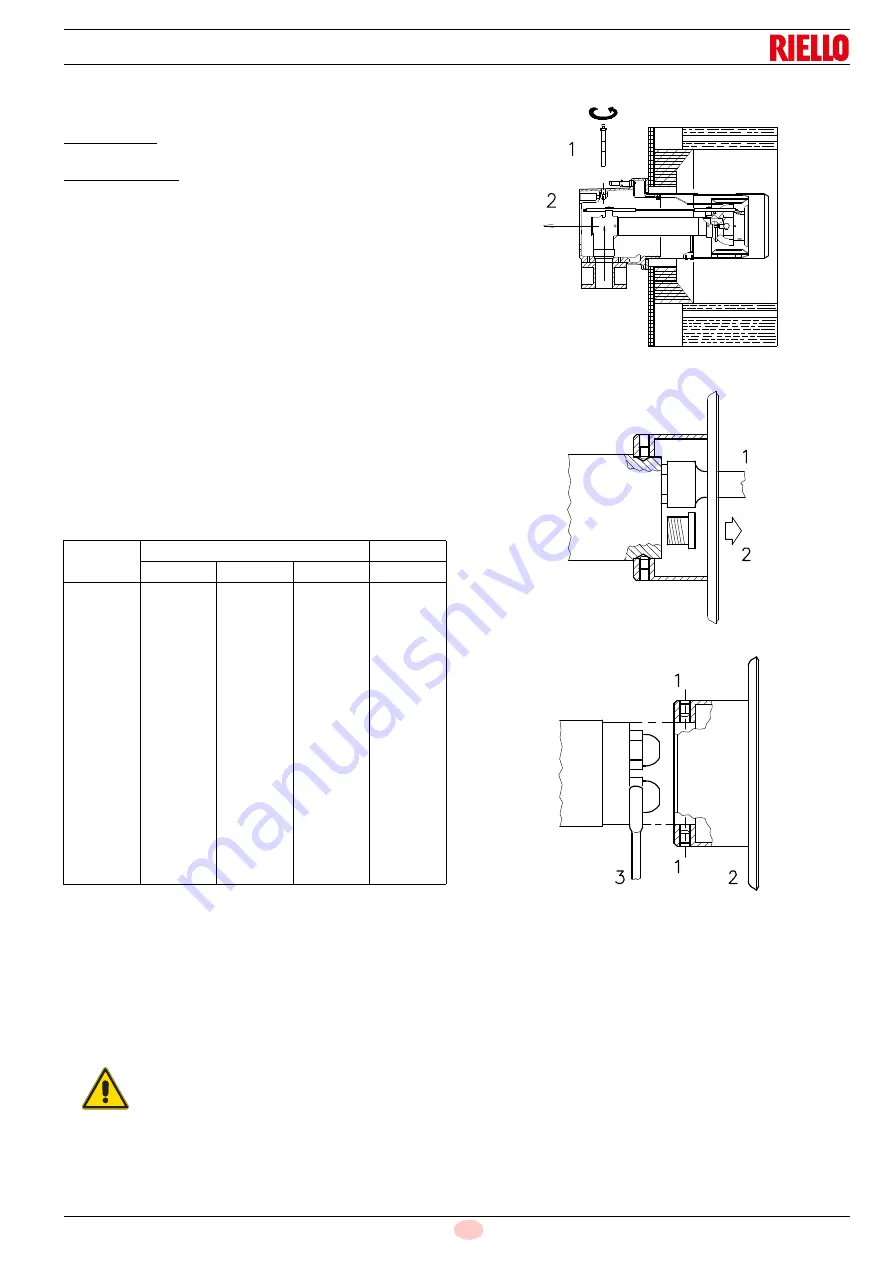
17
20034293
GB
Installation
5.8.1
Choice of nozzles for 1
st
and 2
nd
stage
Both nozzles must be chosen from among those listed in Tab. J.
The first nozzle determines the delivery of the burner in the 1st
stage.
The second nozzle works together with the 1st nozzle to deter-
mine the delivery of the burner in the 2nd stage.
The deliveries of the 1st and 2nd stages must be contained within
the value range indicated on pag. 9.
Use nozzles with a 60° spray angle at the recommended pres-
sure of 12 bar.
As a rule the two nozzles have equal deliveries but the 1st stage
nozzle may have a delivery less than 50% of the total delivery
when a reduction of the counter-pressure peak is desired at the
moment of starting (the burner allows good combustion rates
also with a 40 - 100 % ratio between the 1st and 2nd stage).
Example
Boiler output = 1630 kW - efficiency 90 %
Output required by the burner:
1630 : 0.9 = 1812 kW
per nozzle:
1812 : 2 = 906 kW
therefore, two equal, 60°, 12 bar nozzles are required:
1° = 18 GPH - 2° = 18 GPH,
or the following two different nozzles:
1° = 16 GPH - 2° = 20 GPH
Nozzle DELAVAN B 60°
Tab. J
5.8.2
Nozzle assembly
Remove screw 1)(Fig. 11) and extract the internal part 2).
Fit two nozzles with the box spanner (16 mm) 1)(Fig. 12),
after having removed the plastic plugs 2).
Fitting the spanner through the central hole in the flame sta-
bility disk or loosen screws 1)(Fig. 13).
Remove disk 2)(Fig. 13) and replace the nozzles using the
wrench 3).
The nozzle for the 1
st
stage of operation is the one lying beneath
the firing electrodes (Fig. 14).
GPH
kg/h
kW
10 bar
12 bar
14 bar
12 bar
12.0
13.0
14.0
15.0
16.0
17.0
18.0
19.0
20.0
22.0
24.0
25.0
26.0
28.0
30.0
32.0
34.0
35.0
44.16
47.84
51.52
55.20
58.88
62.57
66.25
69.93
73.61
80.97
88.33
92.00
95.69
103.05
110.41
117.77
125.13
128.81
48.73
52.79
56.86
60.92
64.98
69.04
73.10
77.16
81.22
89.34
97.47
101.53
105.59
113.71
121.83
129.95
138.08
142.14
52.96
57.38
61.79
66.20
70.62
75.03
79.44
83.86
88.27
97.10
105.93
110.34
114.75
123.58
132.41
141.24
150.06
154.48
582.36
630.89
679.42
727.95
776.48
825.01
873.54
922.07
970.60
1067.66
1164.72
1198.00
1261.78
1358.84
1455.90
1533.47
1629.31
1667.23
WARNING
Do not use any sealing products such as gaskets,
sealing compound, or tape.
Be careful to avoid damaging the nozzle sealing
seat. The nozzles must be screwed into place
tightly but not to the maximum torque value pro-
vided by the wrench.
Fig. 11
D3172
Fig. 12
D1146
Fig. 13
D1147
Содержание RLS 250/M
Страница 2: ...Original instructions ...
Страница 45: ...43 20034293 GB Appendix Electrical panel layout ...
Страница 46: ...20034293 44 GB Appendix Electrical panel layout ...
Страница 47: ...45 20034293 GB Appendix Electrical panel layout ...
Страница 48: ...20034293 46 GB Appendix Electrical panel layout ...
Страница 49: ...47 20034293 GB Appendix Electrical panel layout ...
Страница 51: ......