the safety
valve mounting location.
CAUTION: The safety valve is a
primary
safety device.